Smart Pump Monitoring and Your Digital Transformation
Condition Monitoring
For industries seeking a path to digital transformation, adopting smart monitoring devices and IoT solutions for automatic equipment health reporting is a cost-effective place to start. For example, most manufacturers are looking for ways to protect their operations from unplanned downtime, often while facing the challenge of maintaining systems with a smaller workforce.
Fitting pumps with condition monitoring is a smart move in the digital transformation process. It keeps a constant watch on pump operations and sends quick alerts to prevent issues before they turn into problems.
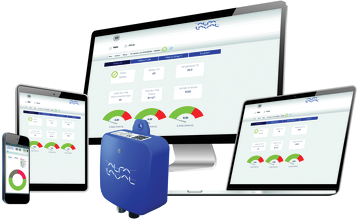
BENEFITS OF CONDITION MONITORING
- Helps operations prioritize service for pumps based on precise data and intelligent diagnostics
- Reduces unplanned downtime by supporting planned and predictive maintenance
- Minimizes staff overtime and rush orders for spare parts
- Extends pump lifetime
- Lowers total cost of equipment ownership
What is the Condition Monitor Sensor?
The Alfa Laval Condition Monitor (CM) is a sophisticated wireless sensor device that attaches directly to pumps, capturing critical data on vibrations and temperature around the clock. This cutting-edge technology is designed to track the health of rotating machinery with precision, using accelerometers that measure vibrations in three axes and an internal temperature sensor to monitor operational conditions continually.
The CM device simplifies the process of condition monitoring, making it accessible and manageable. It collects and digitizes vibrational and temperature data, which are crucial for anticipating maintenance needs and preventing unexpected failures. This data can be accessed directly from the sensor or through a connected network, supporting proactive maintenance strategies that extend the lifetime of equipment and enhance overall plant efficiency.

