What Are Elastomers: A Beginner’s Guide
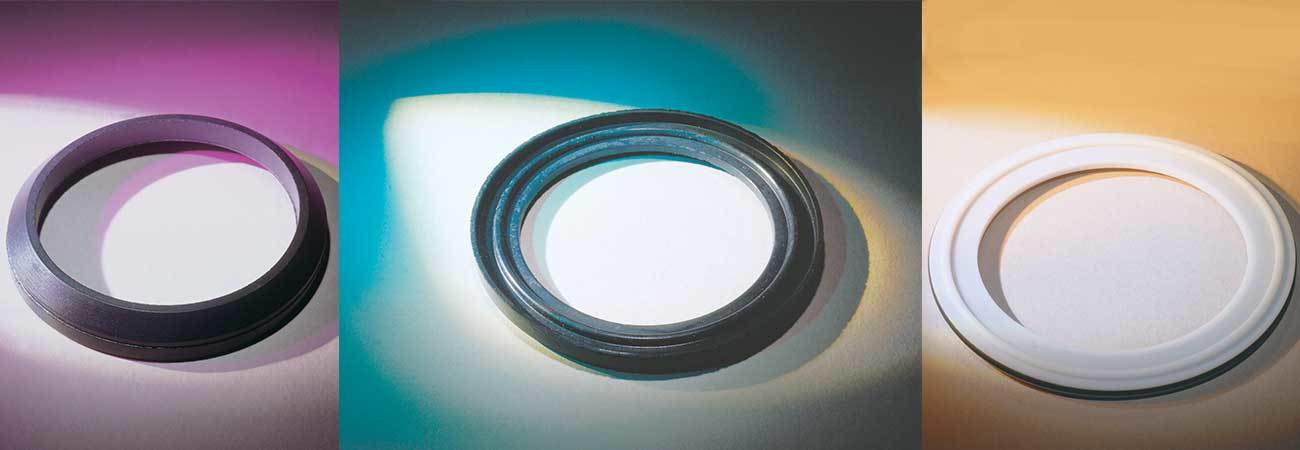
What Are Elastomers?
Elastomers are materials that can return to their original shape after being stretched or deformed. This characteristic makes them essential in many applications, from industrial seals to everyday rubber bands. The choice of elastomer might seem like a minor decision, but it can have a major impact. Seal material that is a poor fit for the application can cause any number of problems, from swelling to peeling or cracking.
To help avoid these issues, analyze the elastomer already used in the same or a similar application. Variables such as chemical compatibility, temperature, pressure, and mechanical wear can make it challenging to predict with certainty what the best material will be. Several materials will work in most cases, but some elastomers will live longer than others. If a gasket is performing well and is low in cost, there is usually no need to change materials.
When an elastomer must be selected for a brand-new application, several important guidelines must be considered.
What Are the Properties of Elastomers?
Elastomers are a diverse group of materials with unique properties that make them suitable for a wide range of applications. Understanding these properties is key to selecting the right elastomer for your needs. Here’s an overview of the various properties and types of elastomers:
The Properties of Elastomeric Material
Elastomers are characterized by their ability to stretch and return to their original shape, thanks to their elastic polymers and cross-linked structures. They exhibit high elasticity and flexibility, which are crucial for applications like seals and gaskets. The glass transition temperature is a critical factor, as temperatures below this threshold can reduce flexibility and affect the material's rubber-like characteristics. The properties of elastomers include:
- Elasticity: The ability to return to their original shape after deformation.
- Flexibility: Ease of stretching and bending without breaking.
- Durability: Resistance to wear and tear, including abrasion resistance.
Elastomeric Materials
Elastomeric materials are specifically engineered to provide superior flexibility and resilience. These materials include both natural rubber and various synthetic rubbers. Key aspects of elastomeric materials are:
- High Stretchability: Can be stretched significantly without permanent deformation.
- Resilience: Ability to recover quickly from deformation.
- Versatility: Can be formulated for specific applications such as automotive gaskets or industrial seals.
Unsaturated Elastomers
Unsaturated elastomers contain carbon-carbon double bonds in their molecular structure. This type of elastomer includes materials like butadiene rubber and styrene butadiene rubber. Key features of unsaturated elastomers are:
- Chemical Reactivity: Reactivity with other chemicals can be higher due to unsaturated bonds.
- Elastic Properties: Provide good elasticity but may require additional chemical treatments for enhanced performance.
