Clean-in-place: How CIP is Used in Breweries
To maximize production, the brewery industry relies on a combination of expertise for design, engineering, installation, control, monitoring, service, and repair of clean-in-place (CIP). Design and engineering expertise is especially valuable when upgrading CIP systems to achieve efficiencies in water and chemical use and to optimize cleaning-cycle duration and frequency.
This post outlines specific CIP design and installation considerations for the brewing industry.
With an emphasis on:
- Tanks
- Spray devices
- Pumps
- Heating systems
- Controls
- Instrumentation
- Automation
For breweries, CIP systems are engineered for fast, efficient, and consistent high-quality cleaning of product contact surfaces. CIP systems achieve their speed and consistency through automated processes and their high-quality cleaning through system monitoring and control.

Brewing, conditioning, and storing of beer occur in large stainless steel tanks that must be cleaned frequently, so CIP systems are designed to circulate cleaning agents through tanks and pipes and then flush the chemicals out during rinse cycles — all without having to disassemble the complex systems that brew and ferment the product.
A cleaning sequence for a brewery CIP system consists of a number of steps including a pre-rinse with water, cycling of acid and/or caustic wash solutions, further rinsing with water in between wash cycles, cycling of a disinfection solution, a final rinse with freshwater, and in some cases finishing with a drying cycle.
5 Steps in a Brewery CIP Cycle
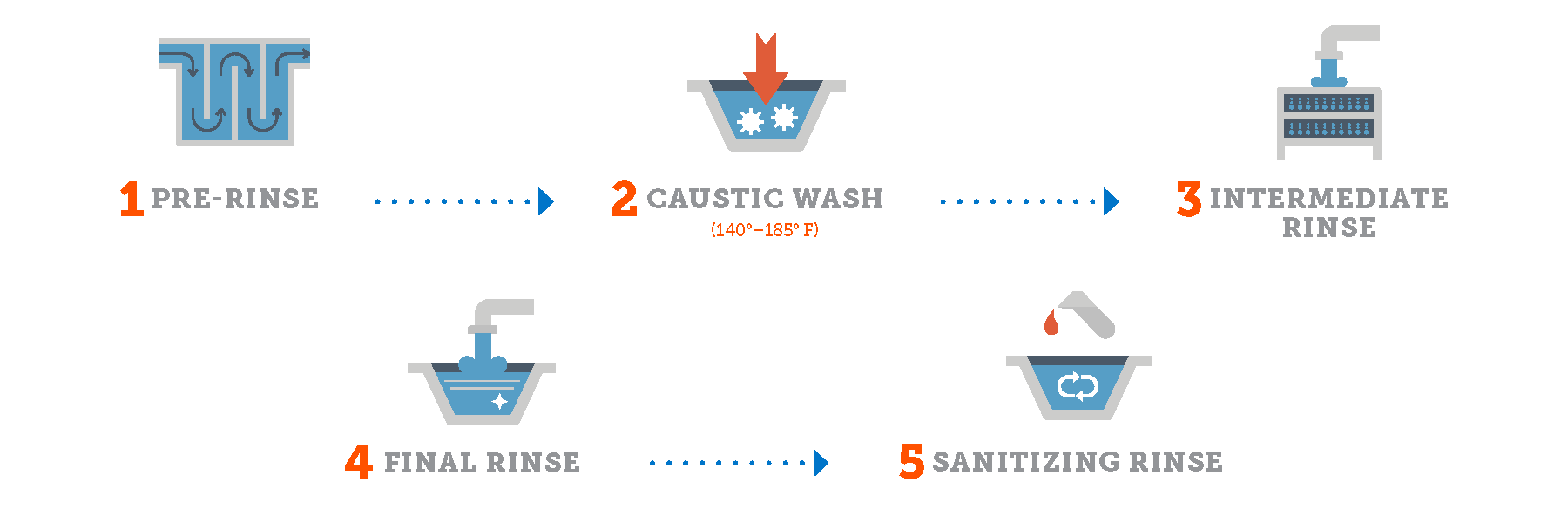
CIP Tanks for Breweries
The size and number of tanks for brewery CIP varies by types of CIP cycles and the size of the brewery. Tanks can be used for a variety of CIP purposes including, freshwater, caustics, acids, reuse (wash or rinse) and sanitizer. Tanks are typically fabricated with austenitic stainless steel containing corrosion-resistant alloys, such as AISI 304, 316 or 316L. Using 304 stainless steel for some brewery CIP tank applications is acceptable, but most quality CIP system manufacturers feature 316/316L as the standard material for all wetted components, including tanks.
