Considering Direct-Contact Steam Injection?
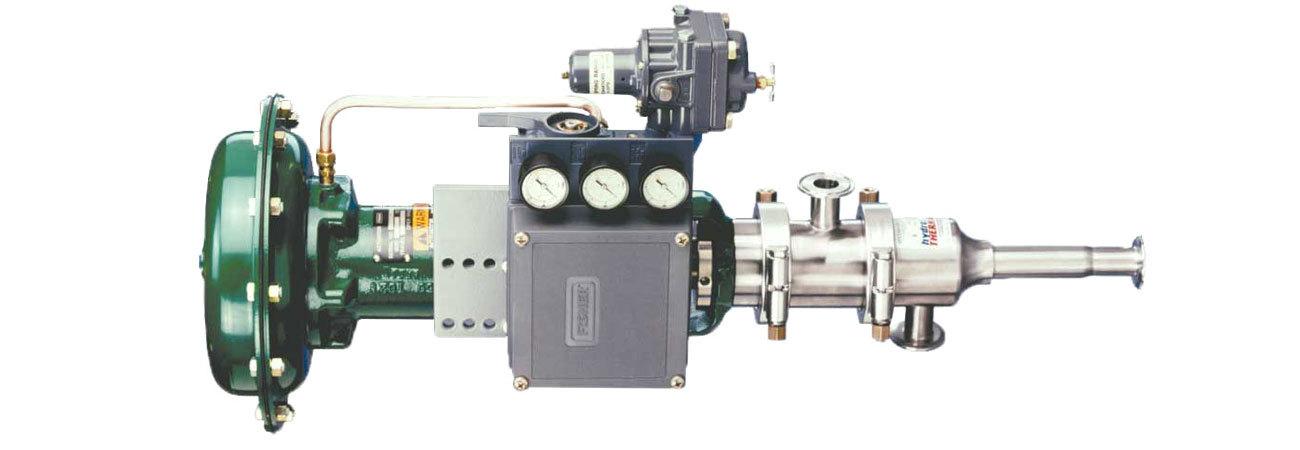
When considering using direct-contact steam injection (DSI) for a process heating application, it is important to understand the two basic techniques—direct and indirect transfer—used to transfer heat into fluids for process and utility heating.
Indirect contact heat exchangers, such as shell-and-tube, plate-and-frame, or scraped-surface designs, have two or more fluid flow paths to prevent the fluids from mixing. The heat is transferred from one fluid to another across a thermally conducting, but otherwise impermeable barrier, such as a tube wall or plate.
Direct-contact heat exchangers transfer heat by injecting steam directly into the process fluid. This results in rapid heat transfer and often is more efficient than indirect heat exchangers. Direct-contact steam heating provides 100 percent thermal efficiency because the sensible and latent energy in the steam is used. The heaters themselves are installed in line with the process piping and usually are more compact than indirect heat exchangers, saving valuable floor space.
Direct-steam injection heaters may be the best option for hard-to-heat fluids such as slurries or highly viscous materials that tend to clog; fluids requiring nearly instantaneous heating, such as some food products; and products that would bake onto heat exchanger surfaces.
Energy savings can be considerable, with reductions in energy uses of 20 to 25 percent.
Types of direct-contact steam injection heaters include tank spargers, inline spargers, mixing tees, and internally modulated steam injection heaters. Direct-contact steam heaters can be classified as either externally modulated or internally modulated, which refers to how the steam injected into the process fluid is controlled.
External Modulation
An externally modulated steam heater uses a steam-pressure control valve to regulate the amount of steam injected into the process. The valve is located in the supply steam piping. At times, steam velocity and the volumes of steam and fluid mixing can vary widely over the operating range. Vibration, poor temperature control, and inefficiency result at some operating conditions. Tank spargers, which use external modulation, can experience steam hammer and vibration damage to tanks. Energy inefficiencies also can occur with this heating method when the steam does not completely mix and escapes from the tank.
Internal Modulation
With the internally modulated direct-steam injection heater, steam flow is controlled through a stem-plug assembly inside the heater. Changing the steam discharge area of the nozzle varies the amount of steam passing through the nozzle and maintains good mixing characteristics.
Internally modulated direct-contact steam heaters inject metered amounts of steam into the process fluid through a variable-area steam nozzle. The nozzle design ensures constant steam pressure and velocity at the point where steam contacts the liquid or slurry, eliminating the potential for pressure upsets and ensuring smooth heater operation. Internally modulated direct-steam injection heaters are cleaned by their own turbulent mixing action, usually sonic velocity steam, so they do not encounter fouling or scale buildup. This cleaning and mixing action allows them to heat slurries containing a high concentration of solids or non-Newtonian liquids.
Advantages
With direct-contact steam injection, energy savings can be considerable, with reductions in energy usages of 20 to 25 percent. Condensate return is not needed as all of the steam’s energy is transferred to the process.
Energy savings aren’t the only advantage of direct-steam injection. Using fewer heat exchangers leads to less required maintenance; the turbulent action and thorough mixing can eliminate the need for equipment such as mixers, and the small size of direct-steam injection heaters can reduce floor space requirements.
Putting It to Work
Specifying direct-steam injection heaters and properly sizing the equipment for an application entails an examination of process requirements, general process information, and the fluid characteristics. Properties such as specific heat, density, solids content, and viscosity need to be identified in addition to any abrasive or corrosive products that are present.
Application conditions such as flow rate (normal, minimum, and maximum), inlet and discharge temperatures, pressure, and pipe sizes must be examined. Users should determine whether manual or automatic temperature control is desired and whether a continuous, intermittent, or variable operation will be the norm. Properly sizing the heater determines maximum performance and benefit—both short term and long range.
It is also important to remember that direct-contact steam injection is only suitable for water-miscible liquids (the fluid and water must mix).
Courtesy of www.hydro-thermal.com
Lee Van Dixhorn
A registered Professional Engineer with Bachelor's and Master's degrees in Mechanical Engineering, Lee has over 17 years of engineering experience in various industries. Recently, he earned the designation of Certified Steam System Specialist through the U.S. Department of Energy. In his past, he worked for Hydro-Thermal Corporation, and he currently works at Vilter Manufacturing.
ABOUT CSI
Central States Industrial Equipment (CSI) is a leader in distribution of hygienic pipe, valves, fittings, pumps, heat exchangers, and MRO supplies for hygienic industrial processors, with four distribution facilities across the U.S. CSI also provides detail design and execution for hygienic process systems in the food, dairy, beverage, pharmaceutical, biotechnology, and personal care industries. Specializing in process piping, system start-ups, and cleaning systems, CSI leverages technology, intellectual property, and industry expertise to deliver solutions to processing problems. More information can be found at www.csidesigns.com.