Why Monitor Your Process?
An overview of process instrumentation
This article will provide a basic overview of the role that process instrumentation and measurement play in sanitary processing plants. We will focus on process monitoring and management in the food & beverage processing and the biopharmaceutical manufacturing industries.
It’s a false economy not to monitor your processes. Some argue that monitoring requires more equipment — that is, instruments — which require a higher initial investment, can break, and require ongoing maintenance.
In reality, process instrumentation are critical components of the manufacturing operations in sanitary plants.
This article will explain:
- Why process monitoring is necessary
- What types of things to monitor
- The various types of components and instruments found in modern process control systems used in sanitary processing plants
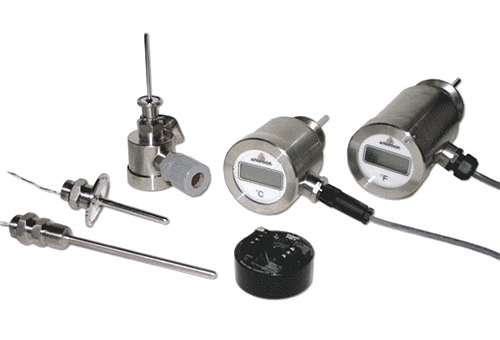
What should I be monitoring in my processing plant, and why?
Monitoring the processes in your sanitary plant is critical to achieving the following objectives:
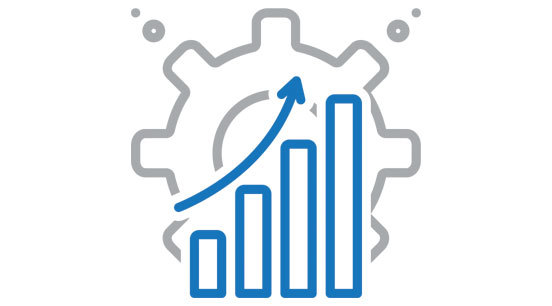
Efficiency
By monitoring process parameters around various product conditions — for example, the flow rates through pipes — plant operators can optimize their production for maximum operating efficiency. More information about process conditions may also be available in one central location, the plant’s central control room, requiring less walking around the plant floor to status components and systems.
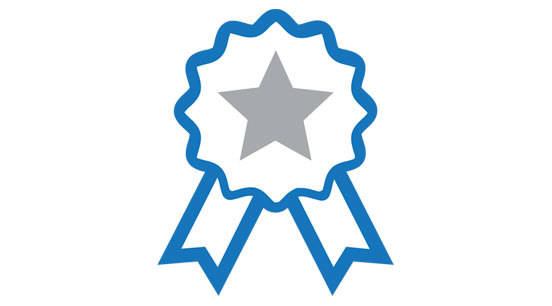
Quality
Monitoring certain operating variables, such as temperature, may also be critical to achieving and maintaining the desired product quality. For example, in food & beverage processing, too high or too low a processing temperature may result in an over-or-under-cooked final product or an unsafe or non-compliant product.
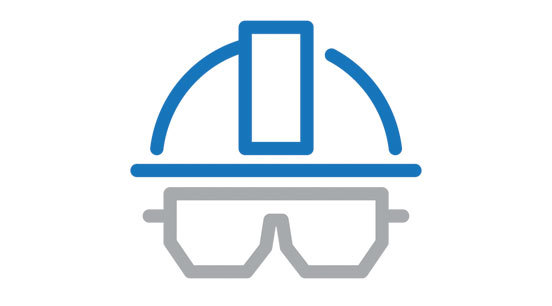
Safety
Other variables, such as pipeline and vessel operating pressures, must also be monitored continuously while in operation to maintain safety and avoid industrial accidents.
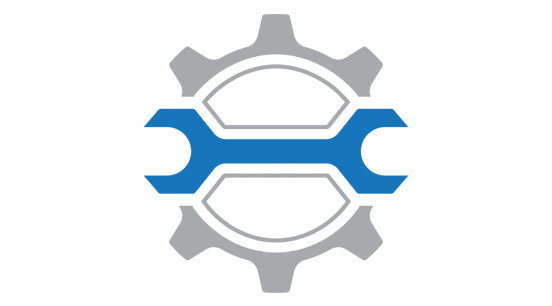
Preventative maintenance
Monitoring some variables — such as the operating hours on a pump — may be used to instruct plant operators on when preventive maintenance is required on a processing system or component to ensure continued error-free operation.
So, what types of things are typically measured or monitored in a sanitary processing plant?
