Hastelloy® C-22® & AL-6XN®: How Weld Quality Affects Corrosion Resistance
Super Alloys™ deliver a stable and reliable return on investment by reducing product loss, maintenance costs, and unplanned downtime, which is why processors often decide to utilize tubing and fittings made from — either AL-6XN® (UNS N08367) or Hastelloy® C22® (UNS N06022) — instead of standard stainless steel.
Although 300 Series stainless steels, such as type 316, are corrosion-resistant in many environments, they aren’t corrosion-proof, as many processors have learned the hard way - sometimes within just a few months of installation.
A system's overall service life and susceptibility to degradation depend as much on the corrosion resistance of the welds as that of the base metal - a chain is only as strong as its weakest link.
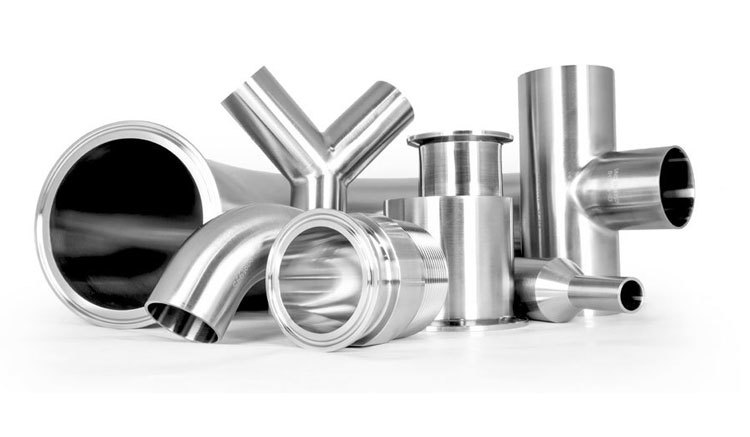
AL-6XN vs Hastelloy C-22
AL-6XN, with about 22% chromium, 24% nickel, and 6% molybdenum, has the highest corrosion resistance among the 300 Series, 4% Mo, and other 6% Mo superaustenitic stainless steels. By comparison, 316L stainless steel has 16–18% chromium, 10-12% nickel, and 2-3% molybdenum. Molybdenum enhances corrosion resistance, especially to pitting and crevice corrosion, in high chloride solutions, and provides increased strength to withstand temperatures typically used in sanitary processing.
AL-6XN was developed to hold up in marine environments that are corrosive due to sodium chloride. It’s now frequently used for food, beverage, personal and home care, and biotech and pharmaceutical processing - products such as ketchup, tomato paste, vinegar-based products, sports drinks, shampoos, toothpaste, and buffer solutions. In some cases, the products themselves are not corrosive, but the chemicals used to clean the system are.
Hastelloy C-22 is a nickel alloy that contains higher levels of chromium and molybdenum than AL-6XN and also contains tungsten (about 3%). The high chromium content provides excellent resistance to oxidizing media, while the molybdenum and tungsten help fight corrosion in reducing media and chloride containing environments. It has superior corrosion resistance in harsh environments like buffer solutions, API, chromatography columns, fish sauce, chili sauce, fabric softeners, and cleaning supplies.
It's critical to keep in mind that the welds joining the parts of your system must have strength and corrosion resistance that are equal to or higher than the Super Alloy used as the base metal. Otherwise, you risk weld corrosion that would mean more work on your equipment sooner, and costs incurred through repairs and downtime. A quality, properly executed weld will help ensure your Super Alloy investment pays off.
Welding Super Alloys is similar to welding standard austenitic stainless steels, quality welds can be readily achieved by using proper weld procedures.
