How to Achieve Valve Automation Through the Use of Control Tops
In any hygienic fluid processing environment, finding ways to increase productivity while reducing the potential for human error can add considerable dividends to the bottom line. Valve automation through the use of control tops is one strategy processors use more and more to accomplish this goal. In this article, we will discuss how automated valves work when connected to a control top and outline the latest technological improvements in these fields.
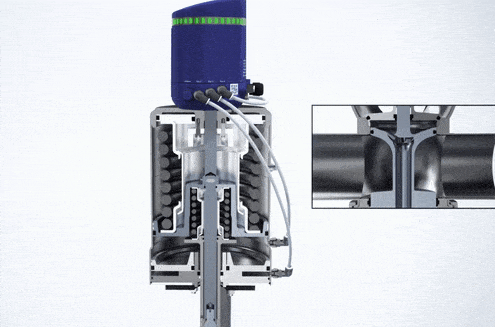
All valves in a process plant contain what are called valve actuators, which are simply the valve mechanisms that actually open and close the valves. Simple valves that are opened and closed manually typically use a lever or a wheel to operate the valve.
Most process plants with a large number of valves, though, have automated valve actuators for opening and closing valves. This valve automation is operated via air pressure, hydraulically, or electronically. Automated valve actuators are commonly found in process plants in the pharmaceutical manufacturing and in the food & beverage processing industries.
They are typically used to control butterfly valves, seat valves, and mixproof valves in process pipelines that contain a large number of valves.
Most types of automated valve actuators may be fitted with an optional device called a control top. As the name implies, control tops are mounted on the top of the valve actuator and are used to provide real-time information, electronically, about the performance of the valve.
Control tops tell process plant operators whether each valve in their system is open, closed, or partially open. Information that is transmitted via valve actuator control tops may be looped into a system network, controlled via a PLC (programmable logic controller), or monitored remotely from a control room in the process plant.
In process piping installations that contain a large number of automated valves, installing control tops on valve actuators can provide a number of advantages.
- They notify the pipeline operator if each and every valve in their system is operating properly, and set to the correct position for the intended operation.
- Automation provides significant cost savings. For example, without a control top a PLC may think that a particular valve is open when it actually isn’t. As a result, thousands of dollars worth of product could accidentally be sent down a waste drain or contaminate a large storage silo.
Due to the peace of mind afforded by control tops, most large process pipeline system operators will pay for the extra cost to install control tops on their automated valve actuators as a risk mitigation measure.
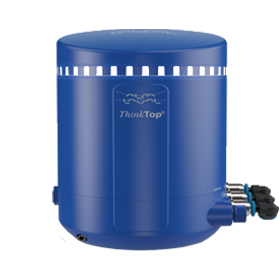
Styles of Valve Automation Control Tops
CSI offers a number of different brands of control tops for use with automated valve actuators. Let’s look at some of the more popular ones in more detail and see how they work.
ThinkTop™ V50 & V70
The ThinkTop™ V50 and V70 control tops from CSI supplier Alfa Laval are designed for use with that company’s diaphragm, butterfly, single seat, and mixproof valves. They are commonly used in the dairy, food, beverage, and biopharmaceutical manufacturing industries.
Sleek and compact, the ThinkTop’s control unit uses a single sensor that may be fitted with up to three solenoids. Inside the ThinkTop’s head, this sensor detects the valve stem movement and valve position to an accuracy of +/- 0.004 inches.
The ThinkTop unit converts electrical output from a PLC to energize or de-energize an air-operated solenoid valve, using the physical sensor target mounted on the stem of the valve actuator. The precise valve position of each and every valve in a process pipeline, then, is essentially managed by the detailed information provided by the ThinkTop control top on each valve actuator.
ThinkTop control units are intuitive, reliable, and quick to set up. The Auto Setup and Live Setup features designed into the ThinkTop recognize the valve type based on its DNA profile and can complete the valve setup without any operator intervention.
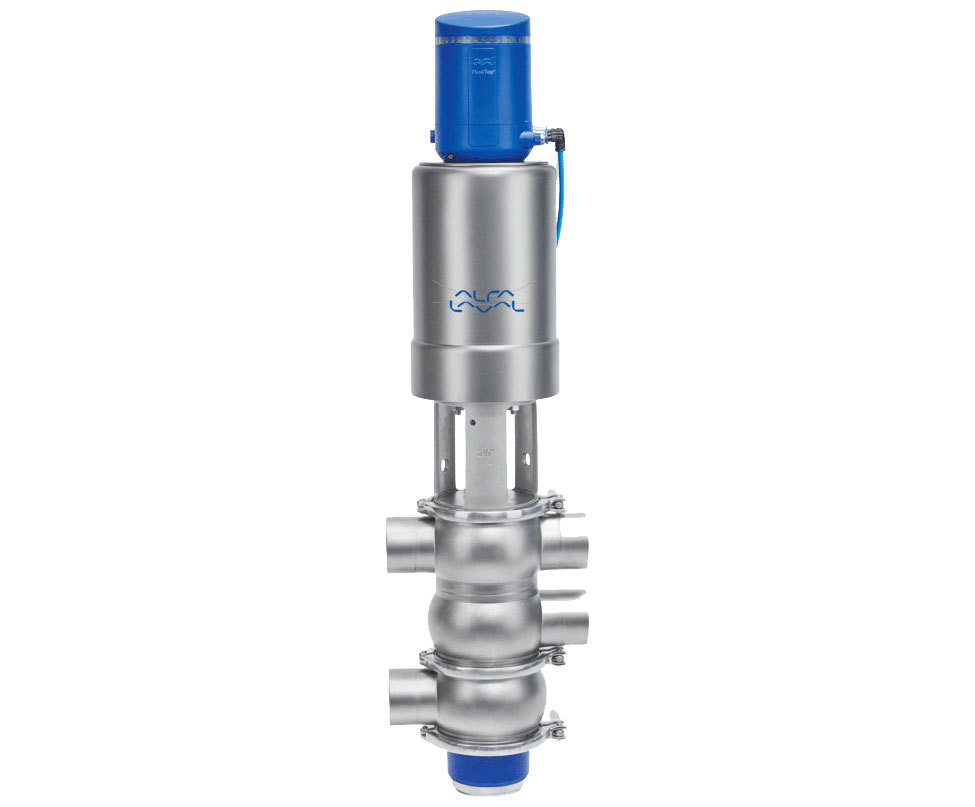
As a result, the setup time can be 90% less than that required for other types of automated control tops.