A cleaning system may be designed with single or multiple tanks, depending on the application. To determine the number of tanks in a brewery CIP skid system, designers analyze the water, chemical, and energy usage and potential time savings with additional tanks. They will also analyze the brewing process and equipment from mashing to boiling, filtering, and fermenting. A thorough analysis then helps to determine how many tanks a CIP system requires to most-efficiently meet requirements for sanitation.
Single-tank System
Most common for simple circuits that only require a wash and/or rinse. Each cycle gets dumped to the drain after a single pass.
Advantages
- Often preferred for avoiding allergens and cross-contamination issues since each cycle is dumped to the drain after a single pass.
- Single-tank systems require a lower initial investment than multi-tank systems
- Requires less space and can easily be cart-mounted for mobility.
Considerations
- The same tank must be used for every cycle.
- Not recommended for multiple cycles or re-use strategies.
- Cleaning cycle requires significantly more time to refill and heat the tank for each cycle.
- Water and chemical usage are higher in single-tank systems because every wash and rinse has to be drained at completion.
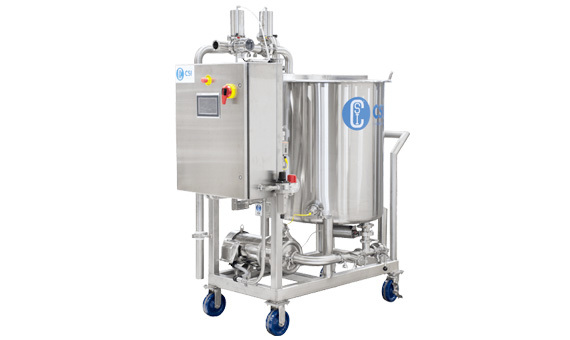
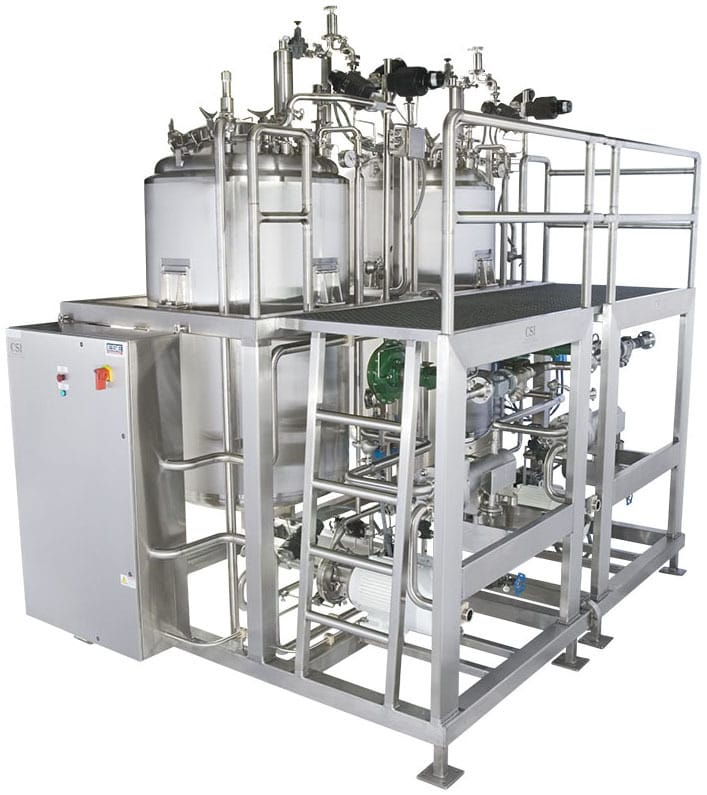
Two-Tank System
Typically one tank is for water (for pre-rinse or final rinse) and one for caustic wash solution.