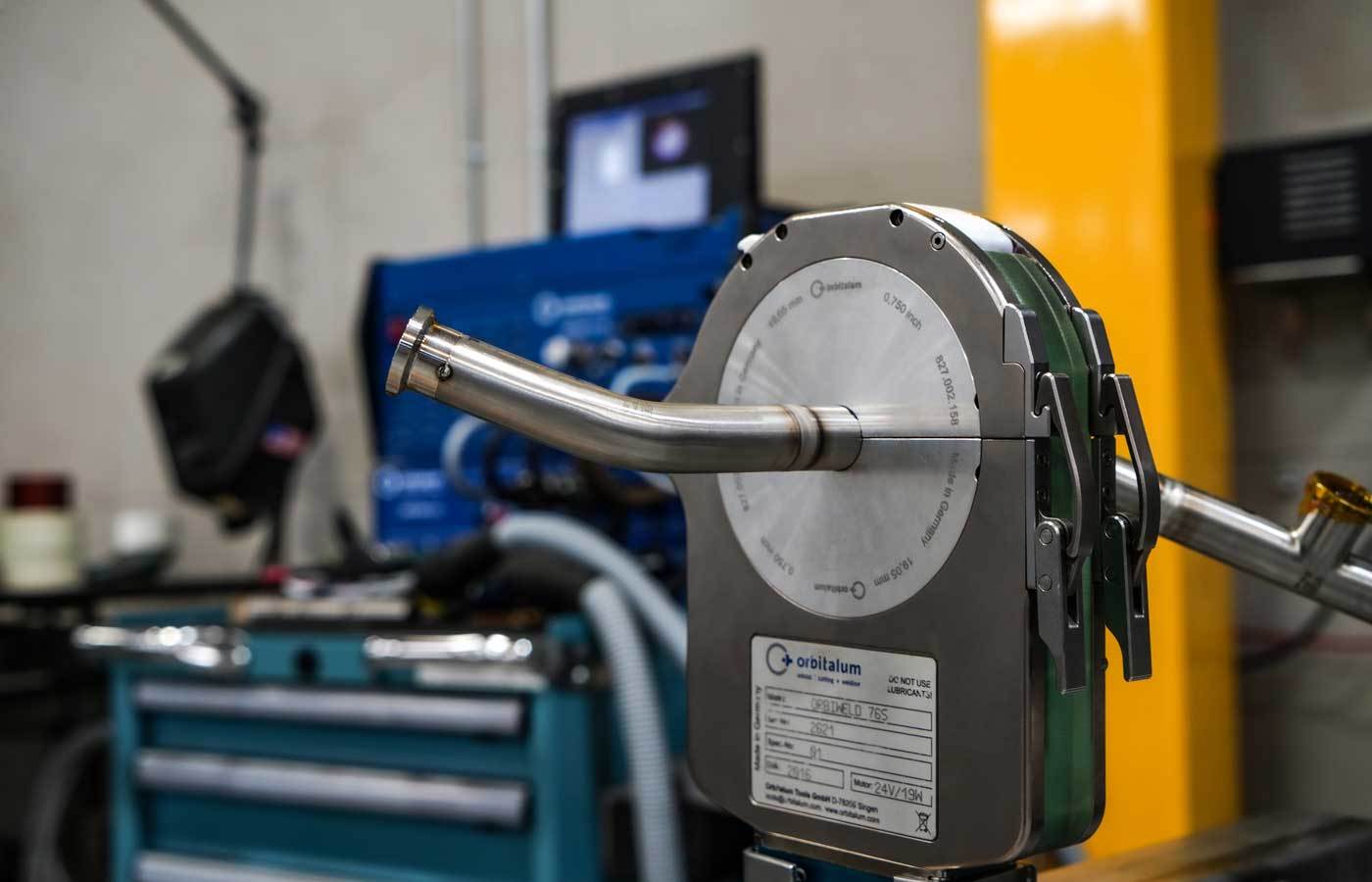
Benefits of Orbital Welding
Super Alloys can be easily welded either manually or with automatic welding equipment. With all the advances in orbital welding equipment that’s evolved over the last 20 years, automatic welding is becoming more attractive to installers and manufacturers.
Orbital welding has many advantages that should be considered when welding super alloys. The primary benefit is consistent and repeatable weld quality. Super Alloys are used in systems where corrosion resistance is a concern and when fittings are properly orbital welded it will give a piping system the added performance of consistent weld quality. CSI has years of experience using orbital weld systems for Super Alloys, so please reach out to us for advice or help.
How Weld Surfaces Affect Corrosion Resistance
A welded fitting has four primary regions, in order of corrosion resistance from most to least:
- Tube base metal - the material that was in sheet form before being shaped into a tube
- Tube weld seam - the weld that joins the sheet edges after the material has been shaped into a tube
- Orbital weld - the weld that fuses system parts together
- Orbital weld HAZ (heat-affected zone) - non-melted areas of the base metal that because of exposure to high temperatures near the weld have undergone changes to their material properties
1. The tube base metal
This is the most corrosion-resistant part of a welded piece. It hasn't been affected or altered by the welding process and retains all the inherent corrosion and mechanical properties of the alloy.
2. The tube weld seam
The tube weld seam is the second least likely place to see failure in a welded piece, however, not all tubing has a weld seam. Super Alloy tube can be either seamless or welded. If seamless, there isn’t a tube weld seam so corrosion potential is eliminated.
Welded tube is susceptible to weld seam flaws that can include mismatched edges, weld undercut, improper weld bead reduction, or weld seam pitting. Welded tubing needs a post-weld solution anneal after seam welding to homogenize the microstructure and restore properties. When done properly, a weld seam will have properties that are very similar to the base metal.
3. Orbital weld
This is the third least prone to corrosion. To achieve the expected corrosion resistance, AL-6XN orbital welds need an over alloyed insert such as a Hastelloy C-22 weld ring, which boosts the alloy content and corrosion resistance. If AL-6XN components are joined with an autogenous weld (no insert), a post-weld heat treatment is required to restore corrosion resistance. Failing to observe these precautions with AL-6XN would make the orbital weld the area most prone to corrosion.
