Preventive Maintenance: Keeping it Current
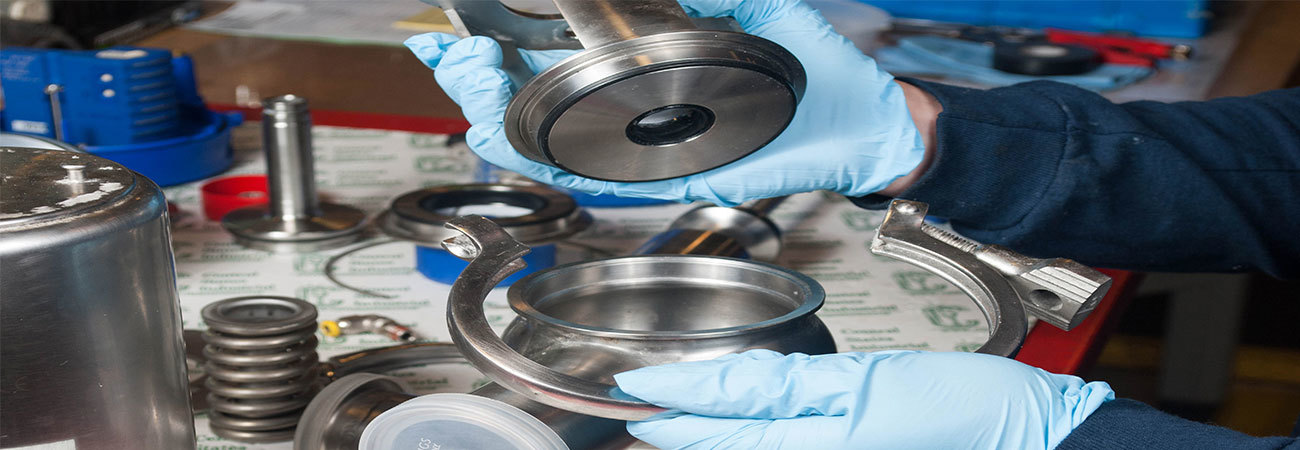
In the food processing world, a well organized and well-executed preventive maintenance (PM) program is essential to sanitary operations. It's no secret that well-maintained sanitary equipment performs better, lasts longer, and saves more money by improving product safety and production uptime.
Nearly all food processors have a PM program, but if complacency sets in, results suffer. A good preventive maintenance program must be current and thorough to be effective. You can improve your PM with better documentation, more predictive maintenance, ongoing training, temporary/reactive maintenance, and periodic preventive maintenance evaluation.
Up Your Documentation Game
Documentation equals traceability, and traceability is imperative if something goes wrong with processing equipment, you have to conduct a root cause analysis, or are audited by a third party.
Whether your PM records are hard copies or electronic, they're only as useful as they are current, complete, and accurate. Using computerized maintenance management software (CMMS) helps with organizing and tracking your PM activities, and it saves a lot of time and confusion when assessing PM activity of particular processing equipment or clean-in-place (CIP) systems.
If your PM documentation is still mostly manual and your budget is limited, developing a CMMS in-house using Excel or Access is a good alternative. If you are able to make the investment, one of the many commercially available CMMS software products can make your maintenance documentation tasks fast and simple.
How To Improve Preventative Maintenance Documentation
Update Your Inventory List
Equipment assets come and go, so keeping your list of equipment requiring preventive maintenance up to date will make your work more efficient. To be complete, your equipment inventory should include asset descriptions; make, model, serial number, asset number, location, and responsible department. Create your own checklist, or use one of the many ready-made templates available. To keep the inventory list accurate, create a system to ensure the list gets updated when equipment is added or eliminated.
Re-Evaluate Your Preventive Maintenance Schedule
Your PM schedule is documentation that you have a plan to keep your equipment running well. Schedules typically include daily, weekly, monthly, quarterly, and annual PM tasks. Most processing equipment will be subject to more than one schedule cycle, such as perhaps a daily visual inspection, a weekly cleaning and a quarterly replacement of gaskets and seals. Also, compare your PM schedule to the production schedule to minimize downtime. Maintenance and repair can often be made between production runs so downtime is minimized. If necessary, schedule a single shut-down to do all necessary PM tasks at once.
