Clean-in-Place (CIP) Systems: Everything You Need to Know
CIP cleaning in place is a technique used across multiple CPG industries to clean and sanitize the processing systems used to make processed food, beverages, dairy products, pharmaceuticals, personal care products, and more. Selecting appropriate cleaning parameters is crucial in CIP systems to ensure efficient cleaning while complying with safety and environmental standards.
What is Clean-in-Place (CIP)?
Industries that produce food, beverages, and medications rely heavily on CIP systems to maintain high hygiene standards and prevent contamination. Production of consumer goods that go in or on a human body must meet strict requirements and standards based on governmental regulations.
How It Works
Clean-in-place (CIP) processes clean and sanitize the interior surfaces of pipes, vessels, process equipment, filters, and associated fittings without disassembly. It is a multi-step cleaning process that removes the remaining product from a production line, breaks down remnants, sanitizes, and rinses. CIP Clean in Place uses a circulating flow where caustics and acids can be recirculated, while rinses and sanitizers are directed to the drain. CIP systems are essential for cleaning processing equipment, including heat exchangers, to ensure efficient cleaning processes.
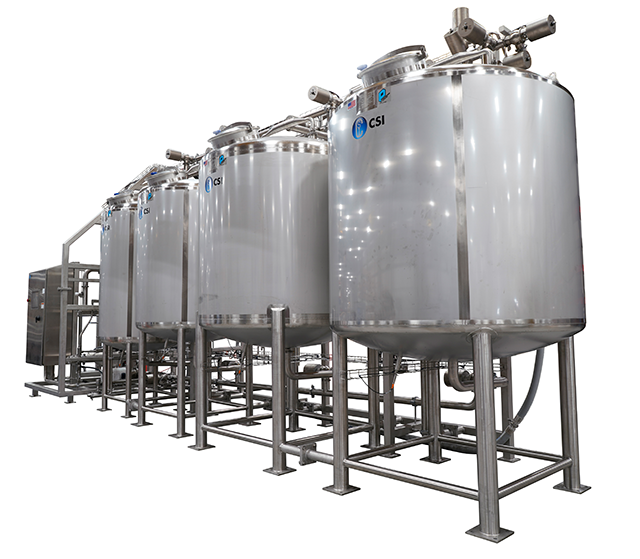
Benefits of CIP Systems
Product Safety
One of the main benefits of cleaning in place (CIP) is that it reduces human error and increases cleaning consistency by automating cleaning. Another considerable benefit is taking better care of your equipment.
Employee Safety
CIP reduces employee chemical exposure by containing cleaning solutions within the system. CIP eliminates the need for vessel entry, so employees don't have to enter tanks to clean them. This reduces the potential for injuries and improves workplace safety.
Economic and Operational Advantages
Most process environments aim to maximize quality production time and minimize other activities and costs. The more challenging the cleaning job is and the more frequent the cleaning cycle, the more cost-effective CIP can be. Some of the main economic benefits of installing a CIP system:
- More Production Time: Less production time is lost to cleaning, and more time is spent making the product.
- Product Quality: Reliable and repeatable cleaning leads to sustainable product quality and consistency, fewer recalls, and higher brand confidence.
- Lower Water Treatment Costs: Less water waste.
- Employee Efficiency: More labor time spent on productive, profitable activities.
- Utility Savings: Water and energy usage are reduced through repeatable cycle control.
CIP System Types and Design Considerations
Types of CIP Systems
Each CIP system type offers distinct advantages, allowing facilities to select a configuration that aligns with their operational needs, scale, and sustainability goals.
Based on their configuration and operational focus, there are three primary types of CIP systems:
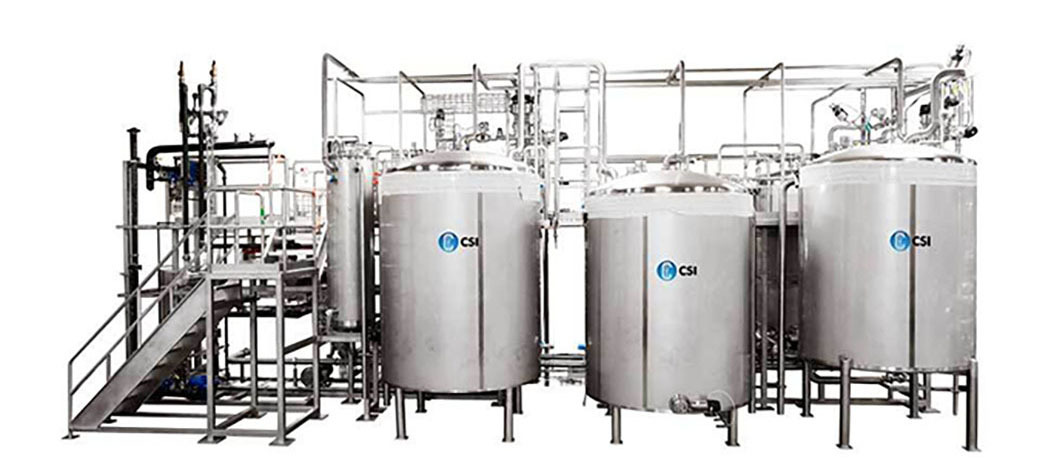
Centralized CIP Systems
These are efficient for large-scale operations. They streamline cleaning processes and reduce the need for duplicative equipment. They often feature advanced controls for monitoring and automating cleaning cycles across various process lines.
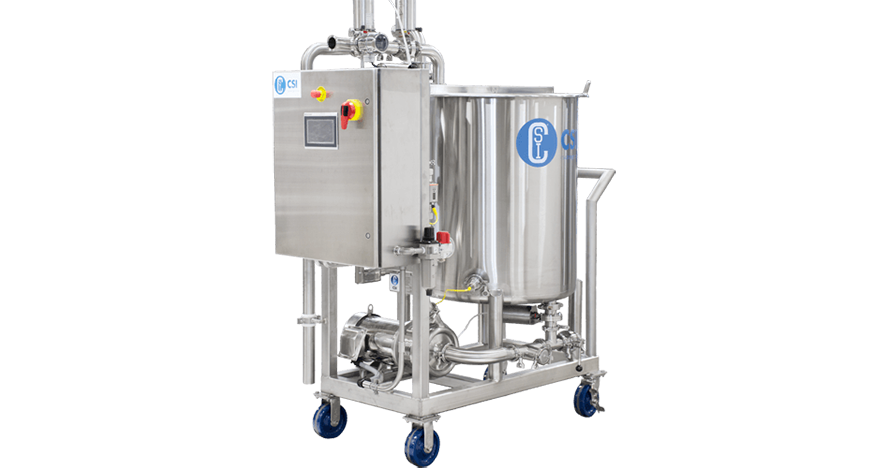
Transportable CIP Skids
These portable CIP skids can be moved to different areas as needed, making them ideal for small-scale operations, pilot plants, or facilities with space constraints. They typically feature compact designs with intuitive controls for easy operation.