Advantages
In many cases, the caustic wash can be returned to its tank and re-used multiple times, which significantly reduces water, chemical, and energy costs over a single tank system.
Cleaning time is reduced by pre-filling and pre-heating each tank as required prior to starting the cleaning cycle.
Can be cart-mounted for mobility.
Considerations
- More space required.
- Less mobile than single-tank system.
Three-Tank System
A system that includes three tanks allows for many more cleaning options than smaller systems.
Advantages
- For example, a water/caustic/acid cycle is common for many cleaning applications because it includes pre-filling and pre-heating of all solutions, which reduces cleaning time.
- Caustic and acid washes can be returned and re-used, depending on the amount of soil in the processing system.
- Water/caustic/re-use: If an acid wash is not needed, the re-use tank can capture a moderately soiled caustic wash and use it as an effective pre-rinse for the next cleaning sequence. This strategy saves water and helps preheat the system, and the residual caustic solution in the recovered wash allows the next pre-rinse to give a big head start to the chemical cleaning action.
Water/caustic/alternative caustic: For cleaning multiple circuits that have different types of product soil that require different types or concentrations of caustic washes.
Considerations
- More space required.
- Not suitable for cart-mounted mobility.
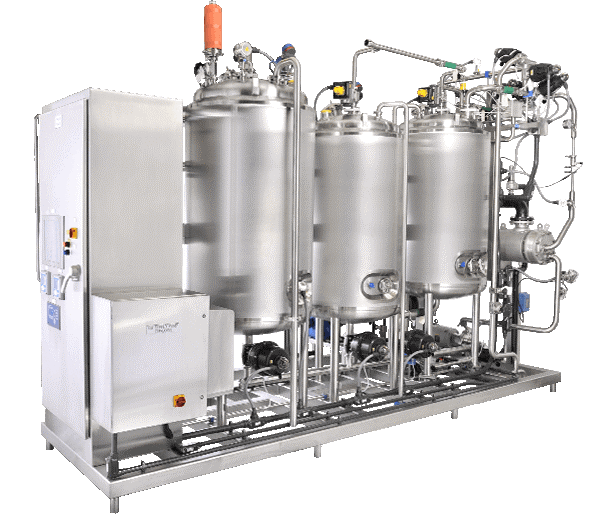
Four-Tank System
The additional tank in a four-tank system provides the flexibility to recover and re-use solutions without sacrificing the convenience of individual ready-to-go caustic and acid solutions.
Advantages
Complex, fully automated systems include valves and instrumentation
that monitor key variables and provide data for system validation
and verification.Water/caustic/acid/re-use is a typical four-tank setup that allows
each wash to be pre-filled and pre-heated with a re-use option for
either wash.A water/caustic/alternative caustic/re-use cycle enables cleaning of
multiple circuits that have different types of product soil and require
different concentrations of caustic washes--all without sacrificing
the re-use option.
Considerations
- Space requirements.
- More complex system.
- Generally not suitable for cart-mounted mobility.
- May require more initial investment
Spray devices for effective tank cleaning
In addition to proper CIP system design and sizing, proper sizing and placement of spray devices are critical to effective tank cleaning. Process applications dictate which device will provide the most effective cleaning: static spray balls, rotating spray balls, rotary spray heads or rotary jet heads.
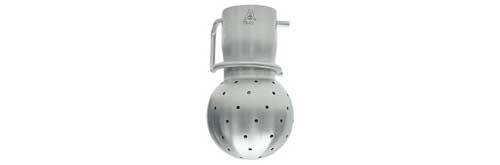
Static Spray Balls
As the name suggests, static spray balls are fixed in place and therefore do not rotate inside the tank. The spray direction for the numerous small jets of the solution is determined by the drilled hole pattern on the ball.
These are the lowest cost option but use the most water because they rely on sheer volume to remove soil loads. Improperly designed and drilled static spray balls may prevent the tank top head from being cleaned properly.
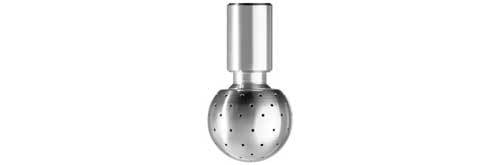
Rotating Spray Balls
Combining the reliability of a static spray ball with the flexibility of rotation gives rotating spray balls the advantage of more targeted cleaning-solution coverage inside the tank. Their heavier design permits higher flow rates than most static spray balls, which results in more effective cleaning.
