Dry Running Pumps: Causes, Effects, and Prevention in Sanitary Pumps
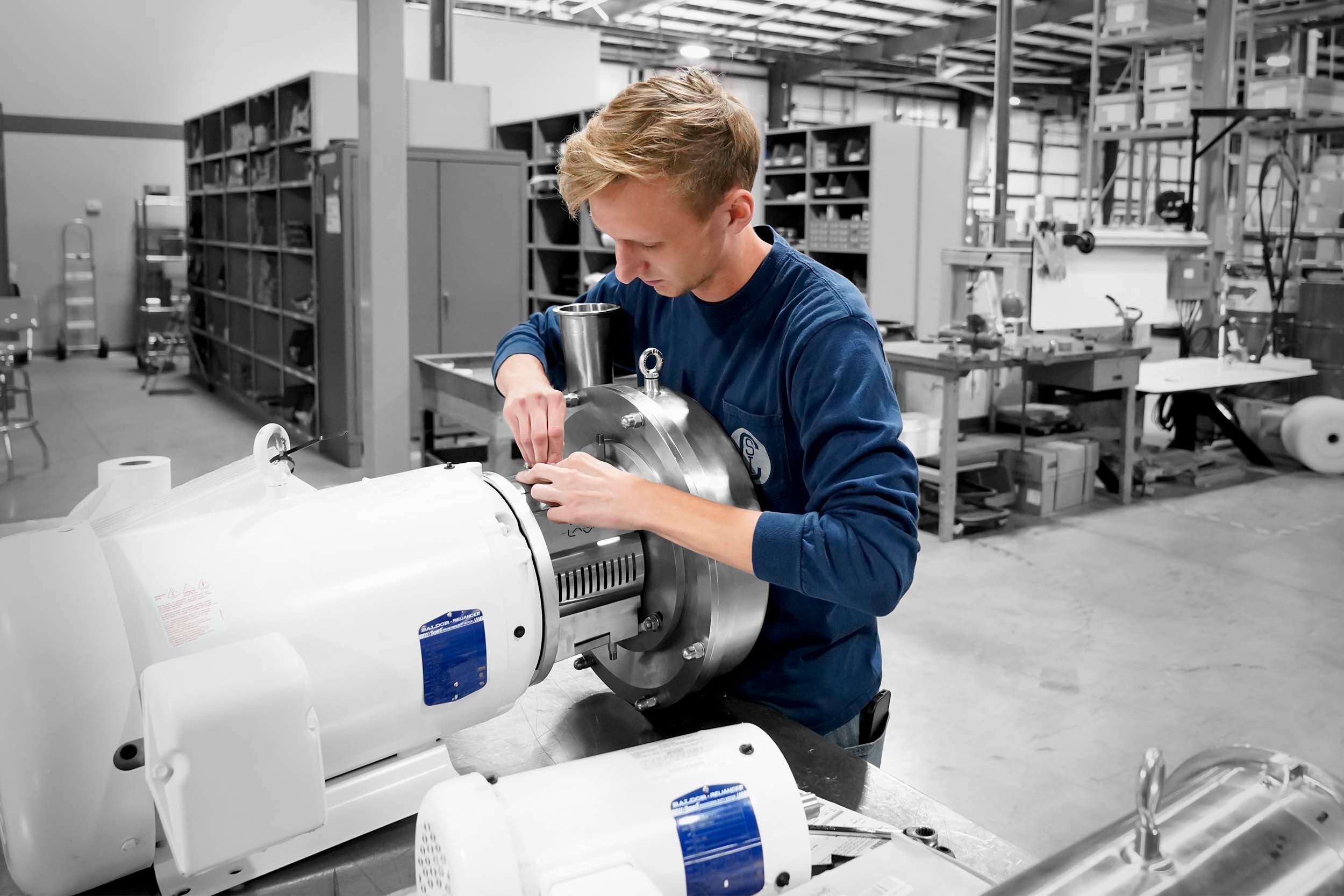
Sanitary pumps are essential equipment in all fluid processing industries, moving large product volumes through processing systems daily. Dry running is a common issue that leads to a damaged pump, costly repairs, product contamination, and downtime in the processing facility. In this article, we examine dry running on sanitary pumps, what it is, its effects, and how to prevent it.
What is Dry Running a Pump?