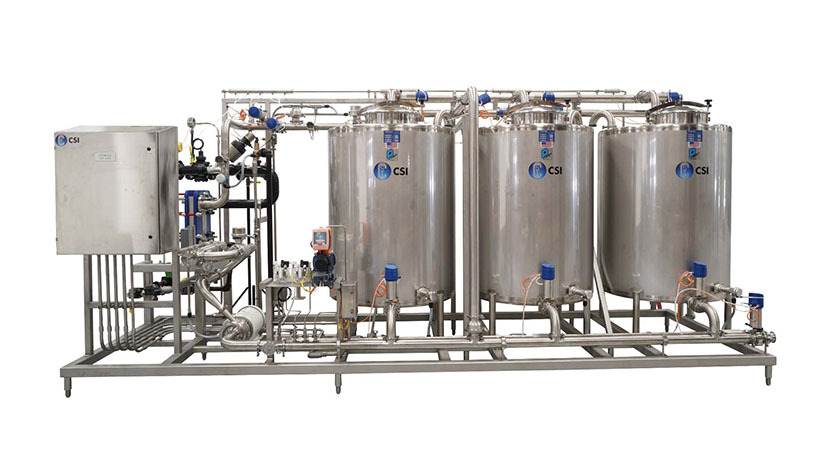
Distributed CIP Systems
Distributed systems use dedicated CIP units closer to the equipment they are designed to clean. This approach minimizes the length of piping required for cleaning solutions, reduces the risk of cross-contamination, and provides facility flexibility.
Key Design Considerations
An ideal CIP system design should consider the specific needs of your overall operation and unique equipment requirements. To ensure effective cleaning and sanitation, it is crucial to design CIP systems that cater to the specific needs of processing equipment. Automated CIP systems optimize cleaning efficiency and reduce manual cleaning, offering cost savings and safety improvements over manual cleaning. Considerations should include:
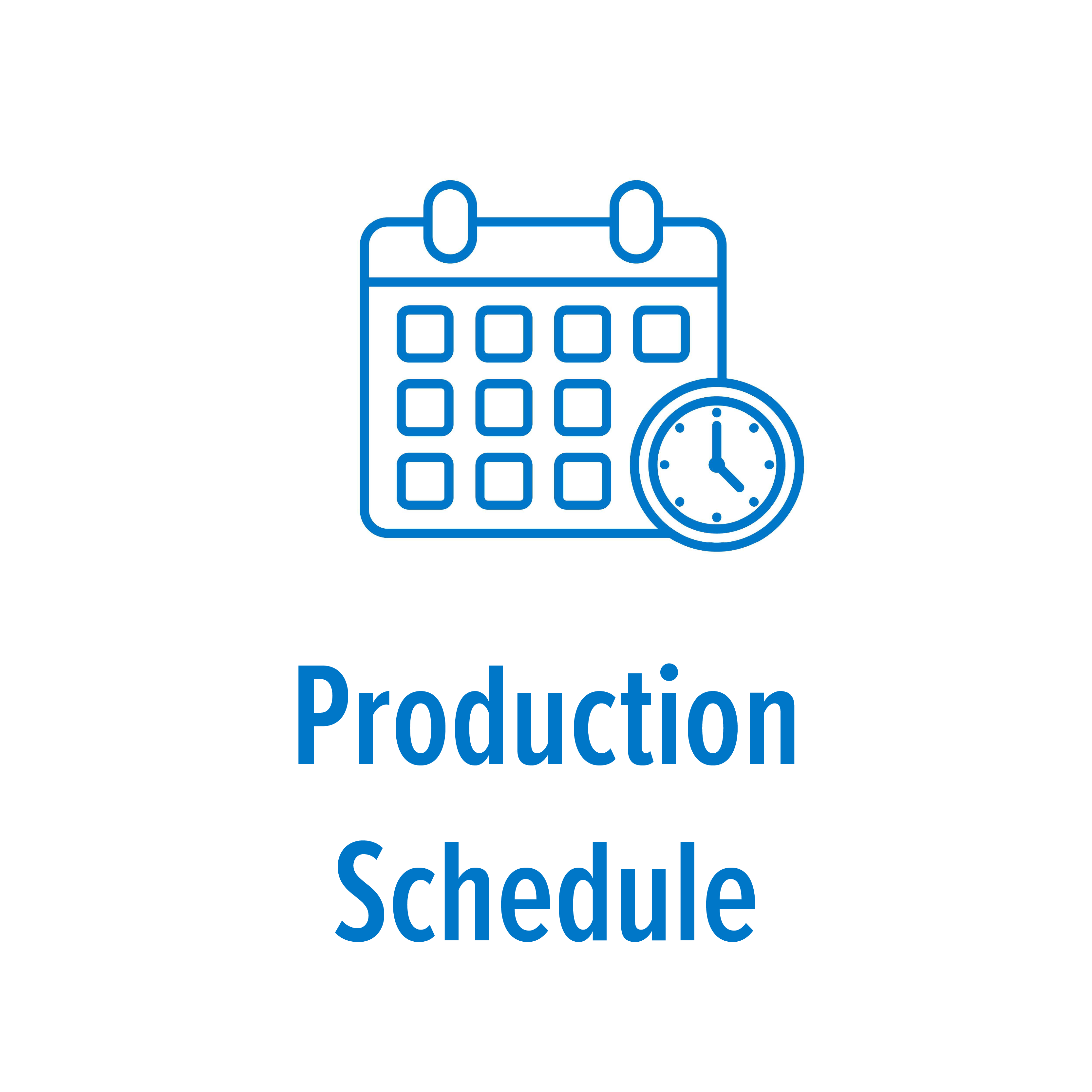
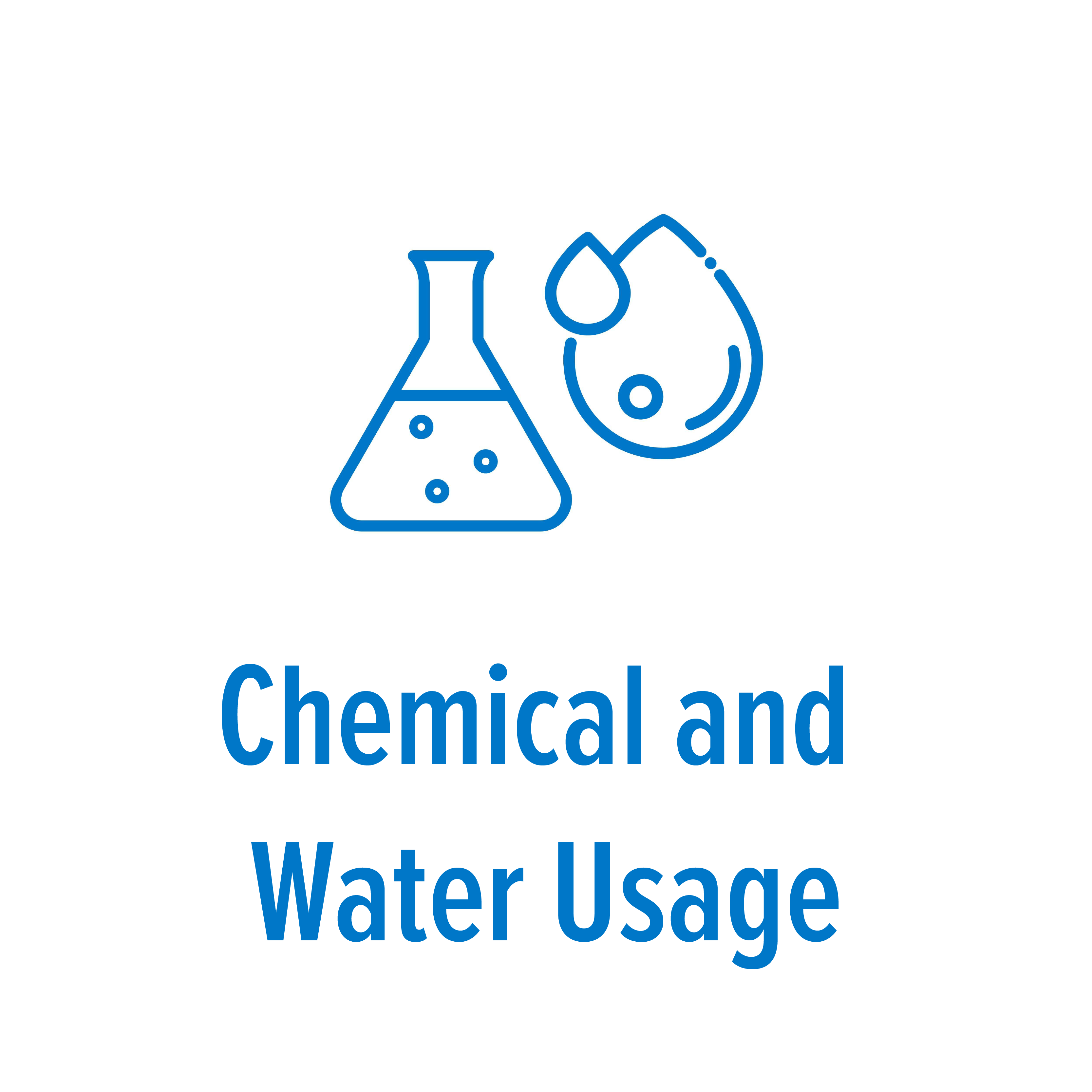
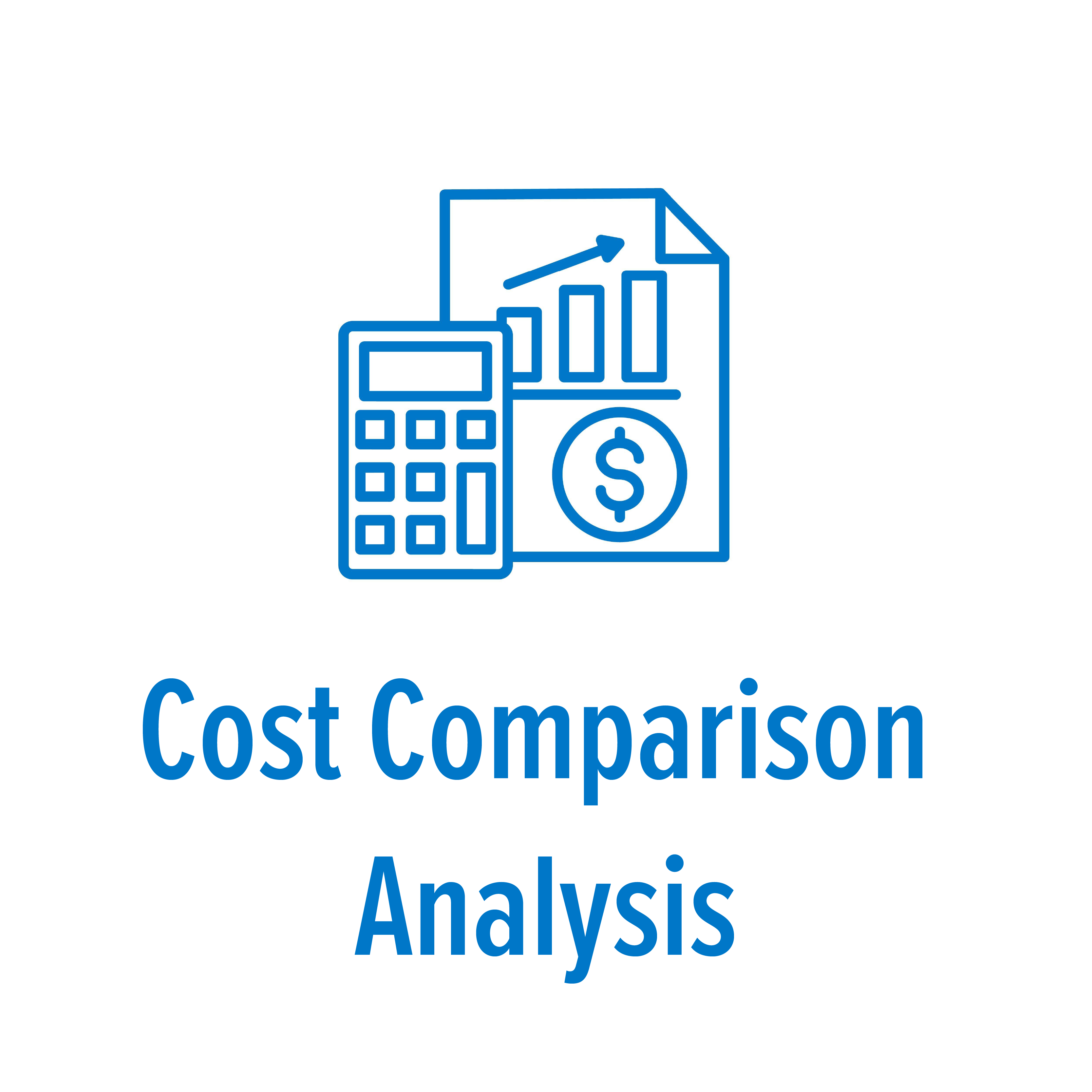

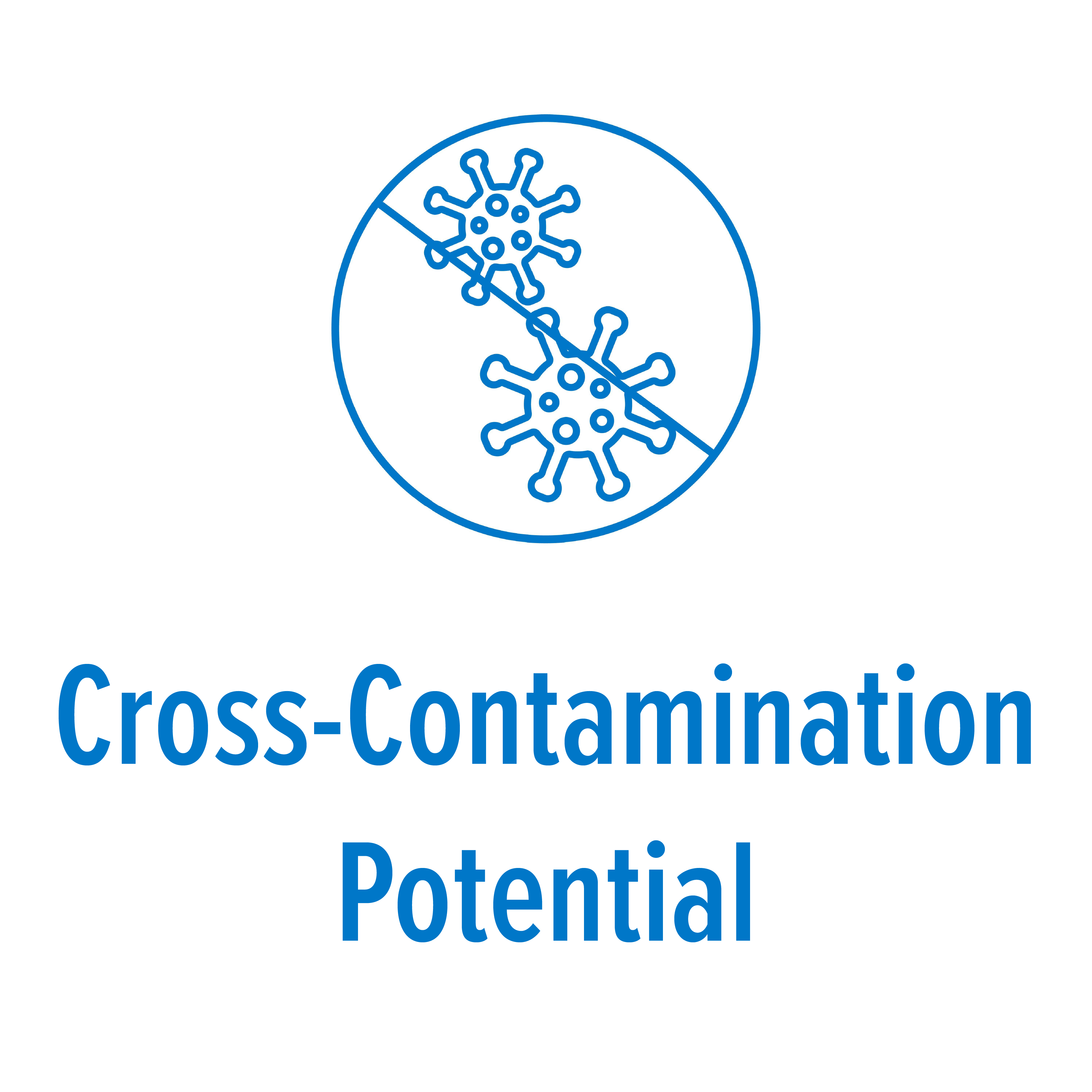
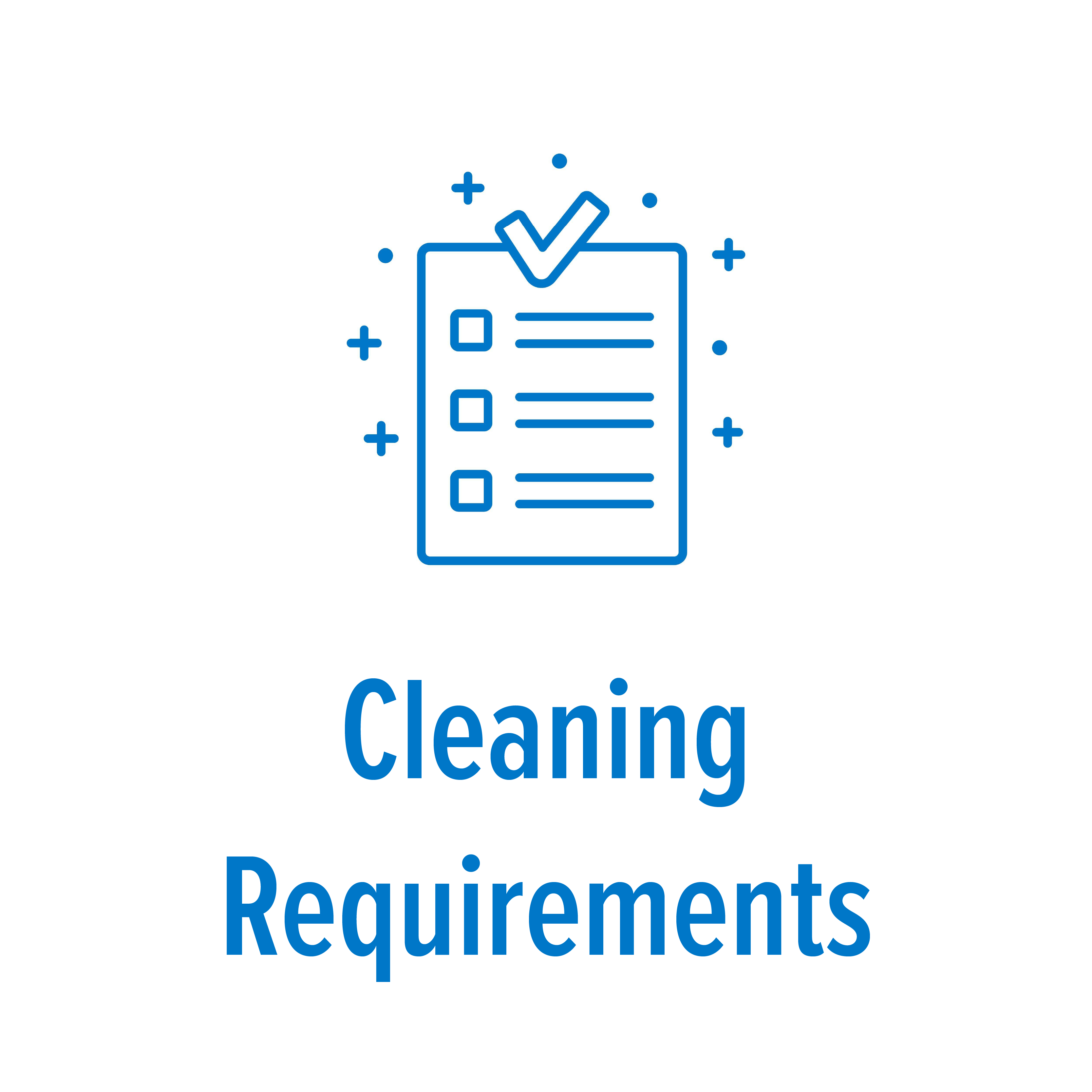
Components of a CIP System
CIP systems have many components, including chemical storage, solution supply and recovery tanks, pumps, spray, and control devices, all crucial in managing cleaning fluids. They can be designed to accommodate different types of equipment and processing lines to minimize labor and reduce water and chemical consumption.