Natural Rubber vs. Synthetic Rubber
Natural and synthetic rubbers are transformed into elastomers through methods like vulcanization and injection molding. Natural rubber is derived from the latex of the rubber tree and is known for its excellent elastic properties and flexibility. On the other hand, synthetic rubber is manufactured from various synthetic materials and can be engineered to offer specific advantages:
- Natural Rubber: Good flexibility and resilience but can be sensitive to environmental factors.
- Synthetic Rubber: Offers better resistance to heat, chemicals, and weathering. Examples include nitrile rubber and butyl rubber.
Butyl Rubber and Other Synthetic Elastomers
Butyl rubber is a synthetic elastomer with exceptional air impermeability and chemical resistance. It is often used in applications requiring high thermal resistance and oil resistance. Other synthetic elastomers include:
- Nitrile Rubber: Known for its resistance to oils and fuels.
- Elastomeric Polymers: These are thermosetting elastomers, which are cured to achieve a stable, heat-resistant material.
Saturated vs. Thermosetting Elastomers
Saturated elastomers have fully hydrogenated polymer chains, which make them less reactive and more resistant to aging and chemicals. Thermosetting elastomers are cross-linked during curing, resulting in a rigid structure that cannot be re-melted. Key differences include:
- Saturated Elastomers: Improved chemical resistance and thermal stability.
- Thermosetting Elastomers: Permanent deformation resistance and high mechanical properties, suitable for harsh environments.
Elastomeric Properties
The elastomeric properties of a material include its ability to return to its original shape after deformation, its flexibility, and its resistance to environmental factors. These properties are essential for applications requiring durability and performance under varying conditions.
Understanding these various properties helps you choose the most appropriate elastomer for your application, ensuring optimal performance and longevity.
Understanding Elastomer Standards and Selection Criteria
Standards and Compliance
Consider the standards that must be met. It's easy to think that EPDM is EPDM, but there's more to the story. An EPDM o-ring could be perfectly safe for sanitary processing or, depending on how the o-ring is made, contain potentially harmful components that can leach into finished goods.
Understand which specific standards are important for an individual application. Are the components considered food grade? Do they meet Food and Drug Administration (FDA) standards? Biopharmaceutical processors often require that seals meet USP Class VI standards.
Sometimes, a choice in curing compounds is offered. For instance, some silicone rubber is cured using peroxide. However, most companies can't allow peroxides to contaminate their product, so silicone cured with platinum is typically preferred in sanitary applications.
Types of Seals
The job the elastomeric material will perform determines the type of seal needed. A static seal that sees no movement may have different needs than a dynamic seal. An abrasive product will be harder on a dynamic seal (like a valve seat or o-ring on a moving component) than on something passive, like a Tri-Clamp gasket.
Sugar syrups can be tricky with dynamic seals. In general, they are very benign and work well with any elastomer. However, sugar crystals can build up on seals, sometimes called “plating.” On a valve seat, the crystals can behave like sandpaper when the seat closes, quickly wearing away the seat. PTFE, also known as Teflon, is often the best choice when abrasion is a concern.
Another consideration for the type of seal is the resilience of the elastomer. Buna and EPDM have good resilience and “bounce back” more like natural rubber when compressed. They're great for a good seal, especially after repeated compression (such as in a butterfly valve seat or a gasket for a fitting often removed). Viton can be somewhat flexible and resilient but becomes less flexible at lower temperatures.
PTFE, known as Teflon, has no memory and can “cold flow,” causing it to change shape when compressed. Often, it provides an adequate seal for the first use, but if a Tri-Clamp fitting is removed and replaced with the same gasket, there might be some leakage. For this reason, envelope-style gaskets were created. These are PTFE gaskets with a core of a more resilient material like EPDM, combining the mechanical and chemical toughness of PTFE with the resilience of rubber.
Chemical Compatibility
Chemical compatibility is crucial when selecting elastomers for specific applications, as the interaction between the elastomer and chemicals can significantly affect performance and longevity. Understanding how different elastomers react to various chemicals helps you choose the right material for your application.
General Guidelines
- Buna (Nitrile Rubber): Known for its excellent resistance to oils, fuels, and hydrocarbons. It generally performs well with aliphatic and aromatic hydrocarbons. However, Buna is less effective with strong acids and oxidizing agents. Typical concentration limits are up to 30% for acids and up to 10% for caustics but can vary depending on specific formulations and conditions.
- EPDM (Ethylene Propylene Diene Monomer): Performs well in water, steam, and alkaline solutions. It is generally not suitable for oils and fats. EPDM is used in applications with exposure to high concentrations of alkaline substances, up to 50%, and moderate concentrations of acids, up to 10%.