Dry running occurs when a pump operates without fluid inside it. Most users are not aware that the product fluid flowing through a pump lubricates the pump’s seals. This lubrication is necessary for the seals’ integrity. Without proper lubrication, the seals, bearings, and rotors experience excessive friction and heat, leading to mechanical pump seal failure.
Pump Damage Caused by Dry Running
Dry running can cause significant damage to a pump, primarily to the pump seal. Pump seals can be expensive, and processing downtime adds to that expense. Regular onsite maintenance and having spare parts on hand can help ensure the pump’s downtime is not longer than it has to be. Training operators and pump controls are significant steps in reducing dry running.
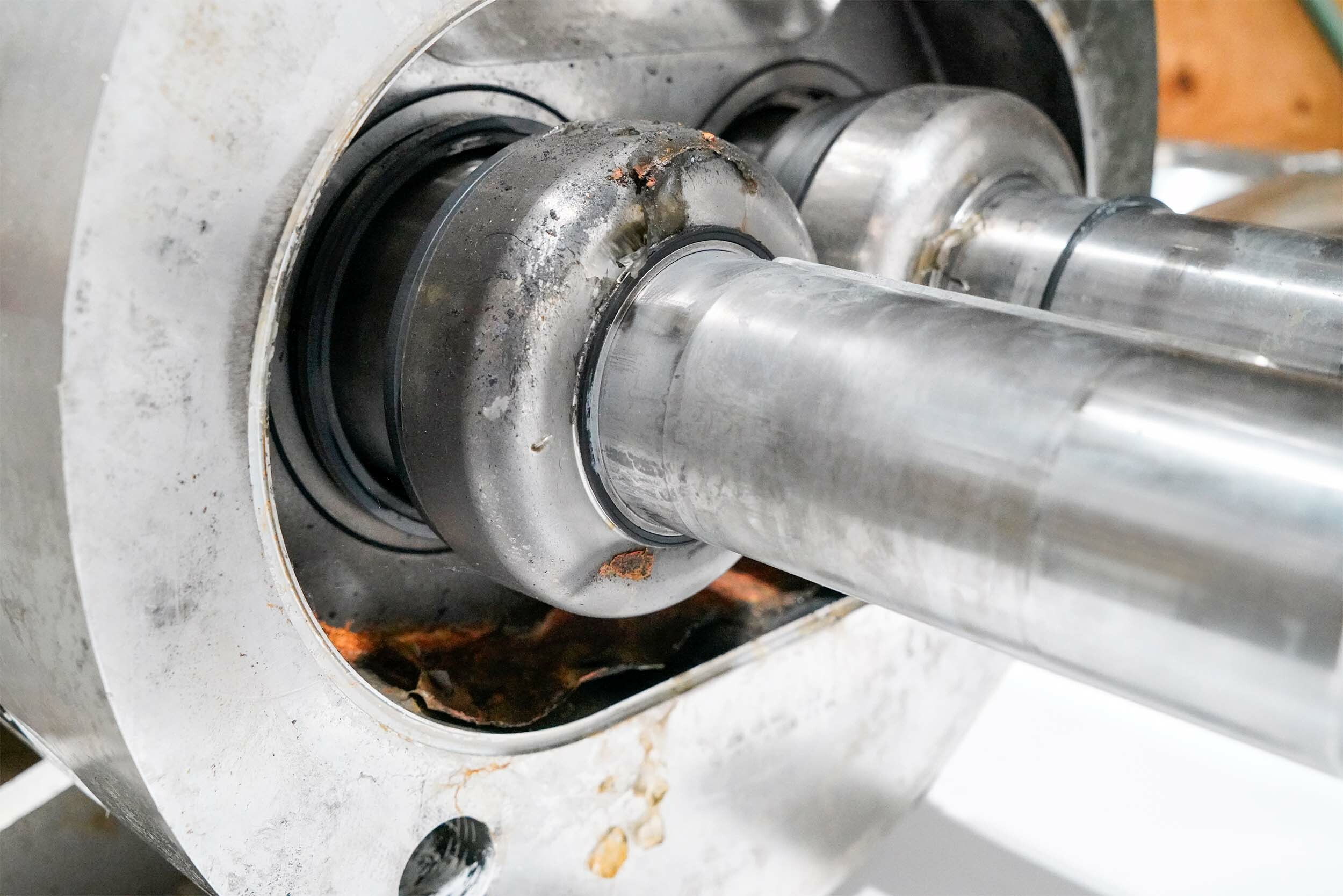
Seal Damage
A mechanical seal prevents fluid from leaking from the pump while allowing the rotating shaft to pass through the pump housing. Dry running occurs when a pump continues to run with no product passing through it. Lack of lubrication from fluids causes the seal faces to experience excessive friction. This results in seal failure due to overheating and wear.