Pumps and Valves
A pump's job is to ensure the proper velocities needed to clean process lines and equipment and the fluid pressure for the spray devices. Ensure you pick the correct pump to be most efficient for your process.
CIP Supply Pump (Clean-in-Place Pump)
The CIP supply pump, or CIP pump, delivers cleaning solutions to the system, ensuring:
- Adequate Flow: Provides the turbulence needed to remove residues effectively.
- System Pressure: Maintains pressure to circulate cleaning solutions through equipment.
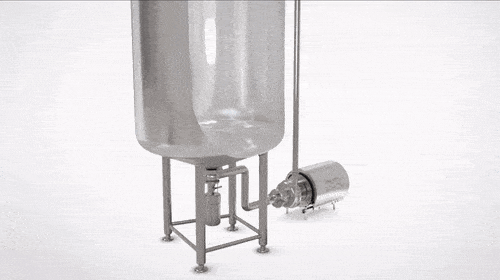
CIP Return Pump
In Clean-in-Place (CIP) systems, the return pump is crucial in efficiently recovering and recirculating cleaning solutions. Its primary function is transporting used cleaning agents from the process equipment back to the CIP system for reuse, thereby minimizing chemical waste, heat loss, and water usage.
A common challenge in CIP return lines is the presence of air or gas within the cleaning solutions, which can lead to issues like cavitation—a phenomenon where vapor bubbles form and collapse, potentially causing damage to pump components. Liquid ring and self-priming pumps can be employed to address this due to their ability to handle mixtures of air and liquid effectively. These pumps can achieve a fully primed condition even when air is entrained in the cleaning solution, making them particularly suitable for CIP return applications.
