Is That High-Pressure Clamp Necessary?
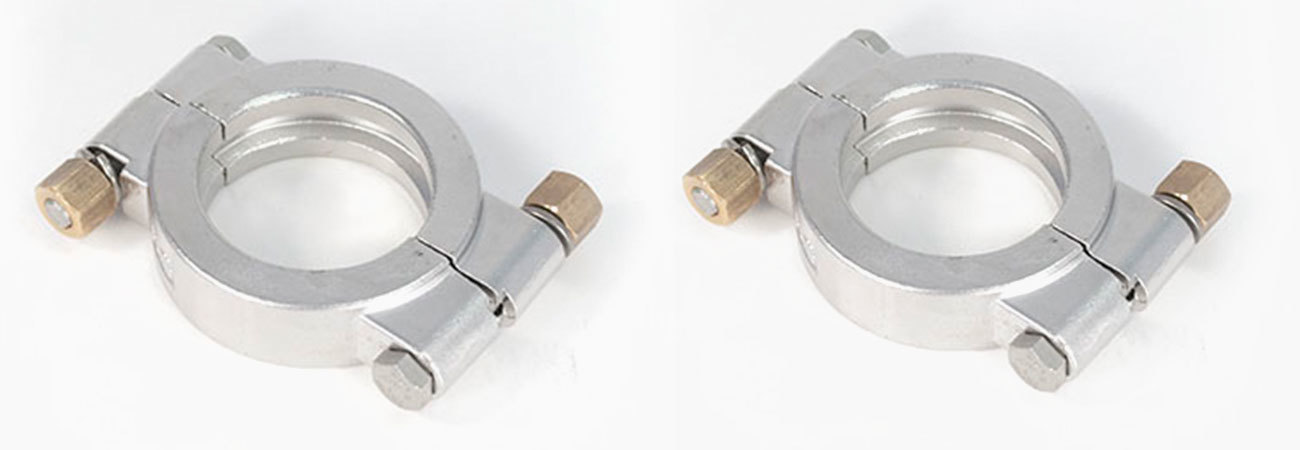
High-pressure clamps are not necessarily designed for high-pressure lines.
The clamp manufacturer currently determines safety ratings for clamps. Typically, the manufacturer will publish a chart of guidelines for maximum safe product pressure. These ratings are temperature-specific—the higher the product temperature, the lower the safe maximum pressure. However, connections rarely, if ever, fail at the clamp.
Operator safety is the most common reason to use high-pressure clamps. High-pressure clamps require a wrench for disassembly, and although this is a disadvantage during assembly, it could prevent an accident. High-pressure clamps are also less likely to loosen over time than a wingnut clamp. Any joint where opening the line could be hazardous is a candidate for these clamps—whether it’s steam, hot liquid, a hazardous chemical, or a pressurized line. High-pressure clamps can be a great option for making a more secure connection or when pressures exceed a hinged clamp’s rating.
While reasons for using high-pressure clamps are valid, these reasons usually don’t apply to every clamp connection in a plant. Despite this, some companies spec high-pressure clamps for everything. Some companies use high-pressure clamps to prevent over-tightening, however, there are a number of clamps on the market that do a better job of controlling the compression of gaskets. Poorly cast wingnut clamps, or even gasket problems, could cause an engineer to swear off a wingnut clamp for good. However, the extra costs of a high-pressure clamp add up, including the cost of the clamp itself, and the extra time and hassle every time it is removed or installed.
High-pressure clamps can be good for creating a more secure connection, but they’re not always the best option. A careful consideration of the advantages and disadvantages of high-pressure clamps could save a lot of time and money.
Expert Bio
Liz Braden, Manager - Employee Development and Continuous Improvement
With a degree in Manufacturing Engineering from Missouri University of Science and Technology, Liz Braden has experience in the food processing industry where she is adept at managing production and improving plant processes. Her experience at Central States Industrial (CSI) includes working as a Technical Service Representative and Customer Service Manager. She is now Manager of Employee Development and Continuous Improvement where she looks after training, resource development, and CSI’s continuous improvement program.
ABOUT CSI
Central States Industrial Equipment (CSI) is a leader in distribution of hygienic pipe, valves, fittings, pumps, heat exchangers, and MRO supplies for hygienic industrial processors, with four distribution facilities across the U.S. CSI also provides detail design and execution for hygienic process systems in the food, dairy, beverage, pharmaceutical, biotechnology, and personal care industries. Specializing in process piping, system start-ups, and cleaning systems, CSI leverages technology, intellectual property, and industry expertise to deliver solutions to processing problems. More information can be found at www.csidesigns.com.