How Rotary Jet Heads Save Water, Energy, and Chemicals During Clean-in-place
Process designers recommend rotary jet heads when cleaning requires a combination of high water pressure and chemicals to produce impingement action. In Clean-in-place (CIP), impingement refers to the force of water under pressure and flow to adequately remove soils from the interior surfaces of tanks. Cleaning occurs when the concentrated fluid stream meets interior surfaces.
To achieve cleaning results, the jet heads use an optimized high-impact jet pattern to create jet pressure, or force of impact, to remove residues.
Designers choose rotary jet heads to clean tanks because they use less water, less energy, and less cleaning agent than spray balls. Rotary jet heads rotate in precise, repeatable patterns to achieve full coverage inside the tank and because of the heads’ rotating action and water pressure, they use less water and take less time to clean than static jet devices.
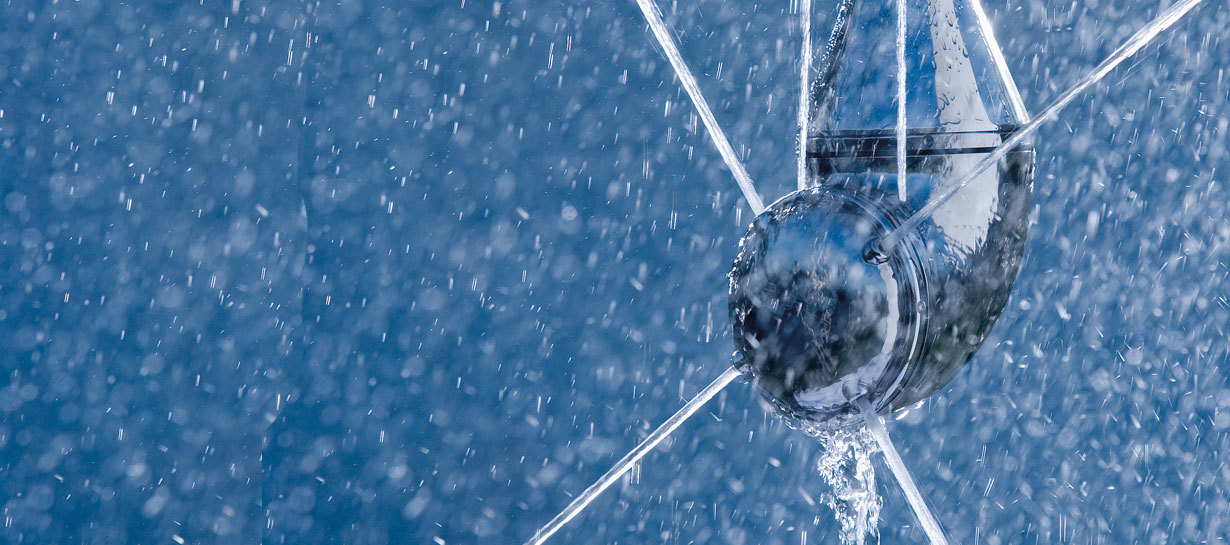
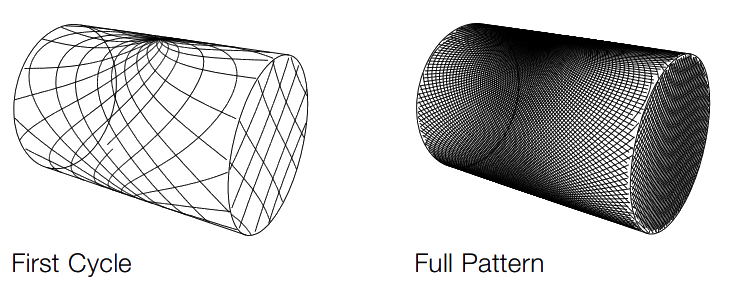
How rotary jet heads work
The flow of cleaning fluid makes rotary jet head nozzles turn on their vertical and horizontal axes. In the first cycle, nozzles deposit a coarse pattern on the tank surface. Subsequent cycles gradually add density to the pattern, until reaching full coverage after several cycles. The operation is fully automatic and provides users with effective quality assurance in tank cleaning.
As Table 1 illustrates, the type of jet head to use depends on tank size, cycle time, and many other variables.