The TrueClean® Air Eliminator is an effective solution for removing trapped air in CIP return lines, preventing airlocks in return pumps, and ensuring smooth operation. Its self-actuating design uses a polypropylene ball to automatically seal against air or liquid, depending on process conditions, to maintain system integrity. Eliminating stubborn air pockets optimizes CIP efficiency and reduces the risk of pump cavitation, making it a reliable addition to sanitary processing systems.
Heat Exchangers in CIP
Heat exchangers play a pivotal role in maintaining the effectiveness of cleaning processes by ensuring that cleaning solutions remain at optimal temperatures. This precise temperature control enhances the removal of residues and contaminants from processing equipment.
Plate and frame heat exchangers are the most commonly utilized in CIP systems due to their high efficiency and relatively low capital cost. They offer flexibility in scaling capacity, ease of maintenance, and efficient heat transfer, making them ideal for a variety of applications. Plate and Frame
Shell and tube heat exchangers remain popular, particularly in applications where low maintenance is a priority. While durable and reliable, they are less efficient than plate and frame systems and require more utility consumption, which can increase operational costs. Shell and Tube
Direct steam injection heat exchangers quickly achieve CIP temperatures, offering exceptional speed and efficiency. However, they require a higher upfront investment and culinary-grade steam filtration, which results in some boiler chemical loss.Direct Steam
Spray Devices
Rotary jet devices revolutionize tank cleaning by delivering high-impact, precise cleaning performance, particularly for challenging applications. These devices are not part of the CIP system but rely on the CIP skid to supply the solution and the pressure required for effective operation.
While rotary jet devices offer unparalleled cleaning performance for stubborn residues, carefully considering CIP skid capabilities and utility costs is essential to maximize efficiency and sustainability.
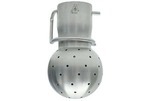
Static Spray Balls
These are the most economical options for easily cleaned products. While they are cost-effective, they consume more water, energy, and time, making them less efficient for complex cleaning tasks.