CM Operation
- Collects vibrational and temperature data from the connected rotating machinery
- Records data digitally
- Transmits recorded data to CM Connect via Bluetooth
In some installation situations, the Condition Monitor cannot be connected to the AI-backed CM Connect network. However, it remains capable of providing important pump data for customer insights.
In many cases, preventative maintenance practices fall short because while there are published intervals for maintaining items, the amount of time a piece of equipment has been in operation is unknown. The standalone Condition Monitor can provide baseline information such as start and stop counts and cumulative run time through the Alfa Laval CM app.
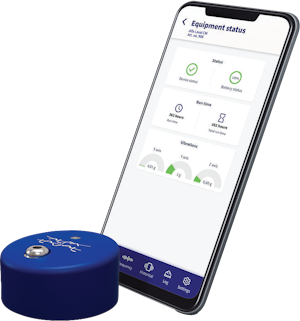
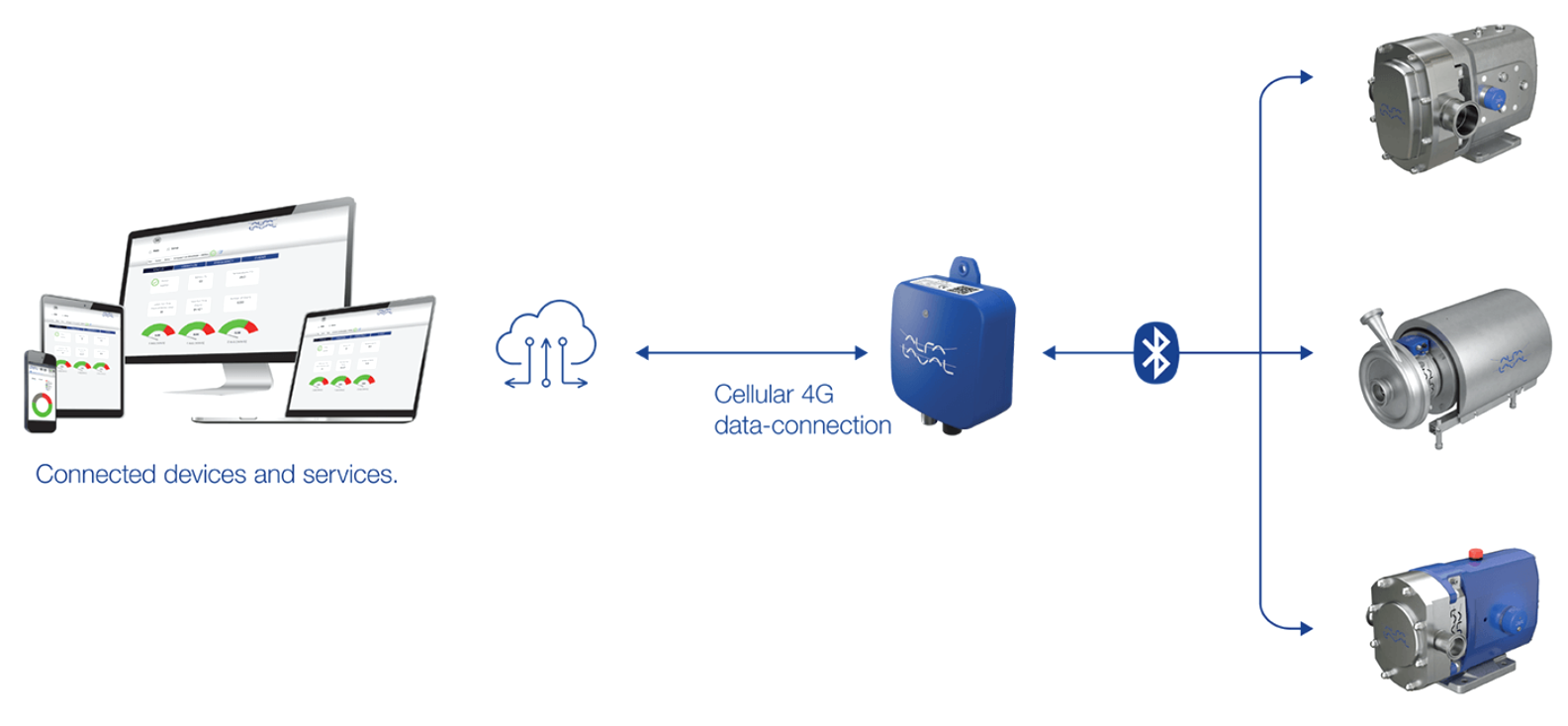
CM Connect for Networked Communication
Alfa Laval's CM sensors are part of an integrated-networked system that includes the CM Connect gateway, enabling seamless data transmission to a cloud-based platform. This networked communication setup allows for real-time monitoring and analysis of equipment health from any location, ensuring that maintenance can be scheduled before issues escalate into costly downtime.
The system's intuitive dashboard presents all relevant data in an easy-to-understand format, highlighting machinery that needs attention and providing actionable insights based on comprehensive trend analyses and frequency data. This approach not only saves valuable maintenance time but also optimizes the operational lifecycle of the pumps.