Here's the complete list:
1. Pressure in process pipes or vessels. Process pressures outside of an expected range indicate changes in product, pump, or agitator performance, or other equipment problems.
2. Temperature. Temperatures that are too high or too low may affect product quality. Trending temperatures and cooling times may also indicate a loss of efficiency on heat transfer surfaces, an indicator of product fouling, bake-on, or system leaks.
3. Fluid level. Fluid level is an indicator of process conditions or when a component such as a tank needs attention. Fluid level under process conditions should also roughly correlate to specific gravity and other product recipe quantities.
4. Fluid flow rate or velocity are also indicators of process conditions or productivity in a process line. Fluid flow is a process parameter that can be used to monitor overall processing rate. Additionally, a flow rate balance is often needed when filling a pasteurizer or other continuous processing equipment, and that rate must be maintained accurately to keep the process running.
5. Product analytics, including pH, conductivity, weight, and chemical composition. Any or all could be monitored to maintain the desired product quality or verify CIP cleaning.
Components used in sanitary processing plant control systems
There are several essential components found in all process control systems used in the hygienic processing industries.
They include the following:
Sensors
Sensors are used at the point of operation (e.g., a process pipe, tank, or another system component such as a pump) to collect information relative to an operation. For example, sensors pick up changes in material conditions such as temperature, pressure, flow rate, etc.
Instruments
Instruments are measuring devices used to gauge the level, position, speed, weight, etc. of process fluids, using data collected from the sensors. At their most basic level, instruments are classified by category and operate either analog or digital. Each type is described below.
Analog instruments are simple mechanical devices that translate the measurement of a material (such as a liquid or gas) onto some sort of calibrated measurement indicator (such as an indicator needle on a dial).
For example, the common thermometer is a type of analog measuring instrument. The heat warms mercury in the storage bulb in the base of the thermometer, and it rises up a calibrated transparent tube in the device to measure how hot (or cold) the substance being measured is. The measurement process is purely a physical one.
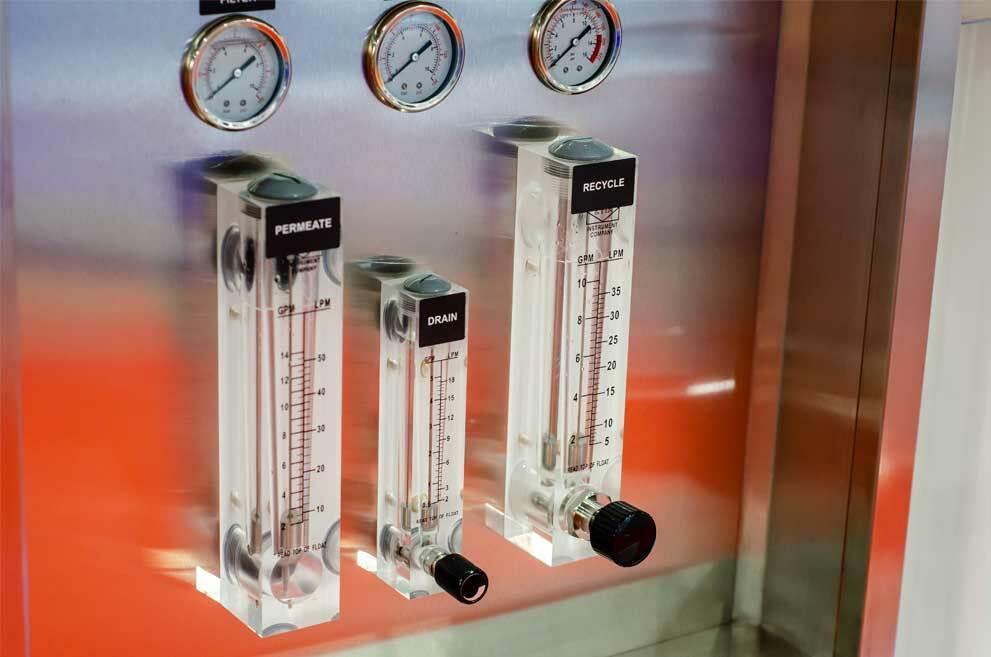
Digital instruments are more complicated. All digital instruments rely on the conversion of the measured results into an electrical signal, which is then converted into a format that may be viewed visually on a monitor or similar device. Digital instruments rely on a number of different physical principles in their operation. Commonly-used digital flow meters, for example, may be based on electromagnetic induction, the Coriolis effect, or ultrasonic wave propagation in their operation, with some varieties better suited for measuring specific types of fluids (such as corrosive fluids) than others.