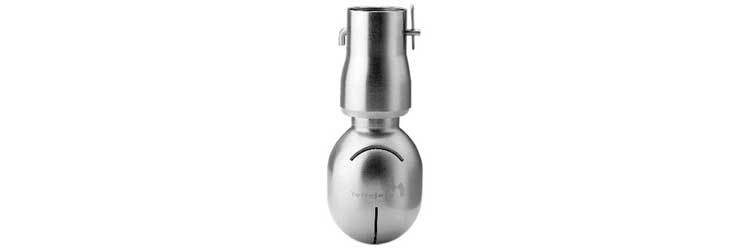
Rotary Spray Heads
Curved and straight slots in the body of the rotary spray head emit fanned jets of solution that swirl in a pattern throughout the entire vessel for a vibrating impact effect and considerable cascading flow, which is effective for large vessels with heavier soiling.
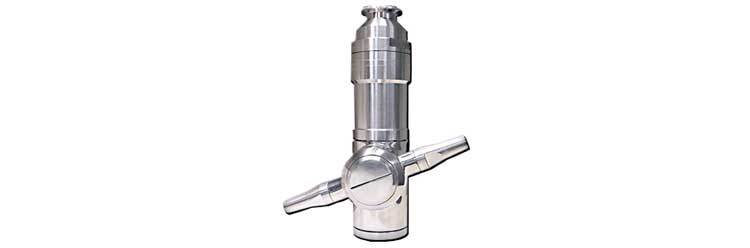
Rotary Jet Heads
When high impingement force is needed to properly clean a tank or vessel--(for example, baked on soil loads or highly viscous products), a rotating jet spray device is the answer.
Their multi-axis rotation can deliver extremely high impact streams of cleaning solution in precise 360° patterns to all areas of the tank. High-pressure capacities allow them to use considerably less water than other spray devices.
Pumps
Supply Pump
CIP systems use pumps to provide the necessary flow and turbulence to effectively scrub the inside of tubing or motive force to move a dynamic tank cleaning device. These are typically sanitary centrifugal pumps.
Return Pump
Process equipment that utilizes spray devices for cleaning purposes require rapid removal of CIP solution to eliminate the solution build up in the equipment. Return pumps are sized to quickly remove the used solution from the processing equipment at a rate of approximately 10% greater than the supply pump. Return pumps are typically sanitary stainless steel centrifugal or liquid ring pumps with cleanable seals.
Chemical addition pumps
To ensure accuracy and avoid employee exposure to potentially dangerous chemicals, chemical addition pumps handle cleaning agents for you. These pumps can be a variety of types including air-operated double-diaphragm (AODD) or peristaltic.
Heating Systems
A number of heating options are available for use on a CIP system. Each CIP heating system has its own advantages:
Plate & Frame Heat Exchanger
Has a relatively low steam pressure requirement of around 50 psi so is a common heating method for CIP systems. High efficiency and modest pricing make it the first choice for many CIP designs.
Shell & Tube Heat Exchanger
A simple, low maintenance in-line heating option. Common in many CIP systems but may require higher steam pressures and volumes to sufficiently heat solutions quickly.
Direct Steam Injection
Precisely metered injections of steam directly into the cleaning solution as it is being pumped through piping is typically quicker and more accurate than other heating options. Initial capital expense is typically higher with this option, but the cost is offset by savings from having no need for steam and condensate control components.
Electric Heater
Although sometimes slower and potentially more costly to operate than other options, electric heaters can be a prudent choice if other heating options are unavailable.