By integrating CM sensors with the CM Connect gateway, users benefit from an enhanced monitoring system that supports remote and real-time visibility of machine conditions. This holistic view is essential for maintaining the high reliability and performance of critical industrial equipment, ultimately leading to reduced maintenance costs and increased productivity.
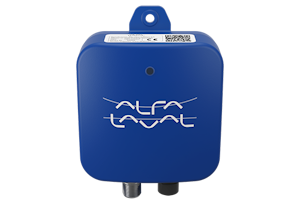
Sample Equipment Report
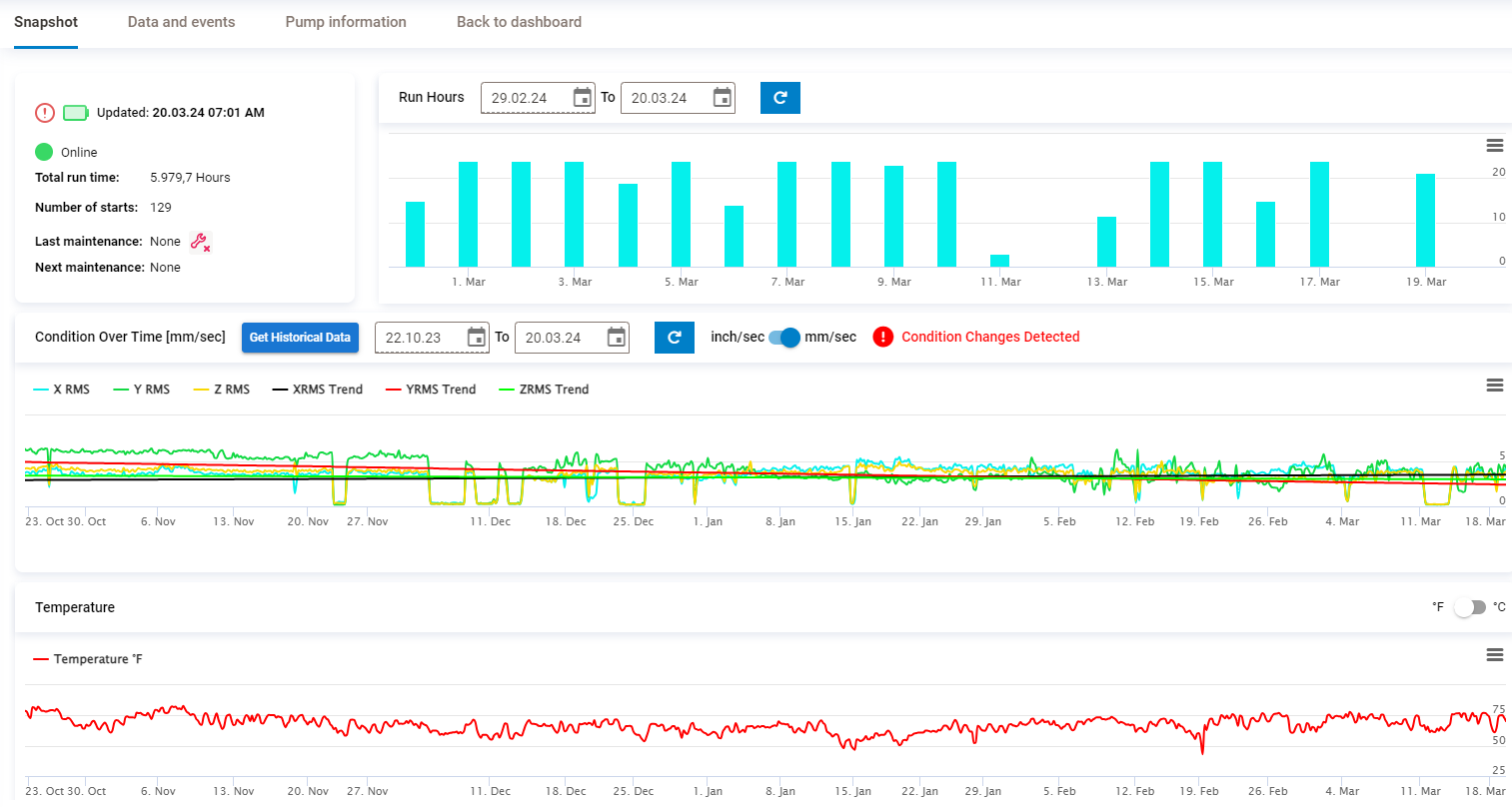
Condition Monitoring in Action
CSI has a customer in the liquid milk industry with a substantial installation base of Alfa Laval pumps featuring the Condition Monitor, connected via CM Connect to the Alfa Laval AI-backed cloud service.
Recently, this customer was notified of ‘Impeller wear and/or imbalance.’ Because the notification from the condition monitoring was specific and timely, the customer was able to find a quick resolution to the issue. They got to a suitable stopping point in their process and, upon opening the pump, discovered that the impeller was making contact and the pump needed to be serviced.
The timeliness of discovery meant that the pump could be salvaged. Without condition monitoring, it likely would have gone undetected until the pump failed.
The customer is adding CM and CM Connect to additional Alfa Laval pumps to take advantage of the digital protection that condition monitoring can provide.
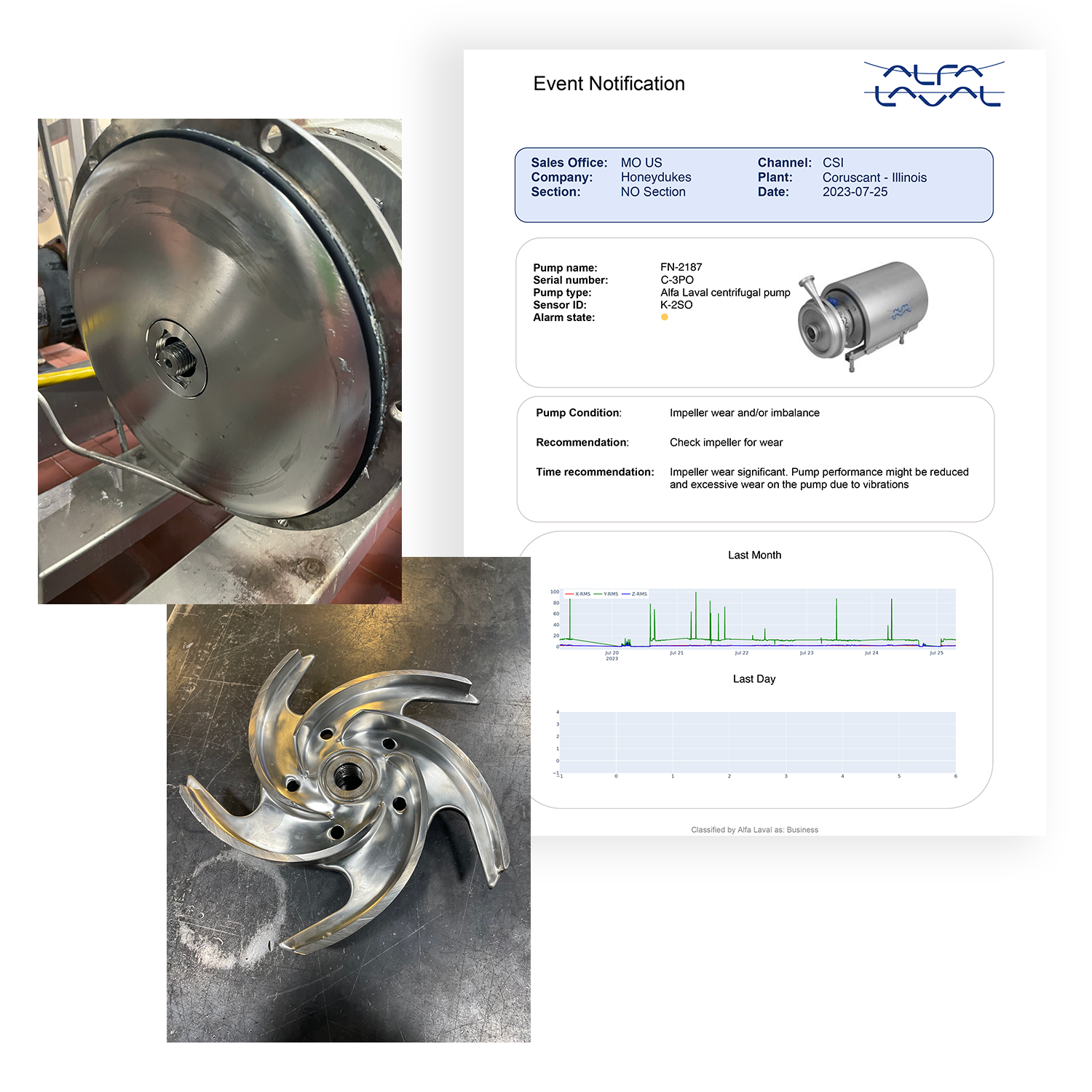

Embracing Digital Transformation
In an industry that can be slow to adapt, CSI and Alfa Laval are leading the way in simplifying and advancing digital transformation. If you want to enhance your manufacturing processes, boost efficiency, and minimize unplanned downtime, consider exploring the possibilities of condition monitoring. Contact CSI today to initiate a discussion on how this technology can elevate your operations.
Next Steps
