How to Get the Most Out of Your Next Factory Acceptance Test
Factory Acceptance Testing (FAT) is an optional step that occurs after design and fabrication to verify that the equipment follows design specifications and operates properly. Customers might choose to conduct an FAT to ensure the components and controls function as required. Testing performed at the factory has several advantages, especially the advantage of identifying problems before the equipment leaves the factory.
Testing lets your team identify discrepancies and learn from the fabrication team how to address them. Conducting FAT is a valuable opportunity that should not be overlooked. Skipping FAT and discovering problems after equipment is shipped and installed can result in costly shutdowns. In some cases, responsibility for malfunctions can become contentious, so finding and addressing them before equipment leaves the manufacturer is wise and much more efficient than discovering them after installation.
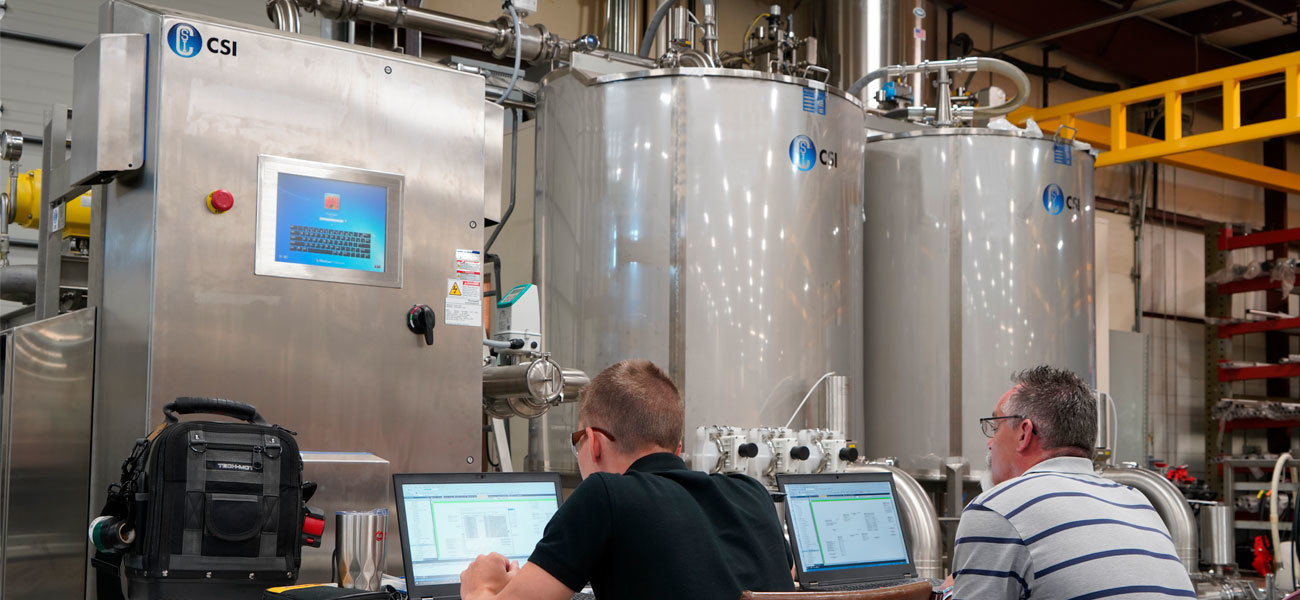
Benefits of a Factory Acceptance Test
- Verify tie-in connection points are where they are supposed to be
- Check accessibility for operation and maintenance
- Check electrical connections
- Verify equipment related documentation
- Verify equipment against project-related drawings and specifications
- Receive hands-on training
- Meet the design, engineering, and fabrication team in person
Basics of a Factory Acceptance Test
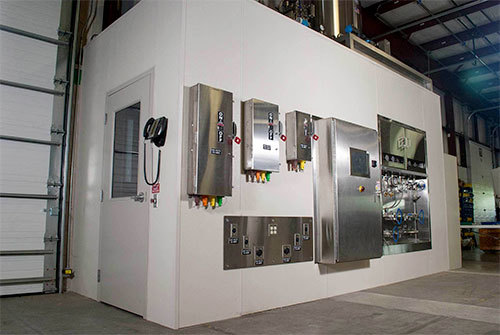
Given the value of factory acceptance testing, choosing a manufacturer who offers FAT is an important first step in the design/build process.
The fundamental process of a FAT execution includes, connecting skid to utilities for preform functional operations, compare assembly to as build drawings, and verify construction to the applicable standards such as ASME-BPE, 3-A Sanitary, or other customer specifications.
Testing gives operators and maintenance personnel valuable information about system readiness before the processing equipment leaves the fabrication center.
A basic FAT checklist includes testing of several important components and functions. Testing is always tailored to customer interests, so while the following items are common on most checklists, they’re not required.
