Jacketed Pipe Design for Effective Jacketed Piping Systems
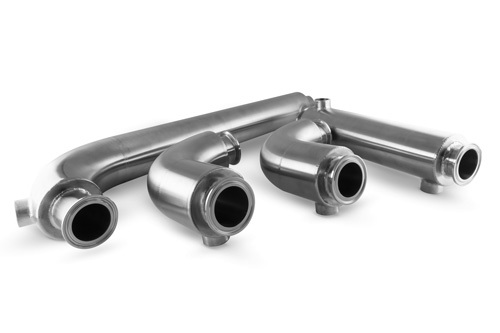
For process engineers and plant managers in the sanitary processing industry, you're always looking for ways to improve and maintain your system efficiencies.
In the language of processing systems, jacketed pipes and tubing are essentially tubes within tubes. The inner pipe transports the product.
Surrounding this product-carrying tube is an outer tube, or jacket, that contains a media fluid — such as steam, hot or cold water, or glycol. This can be a heating or cooling medium, depending on the processing requirements.
This jacket has inlet and outlet ports for the media, pumped through the outer tube to heat or cool the materials flowing in the inner, product-carrying tube. This allows for precise temperature control.
Jacketed piping and tubing can be an effective solution in process piping systems used to convey very viscous fluids, such as honey. In this case, the outer pipe jacket contains a heated liquid that warms the fluid flowing through the product pipe, making it easier to pump through process lines.
A jacketed pipe or tubing is ideal for controlling a fluid's viscosity, especially for products that are shear-sensitive or contain large particles.
Typically, jacketed pipe systems can operate at a wide range of temperatures. For example, the jacketed tubing systems built by CSI are designed for media temperatures ranging from 34°F to 205°F and product temperatures ranging from 24°F to 300°F.
8 Considerations in Designing a Jacketed Piping System
Jacketed tube systems are more complex than standard process piping and require more engineering to ensure that they perform as intended. A number of design considerations must be taken into account when designing and laying out jacketed systems.
1. Fluid Pressure
The fluid flowing in the product side of the tubing must operate at a higher pressure than the process fluid flowing in the media side of the tubing. This ensures that in the event of an unforeseen failure in the process piping, the product is pushed into the media tube rather than being drawn into the product line and causing product contamination.
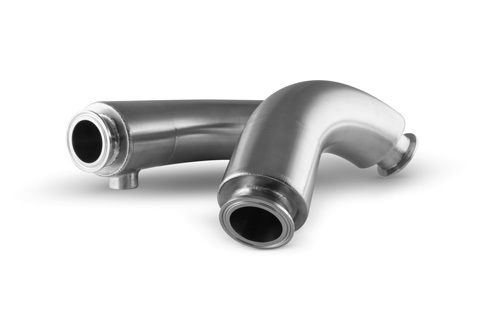
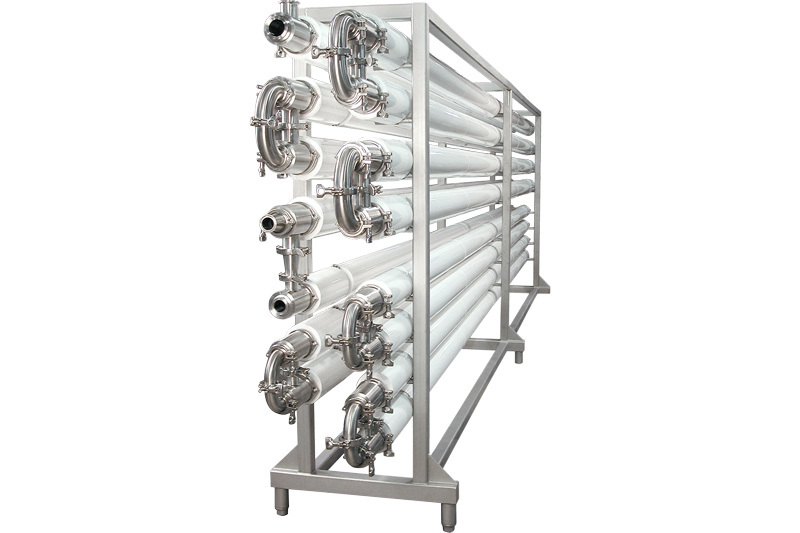
2. Media Port Locations
The media inlet port for the system should be located at the lowest point in the process piping, and conversely, the outlet port should be located at the highest point. This ensures that the media will fill the jacketed pipe before exiting the system and perform the job for which it is intended.