- Viton (Fluoroelastomer): Offers superior chemical resistance to oils, fuels, and acids. It can withstand exposure to strong acids and bases, making it suitable for harsh chemical environments. Viton is resistant to concentrated acids and bases, with limits typically around 10% for strong acids and 20% for strong bases.
- PTFE (Polytetrafluoroethylene): Known for its exceptional chemical resistance, PTFE can handle nearly all chemicals, including strong acids and bases. It is particularly useful in environments with high chemical exposure and has broad compatibility with up to 100% concentrations of various chemicals.
- Silicone Rubber: Performs well in high-temperature environments but has limited resistance to oils and fuels. Silicone rubber is suitable for applications involving exposure to water and mild acids, with concentration limits around 10% for acids and bases. Specific limitations depend on the formulation.
Specific Chemical Compatibility
- Acids:
- Buna: Acceptable up to 2% concentration.
- EPDM: Generally good, up to 10% concentration.
- Viton: Excellent resistance, acceptable for concentrations up to 10%.
- PTFE: Resistant to almost all acids, even at high concentrations.
- Silicone: Fairly good, but you should check compatibility charts for specific acids.
- Bases and Caustics:
- Buna: Effective up to 2% caustic concentration.
- EPDM: Can tolerate higher concentrations, typically up to 50%.
- Viton: Performs well with caustics, suitable for up to 20% concentration.
- PTFE: Excellent resistance to caustics, even at high concentrations.
- Silicone: Consult compatibility charts for specific base concentrations.
- Hydrocarbons and Oils:
- Buna: Excellent resistance to oils and fuels.
- EPDM: Poor resistance; not recommended for oil exposure.
- Viton: Superior resistance, ideal for high-temperature oils.
- PTFE: Outstanding resistance to hydrocarbons.
- Silicone: Limited resistance, suitable for non-oil applications.
Temperature Resistance
Temperature resistance is a critical property for elastomers in high- or variable-temperature environments. Elastomers must maintain their physical properties and performance despite exposure to extreme temperatures. Temperature tolerances can vary by formulation and application, so be sure to check manufacturers' datasheets to verify the information for the specific material you will be working with.
Temperature Ranges and Performance
- Buna (Nitrile Rubber): Typically operates effectively within a temperature high up to 225°F (107°C). It can handle occasional temperature peaks but may degrade over prolonged exposure.
- EPDM (Ethylene Propylene Diene Monomer): Suitable for temperatures up to 275-300°F (135-149°C). It remains flexible at low temperatures and maintains performance at high temperatures, making it ideal for outdoor and steam applications.
- Viton (SFY, Stem-Resistant Fluoroelastomer): Can withstand high temperatures to 400°F (204°C). It is known for its thermal stability and can handle continuous exposure to high temperatures without significant degradation.
- PTFE (Polytetrafluoroethylene): Teflon exhibits excellent performance at temperatures to 450°F (232°C). PTFE maintains its integrity in extreme temperature conditions, making it suitable for high-temperature applications.
- Silicone Rubber: Effective over a wide temperature range to 450°F (232°C). It remains flexible at low temperatures and maintains performance in high-temperature environments, but prolonged exposure to temperatures above 446°F (230°C) may lead to degradation.
Exotic Materials
Exotic elastomers are specialized materials designed for high-performance applications where standard elastomers might not suffice. These materials often provide enhanced properties for specific industrial requirements.
Kalrez
- Performance Characteristics: Kalrez is a brand of perfluoroelastomer, known for its outstanding chemical resistance and high-temperature stability. It maintains its integrity in harsh chemical environments, including strong acids, bases, and solvents.
- Temperature Range: Effective from -20°C to 330°C (-4°F to 626°F). It remains stable across various temperatures, making it suitable for extreme conditions.
- Applications: Commonly used in chemical processing, pharmaceutical manufacturing, and aerospace applications where chemical resistance and high-temperature stability are critical.
PEEK (Polyether Ether Ketone)
- Performance Characteristics: PEEK is a high-performance thermoplastic known for its excellent mechanical properties, chemical resistance, and high-temperature stability. It is resistant to many solvents, acids, and bases.
- Temperature Range: Suitable for temperatures up to 250°C (482°F) and can handle short-term exposure to higher temperatures.
- Applications: Used in demanding applications such as aerospace components, medical implants, and high-performance seals where both mechanical strength and chemical resistance are required.
Delrin (Polyoxymethylene)
- Performance Characteristics: Delrin is a high-strength, low-friction thermoplastic with good dimensional stability and resistance to wear and impact. It is also resistant to various chemicals, though not as broadly as PEEK.
- Temperature Range: Effective from -40°C to 120°C (-40°F to 248°F).