Table 1
Option 1 | Option 2 | Option 3 | Option 4 | |
---|---|---|---|---|
Tank Size | Small to mid-sized | Mid-sized | Mid to large-sized | Large |
Throw Length (max) | 4-24 FT | 19 FT | 45-85 FT | 65FT |
Cycle Time | 8-11 Min | 10-14 Min | 8-12 Min | 8-20 Min |
Working Pressure | 40-1,000 PSI | 30-400+ PSI | 40-400+ PSI | 40-400 PSI |
Recommended Pressure | 50-600 PSI | 30-150 PSI | 50-300 PSI | 50-300 PSI |
Working Temperature (max) | 203°F | 203°F | 203°F | 195°F |
Ambient Temperature (max) | 284°F | 284°F | 284°F | 284°F |
Standards | 2.1 material certificate upon request | 2.1 & 3.1 material certificate upon request | 2.1 material certificate upon request | 2.1 material certificate upon request |
Typical pressure, temperature, and jet pattern specifications for rotary jet heads in CIP remain constant across small and mid-sized tanks. As tank size increases, cycle time and pressure requirements for rotary jet heads also increase.
Download Alfa Laval Tank Cleaner Selection Guide
Complete self-cleaning system
Some rotary jet heads clean themselves inside and out to ensure that the flow of cleaning fluid covers external surfaces of the rotary jet head to reduce the risk of cross-contamination that would cause potential product waste.
- Overlap ensures self-cleaning of the body.
- The nozzle’s concave shape ensures self-cleaning of the nozzle itself.
- Through two holes in the hub, jet streams ensure cleaning of the cone.
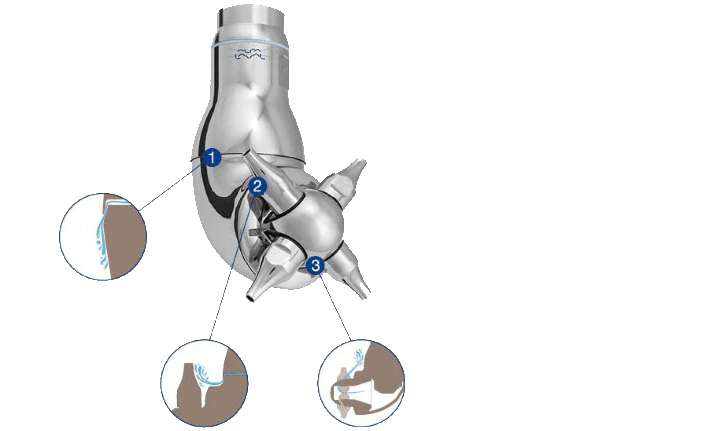
Selecting the right rotary jet head
The choice between rotary spray heads and rotary jet heads depends on application requirements. Jet heads provide higher impingement — impact or mechanical force — than spray heads and are designed to offer the optimal output of force with the least flow and pressure.
Consider several factors when selecting jet heads and their configuration:
- Types of soil being cleaned
In general, simple, easy to clean water-soluble soils can be cleaned by static jet balls because the balls use chemicals, heat, and water to create a cascading action that removes the soil. Rotary jet heads use impingement for hard to clean, dry, sticky, viscous or oil-based products. - Vessel diameter
Vessel diameter and shape determine the flow rate required to meet cleaning requirements. - Available flow rate
Vessel shape and size and tank cleaning device affect CIP flow rate requirements and pump needs, which must be calculated during CIP design. - Available supply pressure
Jet devices have different pressure requirements to operate correctly. Their pressure requirements must be accounted for during CIP design. - Number and type of internal obstructions in the tank
Even though rotary jet heads move, their effectiveness diminishes with the presence of obstructions in a tank such as heating coils, agitators, baffles, or ladders. - Port size
Port size determines jet head size and flow. - Budget
Budget considerations include the number and size of tanks, types of jet devices, system maintenance, and replacement parts.
How cycle configuration affects cleaning
In addition to jet head factors, four cycle factors affect the cleaning action of rotary jet heads during cleaning: time, action, chemicals, and temperature.