- Connections, to ensure they meet specifications for type, size, and location
- Control panel location and installation
- Drain connections, type, size, and location
- Overall dimensions
- Workmanship
- Welding and weld documentation verifications
- Major equipment and materials of construction
- Documentation: supplier documentation, data sheets, drawings, and certifications
- Pressure testing, report verification
- Valve materials of construction and locations
- Verify material type and finish to line classifications
- Review Quality Control documentation
FAT options vary by type, scope, and scale of equipment. The tables below include items commonly recommended, but not required, for testing.
Identification | |
---|---|
Skid Identification (CSI equipment tag) | ASME BPV Identification tag & stamp |
Components tagged per P&ID | Customer defined markings |
Connections: types, size & location | Major Equipment--location , square & plumb |
Control panels-location, square & plumb | Drain connections--type, size & location |
Structural Frame & Assembly Dimensionals | |
---|---|
Frame workmanship (square & plumb) | Visual Weld Inspection of structural welds |
Connections: types, sizes, and locations | Major Equipment: location, square, and plumb |
Control Panels: location, square, and plumb | Drain Connections: type, size, location |
Overall Length, Width, and Height | Mounting Plate Locations & Hole Pattern |
Vessel or Major Equipment | |
---|---|
Vessel per data sheet / drawing. | Equipment per data sheet / drawing |
External visual inspection | Pressure equipment certification (ASME Stamp) |
Materials of construction | Supplier documentation package |
Processes Piping | |
---|---|
Pressure Testing | Drainability (Slope) of piping |
Piping support adequate | Meets configuration as detailed on drawings |
Review piping per P&ID | Valve orientation per drawing |
Materials and Finishes | |
---|---|
Piping finished per line classifications or applicable standard | Equipment and component finishes per specification or applicable standard |
Piping material of construction per line classifications or applicable standard | Equipment and component material of construction per specification or applicable standard |
Documentation | |
---|---|
Weld documentation per ASME BPV section IX and BPE | CSI Certificate of Conformance for the skidded system |
Receiving Inspection documentation, including material examination logs, Material Test Reports, Material Verification (PMI), Certificate of Conformance for elastomers and Surface finish compliancy | Weld Logs and weld examination documentation per ASME BPE |
RInspector certifications for Visual Testing | Passivation logs and other process certifications |
Turn Over Package per VDR requirements | Installation, Operation, & Maintenance manuals |
Vessel Nameplate Review
For ASME pressure vessels, a nameplate review verifies pressure, temperature, material of contrustionand a National Board registration. This review ensures that the vessel meets the skidded systems design requirements.
Motor Data Verification
As part of document review, this step verifies motor manufacturer, model, and serial number. Also confirms that motor classification meets specified class and division standards.
Who should participate in testing?

Manufacturers who offer FAT encourage A&E experts and end-user representatives to take advantage of testing. They recommend that the people most familiar with skid specifications and processing requirements take part to ensure testing of key performance requirements.
Having two or more participants in the evaluation helps with efficiency, so one can review documentation while another inspects equipment and tests functionality. Depending on system complexity, additional testing personnel can provide cross-functional perspectives on compliance, electrical, piping, welding, maintenance, pumps, valves, component accessibility, and other operational issues.
Involving all stakeholders in creating test plans for system functionality and failure conditions helps make testing valuable.
For example, getting input for the test plan from machine operators, quality control, and maintenance staff as well as process engineers gives you a broader view of the testing you need.
FAT areas in fabrication centers have resources for connecting skids to water, steam, compressed air, and power utilities. Centers may provide project managers as needed to help customers with the testing process along with shop, engineering, and design personnel.
FAT gives operators an opportunity to functionally test a piece of equipment before it leaves the shop, giving everyone a chance to discuss questions and modifications.
Testing can cover a variety of inspection points based on specific requirements and unique equipment specifications. Typical FAT areas at the fabrication center include electrical power, clean steam, hot and cold water, clean air, and other utilities for testing skid systems, clean-in-place (CIP) systems, and custom fabrications.
Comprehensive inspection can include a range of conformity checks and verifications to ensure the equipment measures up.
- Contract audit: review of the original agreement to ensure all contractual obligations are met
- Water testing: simulates system operation, provides proof of functionality, and verifies fabrication against data sheets, user manuals, and other relevant documentation
- P&ID (Piping and instrumentation diagram) audit: verifies all lines and components are present and installed as specified in the P&ID
- Inspection: Checking that components are new, anchored correctly to the skid, and built according to specification
Testing may be basic, such as testing of main components, or may include more thorough inspecting and testing of subassemblies. For example, pump testing may include a net positive suction head (NPSH) test.
Sending someone who is familiar with processing needs, specifications and tolerances helps ensure an efficient and cost-effective trip to the manufacturing center. While manufacturers will typically have personnel on hand to help with testing and to answer questions, you want to have your own experts on hand to run the tests and check the specifications that matter most.