- Applications: Commonly used in precision engineering, automotive components, and consumer goods where durability and low friction are essential.
Specialty Materials
- PTFE/Stainless Steel Composites: These materials combine the chemical resistance of PTFE with the mechanical strength of stainless steel, offering enhanced performance in high-temperature and aggressive chemical environments.
- Metal-Detectable Elastomers: These elastomers contain metal particles that allow them to be detected by metal detectors. They are useful in food processing and pharmaceutical industries to prevent contamination from broken gaskets or parts.
Understanding these advanced materials' properties and applications enables you to make more informed decisions for specialized industrial needs.
Price Considerations
The cost of a gasket often influences a decision. A gasket that costs less than 50 cents in Buna could run $1.50 as an envelope gasket with Viton and PTFE or $5.00 in a PTFE/stainless compound like “Silverback” or “Tuf-Steel.” The goal is to find the lowest-cost material that will meet your needs.
The only way to ensure which elastomer will work best is to experiment with the lowest-cost option that meets application requirements. There might be some trade-offs; Viton might provide a longer life than EPDM, but it may not be worth the added cost. Depending on the application, a higher-cost elastomer is not always a better choice.
In many cases, Buna is a low-cost option, while EPDM can be higher priced. PTFE, platinum-cured silicone, and Viton are in a higher price class, with Viton usually the highest. Envelope gaskets and specialty compounds can be higher still. Prices can change depending on the availability of an elastomer.
If you are unsure how to choose the best elastomer, check out the main page for gaskets and the accompanying elastomer guide, or call a CSI representative at 417.831.1411 for help with the decision-making process.
Conclusion
Choosing the right elastomer is crucial for ensuring the effectiveness and longevity of your seals and gaskets. By considering factors such as chemical compatibility, temperature resistance, and the specific requirements of your application, you can select an elastomer that meets your needs and performs reliably. Whether you are working with natural rubber, silicone rubber, or thermoplastic elastomers, understanding each material's properties and performance characteristics will help you make an informed decision. While cost is a factor, it should be balanced against performance to achieve the best overall value.
What Are Elastomers: FAQs
What are elastomers, and how do they work?
Elastomers are materials that exhibit significant elasticity. Due to their polymer chains and cross-links, they can return to their original shape after deformation. Their elastic properties make them ideal for seals and gaskets in various applications.
What is the difference between thermoplastic elastomers and thermoset elastomers?
Thermoplastic elastomers can be melted and reshaped multiple times without altering their properties. In contrast, thermoset elastomers are cured through a chemical process that makes them rigid and unable to be remelted. Each has its advantages, depending on the application.
How does chemical compatibility affect the choice of elastomer?
An elastomer's chemical properties, such as resistance to acids, oils, and caustics, determine its suitability for specific applications. For example, PTFE is known for its high chemical resistance, making it ideal for harsh environments.
What are some key properties to consider when selecting an elastomer?
Key properties include thermal resistance, abrasion resistance, chemical resistance, and elastic properties. These characteristics will influence the elastomer’s performance in different conditions, such as high temperatures or chemical exposure.
How do temperature and mechanical wear affect elastomer performance?
Temperature can impact elastomers' physical properties and elasticity, potentially leading to degradation. Mechanical wear, such as abrasion and repeated compression, can also affect the longevity and effectiveness of the elastomer.
What are the advantages of using synthetic rubbers over natural rubber?
Synthetic rubbers often offer enhanced chemical resistance, thermal stability, and mechanical properties compared to natural rubbers. They can be tailored for specific applications, providing better durability and reliability.
Expert Bio
Liz Braden, Manager - Employee Development and Continuous Improvement
With a degree in Manufacturing Engineering from Missouri University of Science and Technology, Liz Braden has experience in the food processing industry where she is adept at managing production and improving plant processes. Her experience at Central States Industrial (CSI) includes working as a Technical Service Representative and Customer Service Manager. She is now Manager of Employee Development and Continuous Improvement where she looks after training, resource development, and CSI’s continuous improvement program.
ABOUT CSI
Central States Industrial Equipment (CSI) is a leader in distribution of hygienic pipe, valves, fittings, pumps, heat exchangers, and MRO supplies for hygienic industrial processors, with four distribution facilities across the U.S. CSI also provides detail design and execution for hygienic process systems in the food, dairy, beverage, pharmaceutical, biotechnology, and personal care industries. Specializing in process piping, system start-ups, and cleaning systems, CSI leverages technology, intellectual property, and industry expertise to deliver solutions to processing problems. More information can be found at www.csidesigns.com.