Finally, the V70 model of the ThinkTop controller comes with a burst seat clean function. This feature controls the optimal open position of a valve and makes it possible to achieve up to a 90% savings in fluids consumed during CIP (clean-in-place) operations.
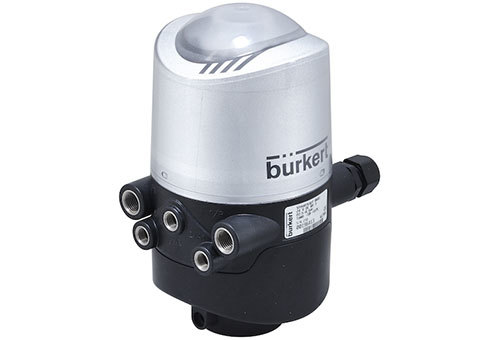
Bürkert Control and Communication
For certain types of requirements, there’s another variant of an automated control top that’s known as a valve positioner. Valve positioners are used to control valves that may need to be partially opened, and not actuated into either the fully open or fully closed positions.
These applications can include valve actuators used with certain steam-based processes, valves used for the mixing of hot and cold liquid media to a precise temperature (i.e., a thermostatic mixing valve), and some sanitary valve applications used for reducing pressure in process pipelines.
For the precise control of throttling and regulating valves that may be operated in a partially opened position, CSI offers a line of specialized control top valve positioners manufactured by Bürkert Control and Communications. Burkert’s valve positioner models range from a simple cabinet-mounted package to a sleek, bus-compatible unit featuring a backlit display and intuitive programming.
Communication Protocols for Automated Control Tops
No discussion of automated control tops for valve actuators would be complete without some words said about the communications protocols that are available for these electronic devices. Since control tops are used to transmit real-time information about the performance of automated valve actuators in a valve system, they are designed to be used and controlled via a communications network in the process plant.
Depending on the specific type of valve actuator that is selected, several types of communications protocols may be available. The default communications network used with valve actuator control tops is typically basic 24 VDC digital wiring. However, more sophisticated controls may be afforded by the use of industrial network protocols (i.e., field-bus networks) that can manage real-time operational control and data integrity in large installations. Several of the most common network protocols include DeviceNet, AS-Interface, CAN bus, and IO-Link. Each is discussed briefly in the following paragraphs.
DeviceNet
A network protocol used in the automation industries to interconnect control devices for data exchange. It utilizes the Common Industrial Protocol over a Controller Area Network Media layer and defines an application layer to cover a range of device profiles. DeviceNet supports data exchange rates of 125 kbit/sec, 250 kbit/sec, and 500 kbit/sec. Depending on the chosen cable type, it can support communications networks up to 500 meters long in a process plant.
AS-Interface
Actuator Sensor Interface is an industrial networking solution used in PLC, DCS, and PC-based automation systems. It is designed for connecting simple field I/O devices such as actuators and sensors in discrete manufacturing and process applications using a single two-conductor cable. Common automation applications for the AS-Interface communications protocol include bottling plants and food production lines.
CAN Bus
A Controller Area Network (CAN bus) is a robust communications standard designed to allow microcontrollers and other devices to communicate with each other without the use of a host computer. Designed originally for multiplex electrical wiring within automobiles to save on copper, it may also be used in automation applications.
For each device on a CAN bus network, the data in a frame is transmitted sequentially, but in such a way that if more than one device transmits at the same time, the highest priority device is able to continue while the others break off.
IO-Link
A short-distance, bi-directional, digital point-to-point wired (or wireless) communications networking standard used for connecting digital sensors and actuators to either an industrial field bus or an industrial Ethernet. It provides a platform for devices that produce and consume data and can be used for economically optimizing industrial automated processes and operations.
Next Steps
In large process pipeline systems that incorporate large numbers of automated valves, adding control tops to your valve actuators makes a lot of sense. Control tops provide precise information about what’s going on with valves, lowering the risk of improper system performance.
And in some cases, as with the Alfa Laval V70 ThinkTop control top and its burst clean capabilities, control tops can also yield a significant operational cost savings.
Contact CSI at 417.831.1411 to discuss your specific needs for control tops on your plant’s automated valve actuators.
ABOUT CSI
Central States Industrial Equipment (CSI) is a leader in distribution of hygienic pipe, valves, fittings, pumps, heat exchangers, and MRO supplies for hygienic industrial processors, with four distribution facilities across the U.S. CSI also provides detail design and execution for hygienic process systems in the food, dairy, beverage, pharmaceutical, biotechnology, and personal care industries. Specializing in process piping, system start-ups, and cleaning systems, CSI leverages technology, intellectual property, and industry expertise to deliver solutions to processing problems. More information can be found at www.csidesigns.com.