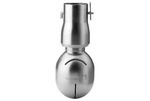
Rotating Spray Balls
A step up from static balls, rotating spray balls provide improved coverage and a more thorough clean. They are still budget-friendly and best suited for less demanding cleaning applications.
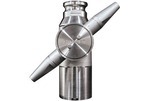
Rotary Jet Devices
Rotary jet devices excel at cleaning tough residues with high-pressure jets, reducing water usage but increasing CIP skid horsepower and utility consumption due to higher pressure demands.
Metering and Dosing
In Clean-in-Place (CIP) systems, accurate dosing of chemicals is essential to ensure effective cleaning. Diaphragm pumps are commonly used for dosing caustic and acidic chemicals. These substances typically have a predictable conductivity profile, allowing systems to monitor and adjust the dosing to meet concentration targets. Since these chemicals are dosed at slower rates, the diaphragm pump’s pulsing action is generally sufficient for maintaining the right concentration, making it a cost-effective solution without the need for more expensive pump technology.
For sanitizers, typically used in a once-through-to-drain design, higher dosing accuracy is important to ensure the desired concentration is achieved. While diaphragm pumps can still be used for sanitizing, some processors upgrade to peristaltic pumps, which can provide more precise dosing. These pumps can be sized and calibrated to deliver the exact concentration needed, optimizing chemical usage and minimizing waste.
Though peristaltic pumps offer higher precision, they have a higher capital cost. For many processors, the diaphragm pump remains a reliable and economical choice for sanitizer dosing. Those looking to optimize their chemical spend and improve dosing accuracy may find value in the added control that a peristaltic pump offers.
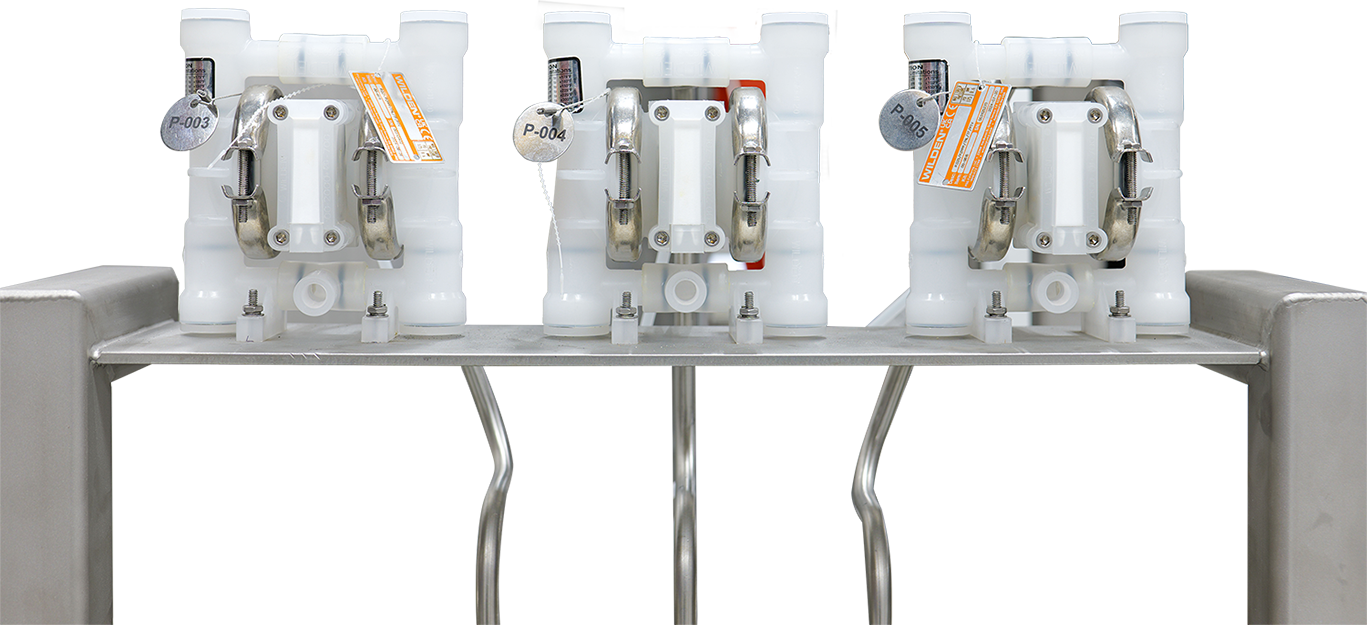
Regulatory Compliance for CIP Systems
As the concern for public safety of food and pharmaceutical products increases, cleaning in place helps maintain required levels of hygiene by meeting regulatory standards. CIP equipment controls and monitors cleaning methods essential to sanitary processing. Industries invest in CIP systems to reduce downtime while increasing employee safety and product quality. According to Transparency Market research, CIP has an annual growth rate of over 15%, suggesting that, with industry penetration increasing each year, processors who don't use CIP may be at a competitive disadvantage.
Signed into law in 2011, the FSMA gave the FDA expanded authority to oversee food production and processing. A key FSMA goal is preventing practices that cause foodborne illness. Cleaning in place supports food safety, so a robust CIP system must deliver the functionality required to uphold FSMA standards.FSMA
The Code of Federal Regulations (CFR) contains rules issued by the U.S. government. Title 21 (CFR21) governs FDA standards for food and pharmaceutical manufacturing, including cleaning, maintenance, and monitoring of equipment. A high-quality CIP system must comply with these requirements.CFR21
In recent years, a set of standards known officially as ANSI/ISA-88 was developed to address batch process control procedures and provide standard organization for how systems communicate and work together. A CIP system that complies with S88 would have an advantage when integrated into a process system.S88
Clean-In-Place Case Studies
Brewery CIP Optimization Solutions
A brewery faced challenges with inconsistent cleaning cycles, leading to product quality issues and excessive resource use. CSI collaborated on a brewery CIP project to design and implement a tailored CIP system, enhancing efficiency and reducing water and chemical consumption. By incorporating advanced cleaning technologies, the project achieved consistent sanitation results, improved production uptime, and supported sustainability goals.