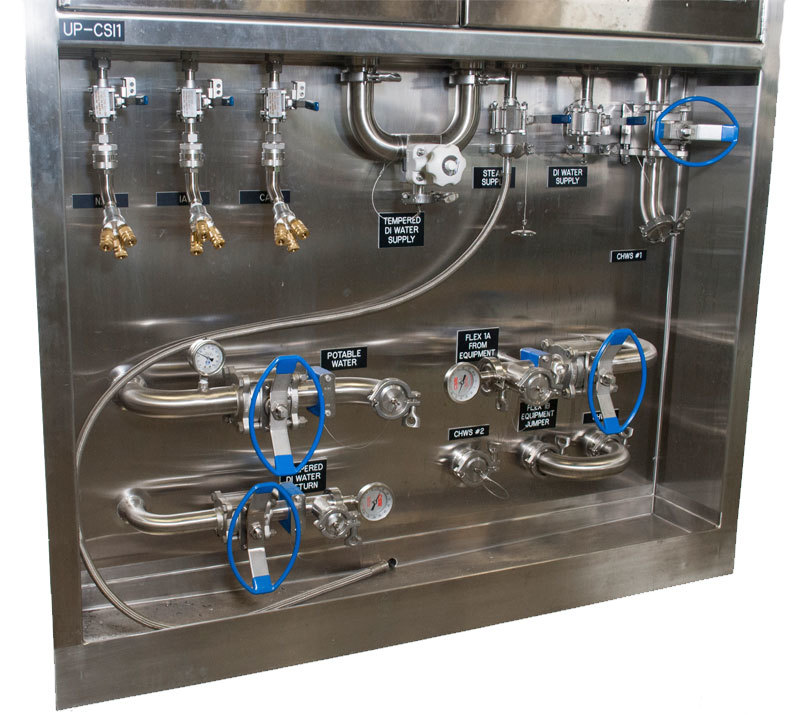
FAT schedule
To ensure a productive test, your FAT schedule should outline a list of items for testing on specific days and allow enough time for reviewing the punch list.
As you make your schedule, consider these questions:
- What processing functions do you want to test?
- Air
- Water
- Electrical
- Vessel and pipe testing?
- Size and footprint dimensions?
- Connections (placement, height, accessibility)?
- What materials and finishes do you want to inspect?
- Software testing? Describe what you want to test: interlocks, alarms, setpoints, and so on.
- What are your documentation requirements?
- Personnel list? (People who know system requirements, operational needs, maintenance, and accessibility requirements and know how to verify performance standards).
Scalable testing
Some skids designed for food, dairy, and beverage plants include software that automates performance and reporting. Software testing, from pre-wash to final rinse, ensures the system is configured to reach predetermined setpoints for flow, temperature, and chemical concentration.
In the case of CIP 2.0, testing gives operators hands-on experience with its software interface and usability, onboard user manuals, cleaning verification functions, cloud connectivity, safety alerts, and predictive maintenance.
During software testing, users run through scenarios to ensure hardware and software perform according to specifications.
Thorough HMI (operator interface) review – Verify buttons and sequencing. Review all screens to understand how to navigate and run the equipment.
Functional Testing – Check components and instrumentation to confirm setpoints and limits.
Performance Testing – Run mechanical verifications, cross-reference with P&ID and electrical drawings.
Review Alarms and Messages – Execute alarms and review messages on the HMI.
Mechanical Verification – Check surface finishes and piping slopes, BOM and P&ID tagging verification, dimensional check.
Next Steps
Don’t bypass factory acceptance tests. Rushing to start production by taking shortcuts or bypassing FAT altogether can result in problems that have to be fixed in the field, where shutdowns are expensive and time consuming.
ROI and FAT
While manufacturers typically don’t charge for testing, customers do incur costs for travel and stays for factory testing. When weighed against the possibility of installation obstacles or processing shutdowns, testing always pays off in hands-on experience with equipment and in valuable learning from expert fabrication partners.
Designed to be among the best in the industry, CSI’s FAT area includes ample electrical power, clean steam, hot and cold water, clean air, and more utilities are piped into a 200-square-foot control room with an additional 750 square foot testing area. To learn more about Factory Acceptance Testing with CSI, contact us today!
ABOUT CSI
Central States Industrial Equipment (CSI) is a leader in distribution of hygienic pipe, valves, fittings, pumps, heat exchangers, and MRO supplies for hygienic industrial processors, with four distribution facilities across the U.S. CSI also provides detail design and execution for hygienic process systems in the food, dairy, beverage, pharmaceutical, biotechnology, and personal care industries. Specializing in process piping, system start-ups, and cleaning systems, CSI leverages technology, intellectual property, and industry expertise to deliver solutions to processing problems. More information can be found at www.csidesigns.com.