3. Slope
Jacketed piping should also be installed with a 1% slope in the line to facilitate complete system draining.
4. Fluid Flow
The system must be designed so that the media fluid flows in the opposite direction of the product flow. This improves temperature control at the desired rate of the heating or cooling of the product to accommodate thermal expansion and temperature regulation.
5. Pipe Breaks and Joints
Tubed piping systems should be designed with minimum piping breaks or joints. Each break, both for the media and product lines, has a direct cost impact (i.e., the physical costs of the components) and an indirect cost impact (i.e., the preventative maintenance costs) on the overall cost of the system.
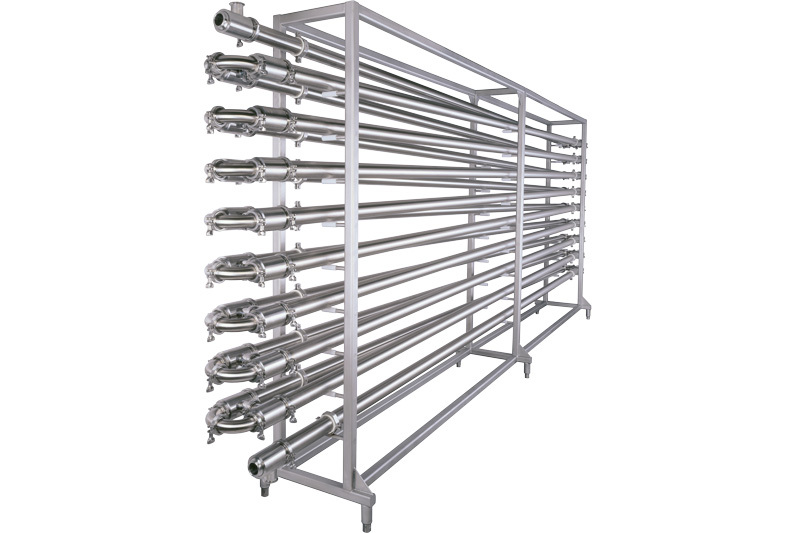
6. Annular Space Between
Optimize the annular space between the product and media tubes. This prevents the product from solidifying or scorching and similar problems.
7. Piping Stress
High stresses can result in the jacketed tubing system if the product core and media jackets operate at significantly different temperatures or are made of different materials. For this reason, it's a good practice to perform a piping stress analysis on a jacketed piping system, anticipating all core/jacket temperature combinations and external loading.
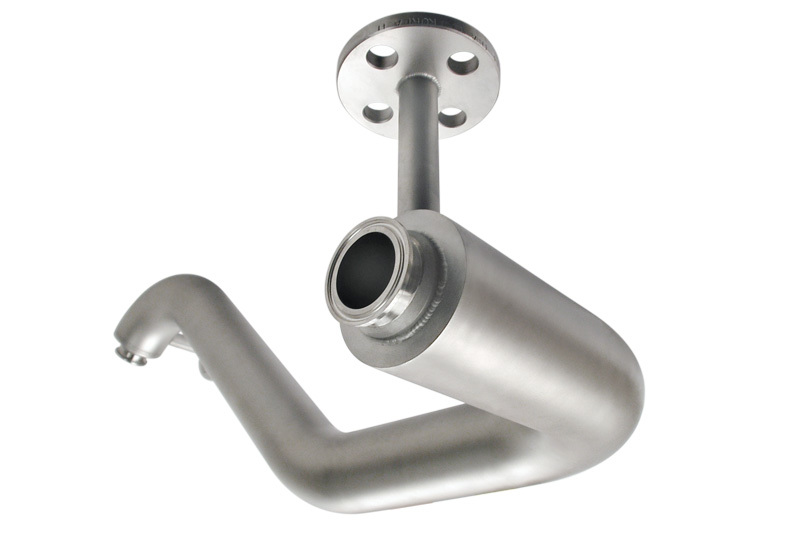
8. System Components and Layout
Finally, consider the following when designing a jacketed tubing system:
- Requirements for peripheral insulation around the jacketed tube (e.g., wrapped fiberglass or polyfoam).
- Thermal differences and expansions between the product and media lines, taking into account cycle times and durations
- Types of piping section connectors used (i.e., expansion joints versus welded connectors).
- There is a potential for crevice corrosion on the media side (this impacts the materials used in the jacket construction).
- Internal supports are needed for the product piping.
- The requirements (if any) for turbulence mechanisms in the pipeline include flow disruptors, fins, and wraps.