Hygienic Solutions in Dairy Processing
A dairy processing facility encountered failures in its CIP return piping, disrupting operations and increasing maintenance costs. CSI identified the root cause—corrosion and design inefficiencies—and provided a durable, hygienic piping solution that adhered to industry standards. The improved design resolved the immediate issues and enhanced system reliability and sanitation, demonstrating the critical importance of robust CIP in the dairy industry.
Streamlining Sanitation in Breweries
Effective cleaning is essential in brewery operations to ensure product quality and compliance with safety standards. A well-designed brewery CIP system was implemented to address sanitation challenges while minimizing water and chemical use. The system's automated processes delivered consistent results and reduced cleaning cycle times, improving operational efficiency. This case exemplifies how breweries can leverage CIP technology.
Selecting the Right CIP Cleaning Solutions
Key Cleaning Agents
Selecting the right CIP cleaning solution is critical for effective cleaning in CIP systems, particularly in the food industry. Commonly used CIP chemicals for the food industry include alkalis (caustic soda) for breaking down fats and proteins, acids for removing mineral deposits, and detergents for general cleaning. It's essential to ensure that these chemicals are compatible with your equipment and processing lines to avoid damage or inefficiency. Monitoring chemical concentrations is also essential.
CIP Cycle Process
The cleaning process involves structured steps to ensure efficiency and hygiene in processing systems. A typical CIP cycle includes pre-rinse, cleaning, and sanitizing phases, each targeting specific residues and contaminants. Key factors like cleaning product concentration, temperature, time, and water usage must be precisely managed. Automated CIP systems enhance efficiency by delivering consistent, repeatable results. Explore this CIP infographic to learn more about the CIP cycle.
Peak Performance
Achieving peak performance in your CIP system requires regular maintenance, proactive troubleshooting, and continuous monitoring to identify and address inefficiencies. Leveraging data analytics and connected worker software can provide valuable insights to optimize cleaning processes, reduce downtime, and lower operational costs. By prioritizing system efficiency and reliability, you can ensure a cleaner, more cost-effective operation that meets the demands of modern hygienic standards.
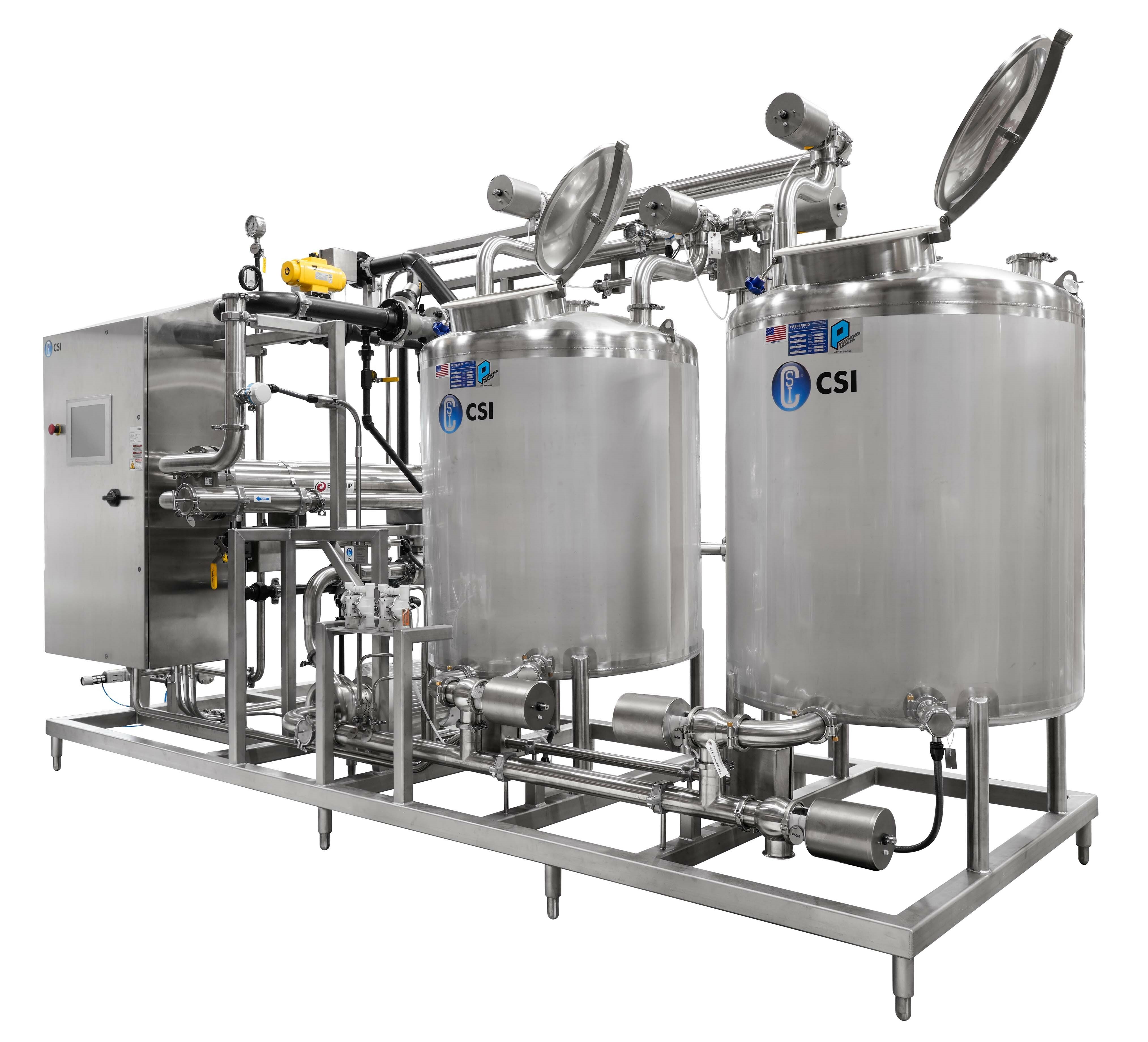
Optimizing Clean-in-Place (CIP) Systems
Clean-in-Place (CIP) systems are essential for maintaining hygiene, safety, and efficiency in industries like food, beverage, and pharmaceuticals. Beyond their role in ensuring cleanliness, CIP systems help manufacturers meet stringent regulatory standards, protect worker safety, uphold product quality, and address operational challenges.