Hastelloy C-22 can be readily welded without an over alloyed insert or post-weld heat treatment and still maintain its corrosion resistance — the post welded, solidified structure maintains adequate corrosion resistance. However, annealing a C-22® weld will remove internal stresses and improve toughness.
Although orbital welds are high quality, they're not immune to flaws if parameters are off. These are a few of the flaws that can be observed in orbital welds:
- Incomplete penetration. A weld bead that doesn't completely penetrate the wall thickness of the weld groove will form cracks or crevices in the weld root where cracks or corrosion can propagate. These defects can happen when proper welding procedures are not adhered to; contributing factors include current setting, arcgap, electrodegeometry, or electrodealignment.
Nickel-based alloys like Hastelloy C-22 are prone to sluggish welding and shallow penetration, increasing the potential for incomplete penetration. Orbital welding programs should use a pulsed current, which helps in controlling the weld penetration without exclusive heat input as well as controlling the weld pool, making the weld bead more consistent.
- Porosity or gases trapped in the weld metal could be generated from moisture in the shielding gas, grease, or dirt on joint surfaces or even inadequate shielding gas flow rates.
- Cracking. Super Alloys such as AL-6XN and C-22 have a microstructure that is fully austenitic, which makes them more sensitive to hot cracking. Common factors that can cause hot cracking are high heat inputs, high levels of undesirable contaminants, and faulty weld assembly design (the bevel angles must be determined correctly).
4. Orbital weld HAZ
This area is the most prone to corrosion. The HAZ, directly adjacent to the orbital weld, is prone to precipitation of undesirable secondary phases and is the area most susceptible to the formation of an undesirable level of heat tint – both conditions that can reduce corrosion resistance. Proper weld procedures, including the use of a consumable insert and a shielding gas, will eliminate these potential problems are avoided and corrosion properties of the HAZ will be very similar to that of the base metal.
Lower heat input allows faster cooling rates and a smaller HAZ, which minimizes microstructure modifications like grain growth and precipitation of undesirable secondary phases and enhances mechanical strength and corrosion resistance.
Differences in Welding Appearance
You and your customers should be aware that AL-6XN and Hastelloy C-22 welds look different than other stainless steel welds.
An AL-6XN weld has non-uniform freeze lines and oxide islands in the weld bead, unlike a 316L weld. The oxide islands are dull or blue-gray and adhere to the surface. Light and dark spots on both the root and face of the weld are also common. The HAZ can be discolored and is generally a little darker than in typical 316L stainless steel welds.
C-22 welds will have oxide islands in the weld bead. The film that forms on the weld pool and solidifies on the weld is composed of high-melting-point oxides. Oxide islands are common and permitted under standards such as ASME BPE (Bioprocessing Equipment).
Some discoloration in the heat affected zone (HAZ) is also common with AL-6XN and C-22 welds and isn’t necessarily the result of improper gas shielding. Other factors that can influence discoloration in the HAZ are finishing processes including:
- tube mill surface conditioning methods such as pickling, passivation;
- mechanical polishing;
- cleaning;
- annealing furnace atmosphere.
Discoloration in the HAZ from these processes is generally darker than that seen in traditional stainless steel materials, but doesn’t indicate a defective weld.
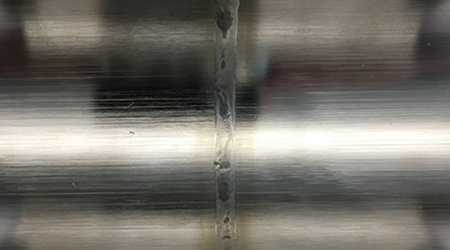
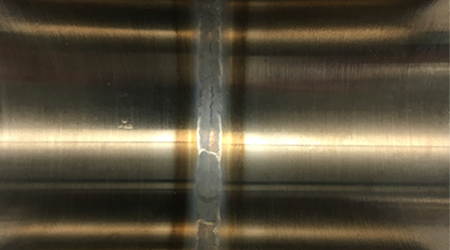
Next Steps
Care should always be taken when deciding to use tubing and fittings made from Super Alloys. Partnering with a trusted company that has a vast experience in Superaustenitic stainless steels and nickel alloys is a great first step!
CSI is the global source for sanitary Super Alloy piping and components for the food, beverage, personal care, home care, and pharmaceutical industries. If you have questions about how AL-6XN and Hastelloy C-22 can improve your processing systems or the welding of Super Alloys, contact CSI at 1-417-831-1411.
ABOUT CSI
Central States Industrial Equipment (CSI) is a leader in distribution of hygienic pipe, valves, fittings, pumps, heat exchangers, and MRO supplies for hygienic industrial processors, with four distribution facilities across the U.S. CSI also provides detail design and execution for hygienic process systems in the food, dairy, beverage, pharmaceutical, biotechnology, and personal care industries. Specializing in process piping, system start-ups, and cleaning systems, CSI leverages technology, intellectual property, and industry expertise to deliver solutions to processing problems. More information can be found at www.csidesigns.com.