Jacketed Pipe and Tube Connectors
As may be imagined, connectors used in jacketed tubing systems are also more complex than those found in standard process piping. Considerations must be given to the types of connectors used for the product-carrying pipe (i.e., the inner tube), the media pipe or the jacket pipe (i.e., the outer tube), and the types of connectors used (if any) to connect the media pipes being used in two separate jacketed systems.
In this latter case, the assumption is that each jacketed subsystem in a more extensive process piping system can share a common media source so the media fluid can travel from one jacketed system to another.
The typical connectors used for each application include the following:
- In product pipes, the fluid being transported is considered to be sanitary, and any typical sanitary connector pipe connector may be used (e.g., butt weld fittings, Tri-Clamp® connectors, and bevel seat fittings).
- The fluid being transported in the media pipes is not sanitary, so a sanitary pipe connector is not required. Typically, National Pipe Thread connectors are used to connect the media pipes.
- Hose connectors are commonly used to connect two separate sections of media-carrying pipes between jacketed subsystems.
With the wide variety of connectors that may be used in jacketed tubing systems, CSI has considerable experience designing and building these systems. We work with our customers to fit nearly any jacketed tubing connector required to meet a particular application.
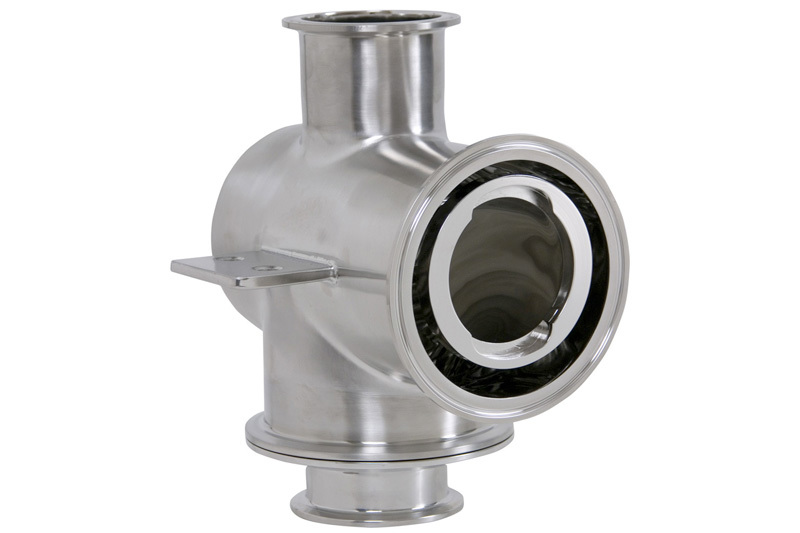
Pipe Jackets or Tube Jackets?
On initial consideration, jacketed fluid processing systems made with pipes versus tubes would appear preferable based on the strength and durability of pipes and valves. However, pipe jacket systems do bring considerable downsides:
- Using pipe as a jacket adds a lot of weight to the system, requiring the mounting structure (hangers, supports, piping racks, etc.) to be constructed of heavier-gauge materials to support the extra weight
- Jacketed system products with a mechanical external finish—often a requirement in sanitary system applications—are more readily available commercially as tubing than piping. Using pipes, then, adds cost to achieve a uniform, cleanable surface.
CSI has received customer questions about the pressure ratings for tube-based jacketed systems versus pipe-based systems. In short, the theoretical bursting pressure of tube-based jacketed systems far exceeds the operating pressures of typical media systems. In other words, other media system components would fail before pressure could collapse or rupture the internal product tube.
Next Steps
Jacketed piping or tubing can be an efficient and effective solution in process piping systems used to convey very viscous fluids, such as honey.
However, these specialized piping systems are complex and require some expertise to design and install properly. Here, CSI can help.
We're experts in process piping system design, engineering, and construction, and we can help you with your requirements for a jacketed tubing system. Call us at 417-831-1411 for more information.
ABOUT CSI
Central States Industrial Equipment (CSI) is a leader in distribution of hygienic pipe, valves, fittings, pumps, heat exchangers, and MRO supplies for hygienic industrial processors, with four distribution facilities across the U.S. CSI also provides detail design and execution for hygienic process systems in the food, dairy, beverage, pharmaceutical, biotechnology, and personal care industries. Specializing in process piping, system start-ups, and cleaning systems, CSI leverages technology, intellectual property, and industry expertise to deliver solutions to processing problems. More information can be found at www.csidesigns.com.