Digital instruments convert the characteristics of the material measured (such as its heat, if a thermometer, or the flow rate of a liquid, if a flow meter) into an equivalent electrical form.
A component in the digital instrument called a transducer is responsible for making this conversion. The electrical information provided by the transducer then flows through:
- A signal processing unit - which amplifies the output from the transducer
- A multiplexer and signal converter - which mix the analog signals provided by the processing unit
- An analog-to-digital converter - which converts the analog data into its equivalent digital form
- A display - which shows the actual quantity being measured in its digital form
Digital instruments are also designed to convert for factors, such as temperature, in the material being measured. See the figure below for a conceptual view of how these types of instruments work.

Analog instruments are simple, relatively inexpensive devices, and they typically perform well under adverse operating conditions (temperature, humidity, etc.). They are, however, intrinsically less accurate in their measurement than digital instruments.
Digital instruments, in contrast, are more complex and expensive and more susceptible to adverse operating conditions than analog instruments (although protective cases designed for these instruments can mitigate environmental issues). They are, however, more accurate in their measurement than analog instruments.
Of critical importance, computers or other devices may store the results of their measurement electronically for further analysis or action or the maintenance of operating records.
Analog instruments are typically located at the point of data collection, either on or adjacent to the sensor. Digital instruments may be located next to the sensor or remotely connected to it via a communications cable.
Control Systems
Control system components are at the heart of measuring operations. They collect information received from the sensors and various instruments and process it for further distribution and/or action.
In modern processing plants, control systems receive data via a communications network connected to the myriad of instruments measuring process temperature, pressure, fluid flow rates, etc.
Typical communications networks used in these industrial process control systems are based on standard protocols, including HART, Profibus DP, Ethernet/IP, and DeviceNet. By far the most common among these communication protocols are based on simple 4-10 mA analog signals.
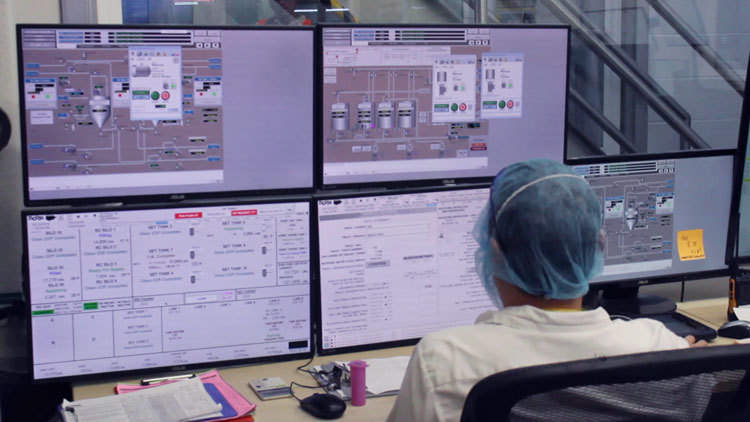
Control systems inform the plant operator about the process conditions to make adjustments to optimize production or correct problems. In the larger and more sophisticated processing plants, these control systems may be centrally located in the plant’s operations control room or outside the control room and connected to it via Ethernet/Internet.
In some cases, computers may automatically instruct other components of the system to adjust when a process anomaly is detected, such as opening or closing a valve. These “brains” behind control systems are not only capable of collecting measurement data from instruments, but acting upon that information as well.
Next Steps
Process control systems are an integral component of any modern sanitary processing plant. Without one in place, plant operators can’t readily measure or monitor the critical operating variables which can affect product quality, plant productivity, or even the safety of operations.
Furthermore, process control systems must uniquely address the product processing variables in a specific processing plant’s operations. In other words, there’s no “out of the box” generic process control system suitable for all plants.
CSI can help. We’re in the business of designing and engineering process systems used in the food & beverage and biopharmaceutical manufacturing industries. We also sell process measuring instruments from various OEMs designed to meet your needs without breaking your budget!
To learn more, contact us today by calling 417-831-1411.
ABOUT CSI
Central States Industrial Equipment (CSI) is a leader in distribution of hygienic pipe, valves, fittings, pumps, heat exchangers, and MRO supplies for hygienic industrial processors, with four distribution facilities across the U.S. CSI also provides detail design and execution for hygienic process systems in the food, dairy, beverage, pharmaceutical, biotechnology, and personal care industries. Specializing in process piping, system start-ups, and cleaning systems, CSI leverages technology, intellectual property, and industry expertise to deliver solutions to processing problems. More information can be found at www.csidesigns.com.