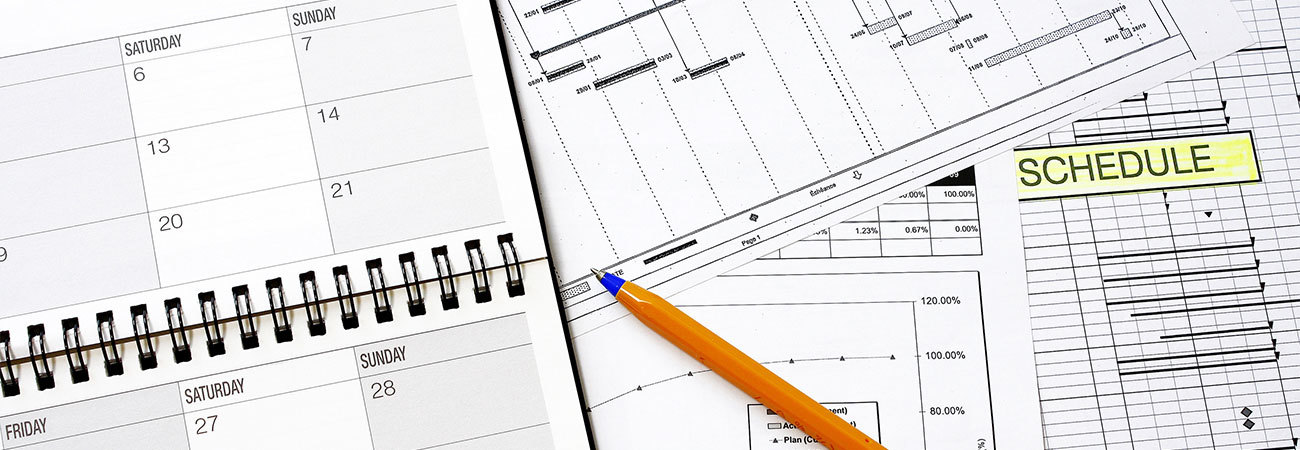
Prioritize Your Processing Equipment
Assess the potential risk factors for each piece of equipment by implementing some "asset risk assessment" practices. This will help you identify the equipment with the highest potential impact on food safety, the ones with the most critical impact on food production, and the ones that would create the most costly downtime if something were to go wrong. All equipment is important, but focus extra attention on the assets that play the most crucial roles in your processing environment.
Ensure All Maintenance Procedures are Formally Documented
Your maintenance procedures are the roadmap for your PM program. Keeping them accurate, complete, and up-to-date helps you avoid costly roadblocks. Review and understand the manufacturer's guide for each asset and update your procedural documents as needed so that your procedures meet the manufacturer's recommendations. Review and document their recommendations for maintaining the equipment properly. Your procedures should include detailed descriptions of what needs to be done, how it should be done, who should do it, and when they should do it. Record small or routine tasks such as gasket changes and machine lubrication, and avoid rushing through equipment reports. Remember: thorough preventative maintenance records are part of compliance requirements for Hazard Analysis Critical Control Point (HACCP) programs and the Food Safety Modernization Act's (FSMA) Hazard Analysis and Risk-based Preventive Controls (HARPC) provision.
Document Time and Costs
Keep track of maintenance time and expenses for all processing equipment and clean-in-place systems. This will help when you start the process of determining whether to get a new piece of equipment or not. Define and document key performance indicators and metrics to demonstrate the PM program's contribution to overall plant performance (for example, total uptime vs downtime, improvements in repair costs, and repair time reductions).
Advantages of Predictive Maintenance
A predictive maintenance (PdM) strategy is most effective for assets with critical operational functions and potential failure characteristics that can be predicted through monitoring, such as CIP tanks, tubes, pipes, and pumps. Consider PdM for the equipment that ranks high on your asset priority list and those that would be costly and time-consuming if they failed.
While preventive maintenance is a schedule of tasks driven by the average or expected life cycle of processing equipment and fittings, predictive maintenance is based on the actual condition of the equipment. PdM is all about monitoring the condition and performance of your equipment during normal operation, analyzing that data and using the information to help you avoid breakdowns and reduce or even eliminate some unnecessary PM tasks.