Time | Duration of surface exposure to cleaning fluid. |
Action | Type of impingement the jet head delivers during cleaning, dependent on flow velocity and jet device design. |
Chemicals | Amount of chemical per unit volume contained within the cleaning fluid. This includes caustic, acid, and sanitizer. |
Temperature | Amount of heat energy within the cleaning fluid that can be transferred to a surface. |
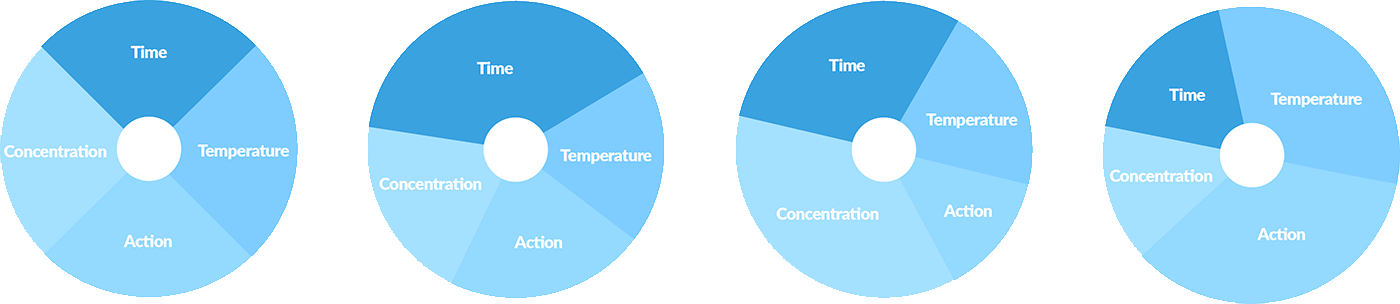
The pie graphs above illustrate various combinations of parameters. An increase in any one parameter decreases the other parameters.
Time
The total amount of time it takes to run a complete cleaning sequence can include a number of different steps (like preparation, programming, wash and rinse, drying, etc.), but the critical “time” element of the cleaning process is the amount of time that cleaning solutions are in direct contact with the product soil. Longer contact times can equal better cleaning, however, increasing impingement can result in better cleaning in shorter cycles. Your wash and rinse cycle times may each be as short as 2 minutes, or they may take up to 19 minutes each depending on system design.
Since the time spent cleaning reduces the time spent producing a saleable product, the goal is to reduce cleaning cycle times as much as possible while still ensuring that the processing system is sufficiently clean and safe. An experienced cleaning expert can determine the right cleaning jet device and cycle times for a particular application based on product and system variables.
Action
The action in a cleaning process is the mechanical force of the cleaning solution that physically dislodges soil from the surface. The amount of impingement needed--and therefore jet devices and pressure required--are important considerations.
Chemicals
The right chemical cleaning agents in the right concentrations make a significant difference in CIP efficiency. The main job of chemicals in any CIP process is to enhance cleaning.
Temperature
Calculating the precise solution temperature is critical to effectively cleaning a system while at the same time reducing energy costs. Some studies have shown that for every one-degree reduction in CIP solution temperatures there will be nearly a 1% reduction in the energy needed to heat the fluid.
Higher solution temperatures can increase the effectiveness of chemicals and mechanical action and can also reduce the amount of time needed to clean properly. Considering the cost of energy to heat the solution, it is important that the temperature of each individual cleaning stage be calculated and controlled as accurately as possible.
Advantages of rotary jet heads
Because rotary jet heads operate at higher operating pressure, they have the advantage of higher impact velocity, which concentrates energy and chemical cleaning agents at impingement points. At the point of impact, the high-velocity CIP stream spreads out, resulting in shear to “scrub” soil from the tank wall.
Rotary jet heads distribute cleaning water while turning on two axes: jets turn vertically while the head turns horizontally. As the jets of water rotate, they create an impingement action on the tank circumference, which allows soaking and cleaning with a greater force than spray balls because rotary heads direct the flow in narrow streams.
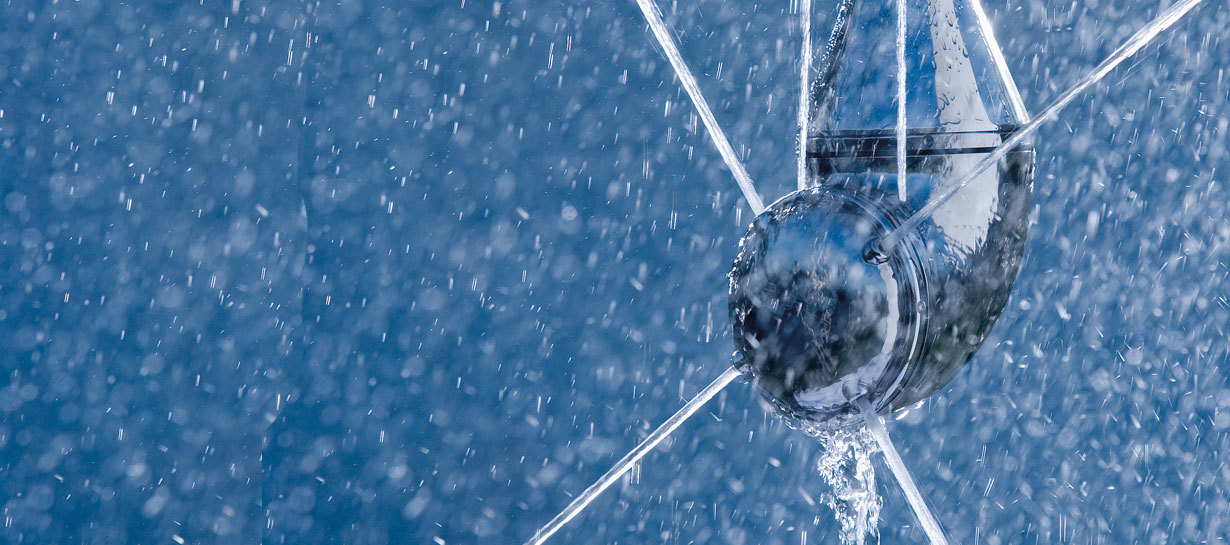
Verifying jet coverage with Riboflavin testing
Summary
To verify the completeness of jet coverage during a CIP cycle, it’s common to perform a Riboflavin test. Testing involves spraying a fluorescent dye solution on the interior of process tanks and cycling the CIP system to study resulting jet patterns and cleaning effectiveness.