Avoid running pumps dry entirely. Even a few seconds without lubrication can cause damage. Implement systems that eliminate the risk of dry running.
Michael David, Pump Solutions Manager at CSI
Damage by Pump Type
Because of the damage they can sustain, all sanitary pumps should avoid dry running. Some pumps, like AODD (air-operated double diaphragm), are less impacted by momentary dry running due to their unique pumping mechanism. Even though AODD pumps are one of the least affected pump types to dry running, they should not be run dry for extended periods.
On the other hand, progressive cavity pumps are more affected by dry running. The damage to this style of pump can happen virtually instantly when the pump sees a dry condition.
Contact between the rotor and stator with no lubricating fluid present causes the stator to be destroyed. Couple this with the fact that progressive cavity pumps can be some of the most time consuming to repair.


System Contamination
System contamination is a potential consequence of dry running any style of pump. Various parts can be compromised when a pump operates without sufficient lubricating fluid. When the seals fail due to dry running, they will often crack and chip, releasing bits of seal material into the process fluid.
In other instances where contact is made between parts with no lubricating fluid, metal particles can be scraped from disintegrating moving pieces within the pump and travel through the rest of the system, causing damage to valves, pipes, and other sensitive system components.
Regular maintenance and inspection can help prevent system contamination by recognizing dry running early. Ensuring that the pump operates with adequate lubrication is essential for maintaining the entire system's integrity.
Cost Factors
Dry running involves several costs that should be considered. Dry running causes increased operational costs from replacing seal sets, operational downtime, and maintenance fees incurred from replacing seals or pumps.
Preventative maintenance is recommended and should be the standard in maintenance plans rather than a reactive approach.
A Guide to Choosing the Right Pump for Hygienic Applications
This guide is intended for engineers, production managers, or anyone concerned with proper pump selection for pharmaceutical, biotechnology, and other ultra-clean applications.
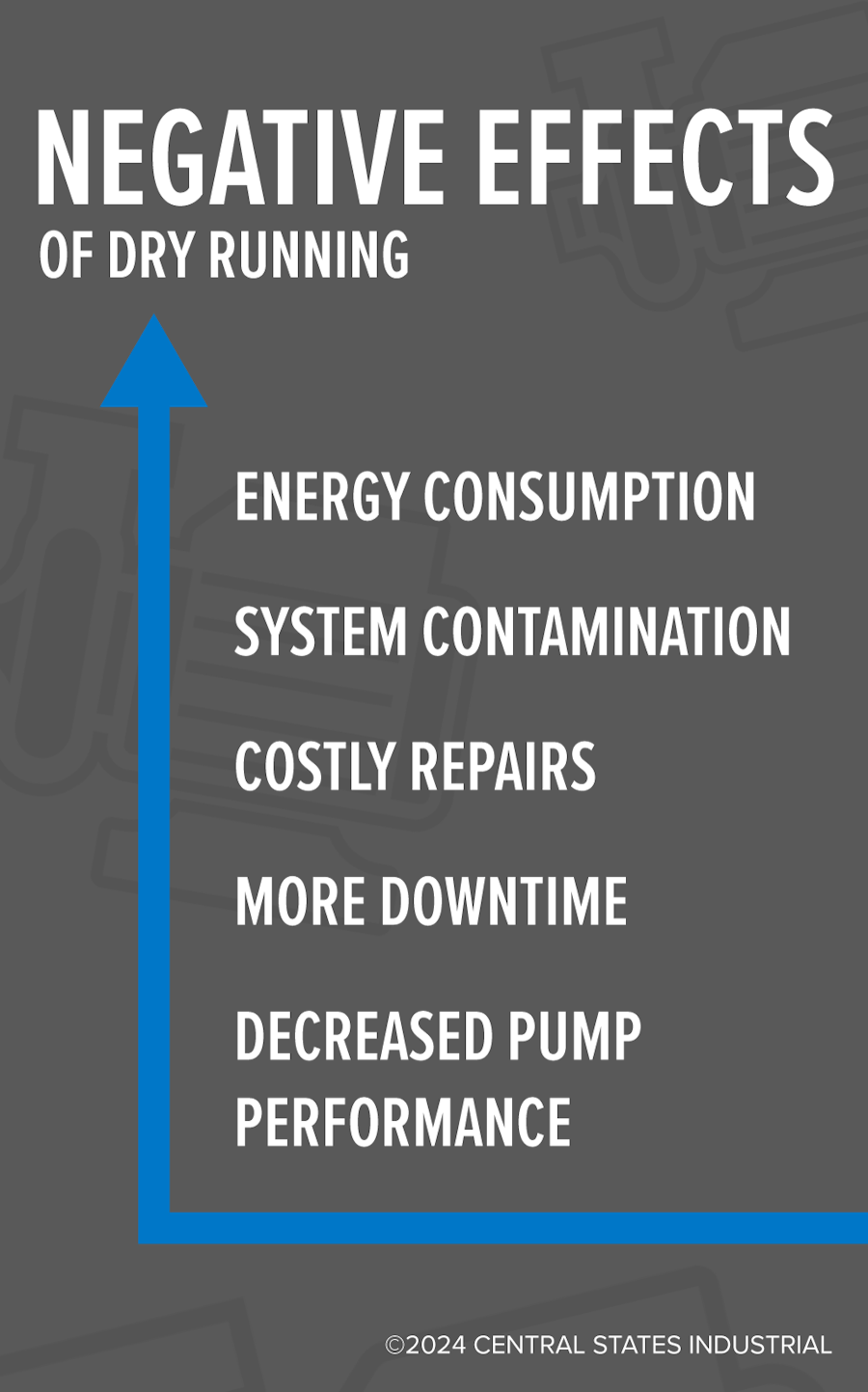
Effects of Dry Running
Dry running can have severe effects on positive displacement pumps, including:
- Increased Energy Consumption: When a pump operates inefficiently due to dry running, it consumes more energy, increasing operational costs. Ensuring that the pump operates under normal conditions can help maintain energy efficiency.