An investment in PdM helps you stay one step ahead of equipment failures.
Making Your PM Program More Predictive
Industrial manufacturers of food, beverage, and pharmaceutical products have a variety of options for improving predictive PM.
Vibration Analysis
Vibration sensors can detect potential performance failures in equipment like motors and pumps. Vibrations caused by bearing wear, unbalanced, misaligned or bent shafts, eccentric rotors or sheaves, gear mesh issues or general mechanical loosening can be detected and fixed before they become an untimely and costly failure.
Infrared Testing
Infrared cameras can detect areas of unusually high temperature caused by excess friction or other abnormalities.
Motor Condition Analysis
Checking the current draw in motors can indicate the condition of the motor windings, rotor, and supply circuit. It provides a picture of the general health of the motor.
Lubrication and Oil Analysis
Sometime it's not enough to just follow asset's recommended oil change schedule. Conducting a periodic analysis of the equipment's lubrication fluids can determine wear and potential failure by measuring the presence of water or other contaminants.
Acoustic Analysis
Sonic or ultrasonic testing can locate steam, liquid, or gas leaks, pump cavitation and abnormal electrical or radio signals. It can also detect harmonic changes caused by excessive bearing wear or shaft imbalances.
Ongoing Training
When it comes to preventive maintenance, training isn't an expense - it's an investment. Give your PM program a boost by investing in training for your maintenance staff and operators who may be performing some of the PM tasks. And don't forget to document the training time. These ideas for PM training could pay you big dividends:
- Regular in-house reviews of all procedures and documentation requirements for industrial process equipment.
- Factory-offered repair and maintenance training specific to your process systems.
- General classes on PM program organization, scheduling, and monitoring.
- Coaching on proper maintenance management.
- Seminars about relevant new technologies, diagnostic instrumentation and techniques.
- Education on interpreting repair and maintenance historical data to plan future needs.
- Classes on root cause analysis, vibration analysis, or other analysis techniques.
Don't let your PM program be stagnant. Help it grow with your business.
Prepare for Temporary and Reactive Maintenance
Not all equipment failures can be prevented or predicted, so don't just expect the unexpected: be prepared for it too. Temporary or reactive (emergency) maintenance is inevitable, so review your approach to these situations to make sure you're well prepared to keep your plant running. Your asset risk assessment techniques will help you identify the pieces of equipment that need a plan for temporary or reactive maintenance.
Temporary Maintenance
If you don't already have them, establish and document of procedures for temporary repairs. Identify and inventory the materials and parts you need to keep the assets running until proper repairs can be made.
Reactive Maintenance
You can't keep a backup for every single part in the plant, but maintaining a reasonable spare parts inventory can keep production rolling when things go wrong. Depending on availability, risk and cost, you may even keep complete replacement assets on hand, such as complete valves or drop-in replacement motors. Reviewing your detailed maintenance records will help you decide which spares and backups to keep and how many you need.
Periodic PM Evaluation
It is easier to predict the future if you know the past. At least semi-annually, review a number of your recently documented PM activities to help gauge your program's overall effectiveness. Look at the number of breakdowns and why they occurred. Is the PM program extending the time between breakdowns? Are repair work orders being generated as a result of PM activities or elsewhere? Did you have the spares and materials you needed to get the equipment back on line? The information you get from your well-documented preventive maintenance records should tell you if your PM efforts are truly preventing failures and improving productivity.
Consider developing a PM effectiveness audit plan. This comprehensive review of your preventive maintenance activities can provide the data you need to drive procedural improvements, asset acquisition decisions, scheduling changes, inventory adjustments, or personnel assignments. Don't let your PM program be stagnant. Help it grow with your business.
ABOUT CSI
Central States Industrial Equipment (CSI) is a leader in distribution of hygienic pipe, valves, fittings, pumps, heat exchangers, and MRO supplies for hygienic industrial processors, with four distribution facilities across the U.S. CSI also provides detail design and execution for hygienic process systems in the food, dairy, beverage, pharmaceutical, biotechnology, and personal care industries. Specializing in process piping, system start-ups, and cleaning systems, CSI leverages technology, intellectual property, and industry expertise to deliver solutions to processing problems. More information can be found at www.csidesigns.com.