Materials and equipment
- Riboflavin powder
- Long wavelength UV lamp for inspecting tank interiors
- Water with a maximum of 30 PPM chloride (plant water) or deionized water
- CIP supply pump: 40 psi [2.7 Bar (g)].
- Water tank and water
- Riboflavin solution jet device that creates a fine mist jet.
- Calibrated pressure gauge(s).
- Calibrated flow meter(s).
General requirements
- Tank must be in its final installed position.
- Perform the procedure after polishing and /or electropolishing the tank.
- Plug or cap all holes, with proper gaskets in place. Components have to be stainless steel, PVC, or brass.
- Have a manual flow control valve, flow meter, and pressure gauge at each CIP manifold inlet.
- Rinse and dry the tank prior to testing.
Dye preparation
- Mix one gram of riboflavin with ten liters of water in a clean polyethylene container to prepare a 200ppm solution (Seiberling, 2008, p. 174).
- Transfer the solution to a suitable hand atomizer.
Set-up
- Ensure tank is positioned in its operating orientation in the test bed and seal all tank openings with proper caps and gaskets.
- Verify that the tank is clean, rinsed, and dried.
- Verify that cleaning devices, jet heads, and wands are properly installed.
Pre-test procedure
- Visually inspect the interior of the tank under UV light.
- Record inspection results.
Dye application
- Observe all confined-space safety regulations.
- Enter tank.
- Jet all interior tank surfaces with dye.
- Exit tank without touching jetted surfaces.
- Inspect the interior of the tank by illuminating all surfaces with a UV lamp to ensure complete coverage (dye fluoresces bright green under UV).
- Re-jet areas that are not completely covered.
Rinsing
- 2-minute ambient rinse
- 1-minute draining
- Repeat for a total of three rinses
Variables that impact test results
The purpose of the riboflavin test is to determine jet-head coverage. The test does not tell you the effectiveness of cleaning, which is a different validation process.
Dale Seiberling notes several variables that can affect the results of riboflavin testing for coverage:
- Riboflavin concentrations
- Rince times
- Drain times
- Rinse cycle repeats
- Rinse cycle lengths
- Rinse temperature
- Vessel cleanliness
- Method of riboflavin drying
- Interfering white light
- Intensity of the UV light
- Interpretation of results (2008, p. 174)
Next Steps
As a hygienic processor, you understand how much reducing water, energy, and cleaning agent use will impact your bottom line.
That’s where Rotary Jet Heads comes in.
Designed to provide high impact cleaning over a defined time period, these devices are automatic and represent a guaranteed means of achieving quality assurance in tank cleaning.
Clean-in-place Buying Guide
This Buying Guide for Clean-in-Place Solutions is a comprehensive resource for anyone who designs, owns, or operates processing systems and wants information about all aspects of CIP Systems.
ABOUT CSI
Central States Industrial Equipment (CSI) is a leader in distribution of hygienic pipe, valves, fittings, pumps, heat exchangers, and MRO supplies for hygienic industrial processors, with four distribution facilities across the U.S. CSI also provides detail design and execution for hygienic process systems in the food, dairy, beverage, pharmaceutical, biotechnology, and personal care industries. Specializing in process piping, system start-ups, and cleaning systems, CSI leverages technology, intellectual property, and industry expertise to deliver solutions to processing problems. More information can be found at www.csidesigns.com.
References
Frank, J. W. & Seiberling, D. A. (2008). CIP jet device design and application. In D. A. Seiberling (Ed.), Clean-in-place for biopharmaceutical processes (pp. 159-174). Drugs and the Pharmaceutical Sciences 173.New York, NY: Informa Healthcare USA.