Contact us today to explore how condition monitoring can revolutionize your processes. Let's discuss your specific needs and how our solutions can be tailored to unlock maximum performance and cost savings for your business.
Call Michael David at (417) 831-1411.
Don't let unplanned downtime disrupt your operations. Take the first step towards operational excellence. Reach out now and let us help you make informed decisions that propel your business forward.
Contributing Author
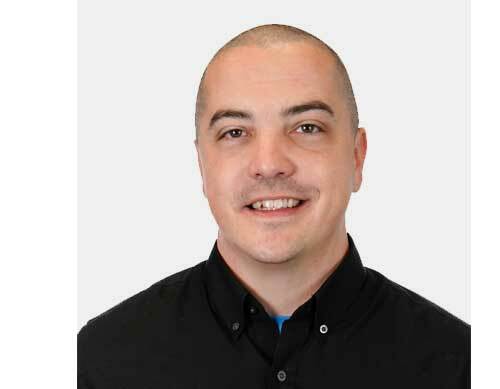
Michael David is the Manager of Pump and Heat Exchange Solutions at CSI. Michael received his B.S. degree in Mechanical Engineering from the Missouri University of Science and Technology, and brings over 17 years of experience in engineering, process design, fluid dynamics, and maintaining equipment for the food, dairy, beverage, biopharm and biotech markets. Michael supports a team of application specialists who focus on Pump and Heat Exchange solutions. He also leads many training initiatives for internal and external customers aimed at developing competence and confidence in the worlds of pumps and heat exchange technology.
ABOUT CSI
Central States Industrial Equipment (CSI) is a leader in distribution of hygienic pipe, valves, fittings, pumps, heat exchangers, and MRO supplies for hygienic industrial processors, with four distribution facilities across the U.S. CSI also provides detail design and execution for hygienic process systems in the food, dairy, beverage, pharmaceutical, biotechnology, and personal care industries. Specializing in process piping, system start-ups, and cleaning systems, CSI leverages technology, intellectual property, and industry expertise to deliver solutions to processing problems. More information can be found at www.csidesigns.com.