- Reduced Pump Performance: Dry running can reduce the pump’s performance and flow rate, decreasing productivity and efficiency. Maintaining proper fluid levels and regular maintenance can help ensure optimal pump performance.
- System Contamination: As mentioned earlier, dry running can lead to system contamination, causing damage to valves, pipes, and tubes. This can result in further operational issues and increased maintenance costs.
- Costly Repairs and Downtime: Dry running can cause mechanical damage, leading to costly repairs and extended downtime. This can result in financial losses and decreased competitiveness for the processing facility.
Regular maintenance and inspection, implementation of control systems, and proper pump sizing and system design can help prevent dry running and its effects on sanitary pumps. By taking these preventative measures, you can ensure that your pumps operate efficiently and reliably, minimizing the risk of damage and maximizing productivity.
How to Prevent Dry Running
There are several ways to prevent a pump from dry running, the most effective of which is to have controls in place to monitor process conditions and stop the pump when the liquid runs out. These controls ensure the pump can resume regular operation once the issue is addressed. Flow switches, level transmitters, and other control mechanisms are standard for remotely and automatically turning rotating equipment like pumps on and off.
Alternatively, you can be more diligent about monitoring the process when you are nearing the end of production, although monitoring and manually watching can be difficult to do repeatedly.
Stop Dry Running Before It Starts
Maintenance
Routine maintenance involves inspecting seals, rotors, and bearings. Evaluate components for wear and replace them when necessary or recommended. Install sensors or control systems to assist in detecting and preventing dry running. Implement maintenance best practices to flush seals and ensure proper lubrication at all times.
Training
In addition to strict adherence to a preventative maintenance plan, thorough and ongoing employee training is essential. Every employee operating systems involving a pump should be aware of the risks of dry running and what steps to take to prevent it. Refresher training should be done on a routine basis.
Controls
Preventive maintenance can save costs, extend pump life, and avoid contamination risks. Improved uptime comes with increased production volume, a winning equation for implementing prevention practices.