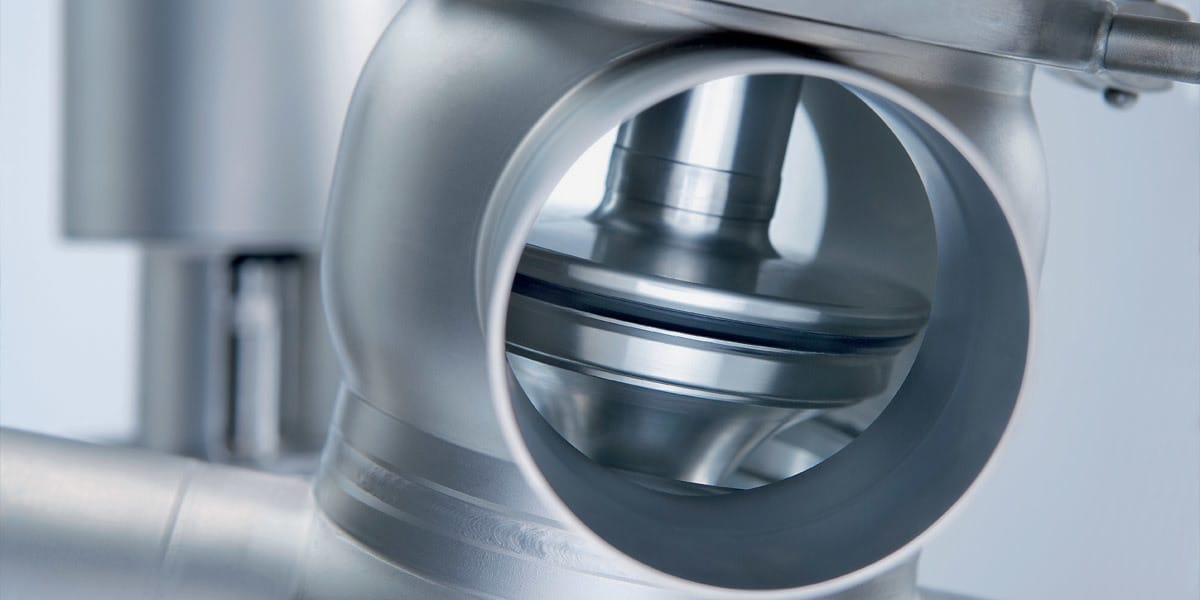
Piping and Valves
The network of piping and valves in a CIP system should maximize efficient control of each CIP process.
Efficient piping in breweries
- Should be the proper diameter to provide flow and pressure requirements.
- Should take the shortest route possible.
- Should be free from runs of pipe with low or no circulation (dead legs).
Valves control the traffic
Valves can operate manually or automatically, but manual valves require operator intervention for each step of the cleaning cycle. Automatically actuated valves can be programmed to coordinate with each other during all phases of cleaning and do not require operator intervention.
Controls, instrumentation & automation
CIP systems must meet and maintain cleaning requirements for the duration of each cycle. In a manual system, cleaning activities are subject to guesswork and inconsistencies due to human error, leading to higher cleaning costs and potential safety risks. A CIP system with some degree of automation helps ensure consistent and high-quality results.
Key instrumentation
Maximizing the efficiency of CIP systems requires close control and monitoring of system functions. For breweries, the following instruments measure and report key variables that affect CIP operations.
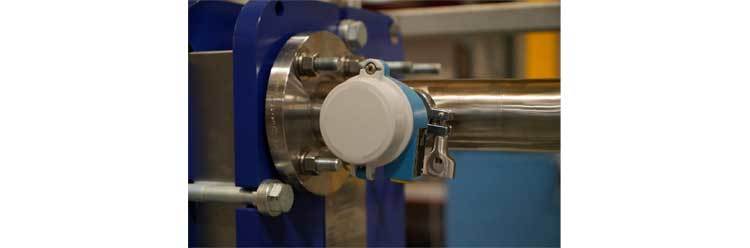
Temperature transmitters
- Monitor the temperature of caustic and acid solution sequences and tanks
- They can send a signal back to the heating system to regulate temperature as needed.
- Probes in the return lines detect when the return temperature has reached the desired set point and timers can be started.
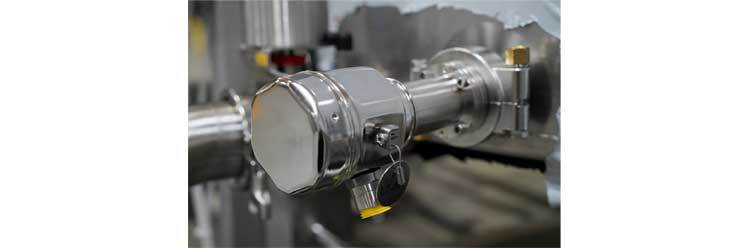
Level transmitters/Level probes
- Monitor tank levels of wash and rinse tanks
- Can signal to turn valves on and off to add water or chemicals automatically as needed.