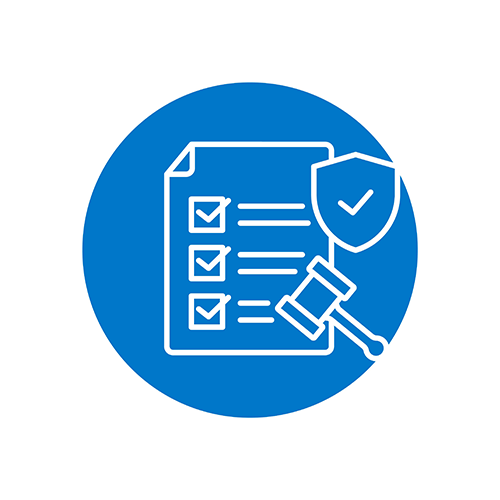
CIP Regulatory Compliance
CIP systems are critical in meeting regulatory requirements set by agencies like the FDA and USDA. To ensure compliance, CIP systems must be designed to adhere to strict industry standards, including features that prevent cross-contamination and safeguard product integrity. Automated CIP systems enhance compliance by delivering consistent, repeatable cleaning cycles. Manufacturers can maintain regulatory alignment by prioritizing product safety and quality.
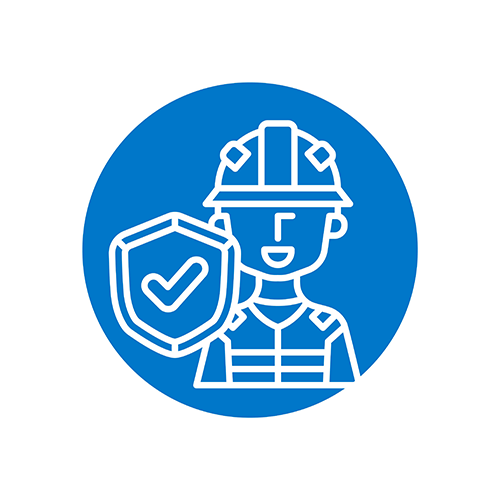
Worker Safety in CIP vs. Manual COP
Worker safety is paramount in CIP and manual COP processes, particularly when handling hazardous chemicals. CIP systems reduce the risk of chemical exposure by automating cleaning cycles and minimizing direct contact. To enhance safety, implement robust training programs and ensure the use of appropriate personal protective equipment (PPE). Manufacturers can create safer environments by designing CIP systems with safety features and focusing on worker protection.
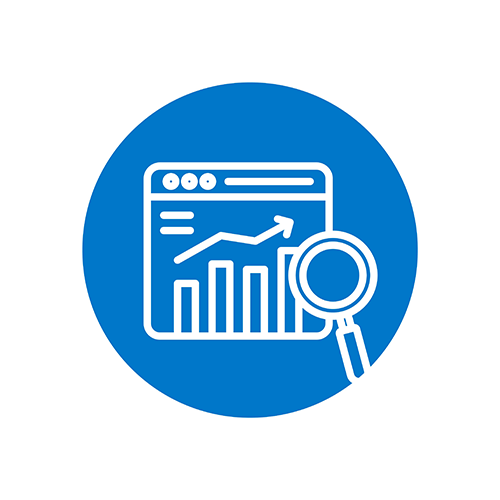
Quality Control in CIP Processes
Quality control in CIP operations ensures equipment is thoroughly cleaned and sanitized, preventing contamination and safeguarding product safety. Incorporating testing and inspection protocols helps verify that the CIP system is functioning effectively. Advanced tools like data analytics and connected worker software can identify inefficiencies and ensure optimal cleaning cycles. Prioritize high cleanliness and product integrity standards with quality control.
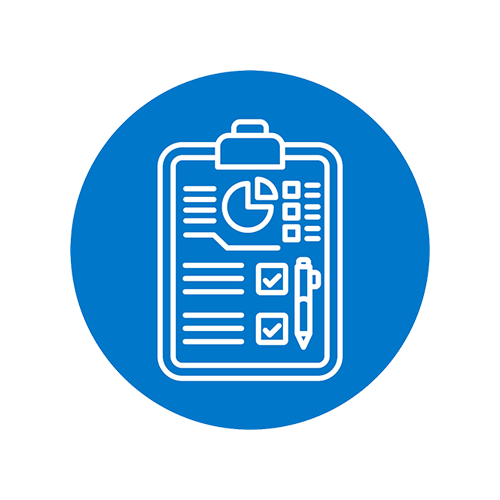
Troubleshooting Common CIP Issues
Common challenges in CIP systems, such as clogged pipes, faulty pumps, and ineffective cleaning, often stem from insufficient maintenance, lack of operator knowledge, or attempting to clean equipment not designed for CIP. Addressing these issues requires a proactive approach, regular maintenance schedules, troubleshooting, and operator training. Consulting services and hygienic audits can identify system inefficiencies and recommendations for improvement.
Conclusion
CIP systems are vital for maintaining hygiene, preventing contamination, and ensuring product safety in many industries, including food and beverage, biopharmaceuticals, and dairy. By adhering to best practices and optimizing system performance, businesses can achieve efficient, thorough cleaning and sanitation of their equipment. Automated CIP systems and tools like connected worker software can enhance operations by reducing downtime, minimizing overhead, and ensuring consistent results. Prioritizing a well-designed, adequately maintained CIP system protects product quality and supports operational efficiency and compliance with industry standards.
CIP Skid Systems for Hygienic Processing Solutions

Custom CIP Skid Design
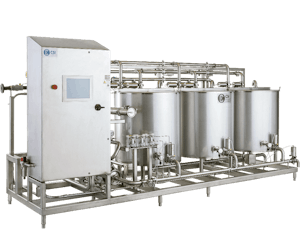
CIP 2.0 System
Clean-in-place Buying Guide
This Buying Guide for Clean-in-Place Solutions is a comprehensive resource for anyone who designs, owns, or operates processing systems and wants information about all aspects of CIP Systems.
ABOUT CSI
Central States Industrial Equipment (CSI) is a leader in distribution of hygienic pipe, valves, fittings, pumps, heat exchangers, and MRO supplies for hygienic industrial processors, with four distribution facilities across the U.S. CSI also provides detail design and execution for hygienic process systems in the food, dairy, beverage, pharmaceutical, biotechnology, and personal care industries. Specializing in process piping, system start-ups, and cleaning systems, CSI leverages technology, intellectual property, and industry expertise to deliver solutions to processing problems. More information can be found at www.csidesigns.com.