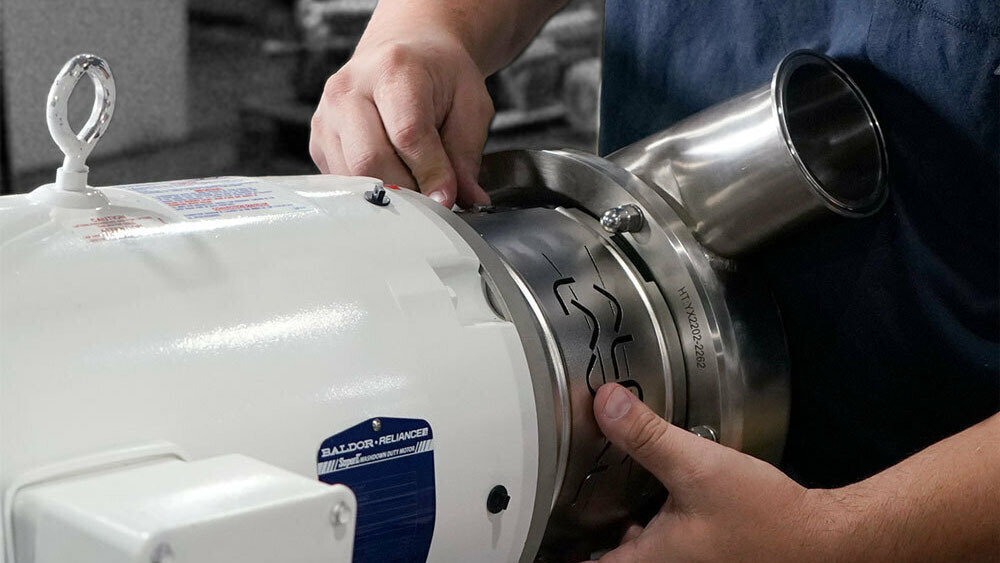

Prevent Dry Running
Dry running causes severe damage to sanitary pumps, impacting production and product safety. A preventative maintenance schedule and ongoing training program are necessary to avoid costly repairs and downtime.
Curious about other pump problems? Read our article on Pump Seal Failure.
FAQs: Dry Running Sanitary Pumps
- What is dry running a pump?
-
Dry running a pump happens when it operates without liquid running through it. The liquid is a lubricant that cools the internal components, including the pump seal. Without lubrication, the internal components heat and cause friction, damaging the seal.
- What happens to a pump if it runs dry?
-
Dry running can quickly cause severe damage to pump components, most notably the seal. Overheating and friction wear the seal, leading to pump failure and costly repairs.
- Can you fix a pump that ran dry?
-
A dry-run pump can often be repaired, but seals must be replaced. If the damage is bad enough, other components like rotors or bearings may need replacing. These parts can be expensive, and it is always best practice not to allow a pump to dry run.
- How long can a pump run dry?
-
We never recommend running a pump dry. The effects of no lubrication are visible in all sanitary pumps, but progressive cavity pumps are more immediate. Implementing checks to eliminate the risk of dry running is instrumental.
Contributing Author
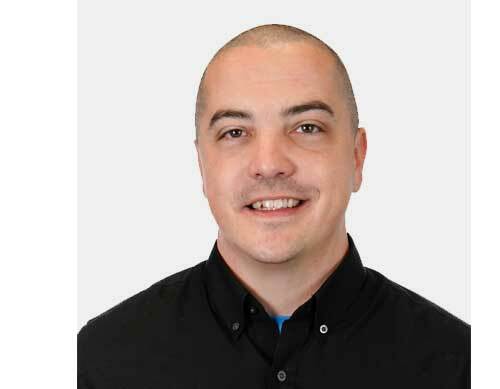
Michael David is the Manager of Pump and Heat Exchange Solutions at CSI. Michael received his B.S. degree in Mechanical Engineering from the Missouri University of Science and Technology, and brings over 17 years of experience in engineering, process design, fluid dynamics, and maintaining equipment for the food, dairy, beverage, biopharm and biotech markets. Michael supports a team of application specialists who focus on Pump and Heat Exchange solutions. He also leads many training initiatives for internal and external customers aimed at developing competence and confidence in the worlds of pumps and heat exchange technology.
ABOUT CSI
Central States Industrial Equipment (CSI) is a leader in distribution of hygienic pipe, valves, fittings, pumps, heat exchangers, and MRO supplies for hygienic industrial processors, with four distribution facilities across the U.S. CSI also provides detail design and execution for hygienic process systems in the food, dairy, beverage, pharmaceutical, biotechnology, and personal care industries. Specializing in process piping, system start-ups, and cleaning systems, CSI leverages technology, intellectual property, and industry expertise to deliver solutions to processing problems. More information can be found at www.csidesigns.com.