- Ensure sufficient volume to run a cleaning cycle.
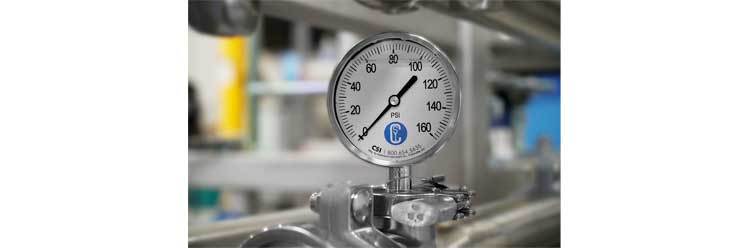
Pressure gauges and transmitters
- Ensure the pressure is sufficient for spray devices to operate optimally.
- Can detect if there is an obstruction or break in the circuit when pressure is too high or too low.
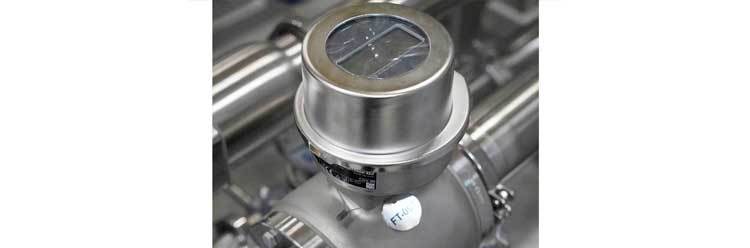
Flow Meters
- Help operators maintain scrubbing action
Flow metering assists in maintaining efficient CIP systems by ensuring a strong turbulent flow of cleaning fluids during each cycle.
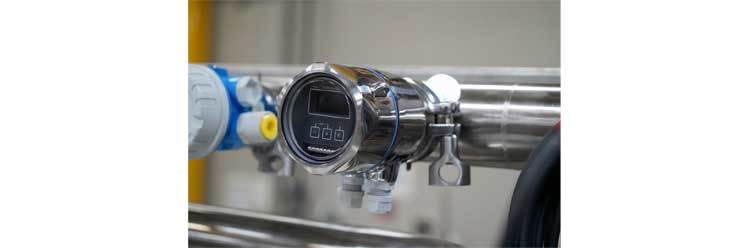
Conductivity Sensor/Transmitters
- Ensure chemical levels are hitting predetermined set points
- Conductivity sensors help ensure accuracy during cleaning and provide valuable data for CIP validation and verification.
NEXT STEPS
Because the brewery industry relies on a combination of design and engineering expertise, access to people is as important as access to the parts and equipment you need to maintain production operations.
That’s where we come in.
CSI engineers, designs, and fabricates custom clean-in-place systems to meet specific hygienic processing needs. CIP equipment from CSI helps you control, monitor, and document the cleaning methods that are essential to sanitary processing.
With CSI's state-of-the-art, climate-controlled fabrication shop, the quality of equipment leaving our facility is second to none. We offer in-house, Level II inspection in accordance with the latest ASNT recommended Practice No. SNT-TC-1A, so you can be certain your equipment meets industry standards.
To speak with a CIP expert request a quote below or call 800.654.5635.
Clean-in-place Buying Guide
This Buying Guide for Clean-in-Place Solutions is a comprehensive resource for anyone who designs, owns, or operates processing systems and wants information about all aspects of CIP Systems.
ABOUT CSI
Central States Industrial Equipment (CSI) is a leader in distribution of hygienic pipe, valves, fittings, pumps, heat exchangers, and MRO supplies for hygienic industrial processors, with four distribution facilities across the U.S. CSI also provides detail design and execution for hygienic process systems in the food, dairy, beverage, pharmaceutical, biotechnology, and personal care industries. Specializing in process piping, system start-ups, and cleaning systems, CSI leverages technology, intellectual property, and industry expertise to deliver solutions to processing problems. More information can be found at www.csidesigns.com.