Flow Meters vs. Load Cells: How Do They Measure Up?
While flow meters and load cells are two very different technologies, their paths may sometimes overlap, making it a challenge to decide which technology would be best suited for a certain application.
A flow meter may come in many forms, but it is usually an in-line device that measures the rate or flow of a fluid—either in volume or mass. A load cell is a device that allows for the contents of a tank or vessel to be weighed.
Flow meters work at their best when measuring continuous flow, rather than frequent starts and stops, and they are great for bulk receiving by weight or volume (depending on the meter). A variety of system checks and balances can also be performed with flow meters, from ensuring adequate flow rate during clean-in-place (CIP) cycles to helping to regulate the flow of a pump.
However, a flow meter is located in the tubing, upstream from a tank, which means there is a difference between what the meter reads and what is truly in the tank. Programming changes can correct for the delays in measurement caused by this difference, but they can be imprecise and require frequent calibration.
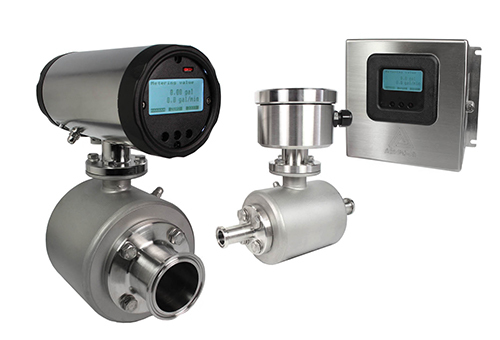
A load cell measures the weight of the tank itself, so delays are minimized. Load cells offer a particular benefit when dealing with products that don’t usually work well with flow meters. Liquids with entrained air or bubbles may give meters trouble, but they are no problem for load cells. Even dry ingredients like powders can be measured just like liquid adds using load cells.
With Alfa Laval’s shockproof digital load cells, a non-contacting capacitive sensor is mounted inside the load cell body. Since the sensor is not placed under direct load, there is never a deflection or deformation of the sensing device, thus providing accurate measurements time after time. Load cell system is a good solution for precise batching.
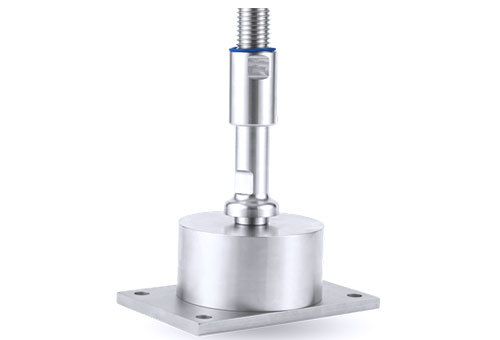
In addition, newer “capacitive” load cells (like the shockproof digital load cell from Alfa Laval) offer high accuracy in weighing and are virtually maintenance free. Unlike traditional load cells, capacitive load cells maintain their accuracy every time they are used, without ever needing to be recalibrated, even over years of abuse.
One downside of using load cells could be that only one ingredient can be added and measured at one time, while using multiple flow meters could allow for simultaneous additions of different products.
In a side-by-side comparison, adding load cells to one tank may initially cost more than one flow meter. However, if multiple flow meters are needed for each tank, the initial investment can often be lower for a load cell setup. After the initial investment, load cells can pay for themselves by minimizing ingredient waste and quality issues due to batching errors.
There are many options and styles available that can be customized to fit user needs, whether load cells or flow meters are the best fit for an application.
ABOUT CSI
Central States Industrial Equipment (CSI) is a leader in distribution of hygienic pipe, valves, fittings, pumps, heat exchangers, and MRO supplies for hygienic industrial processors, with four distribution facilities across the U.S. CSI also provides detail design and execution for hygienic process systems in the food, dairy, beverage, pharmaceutical, biotechnology, and personal care industries. Specializing in process piping, system start-ups, and cleaning systems, CSI leverages technology, intellectual property, and industry expertise to deliver solutions to processing problems. More information can be found at www.csidesigns.com.