Hygienic Pump Repair
Keeping Your Process Pumps Up and Running
Hygienic pumps are one of the most critical system components used in the hygienic processing industries and are often some of the most used equipment across all sanitary industries. Whether it is food & beverage or biopharmaceutical manufacturing, hygienic pumps typically receive more wear and tear than most equipment.
Invariably, these pumps will fail due to extended use or other factors, and keeping them up and running is critical to maintaining plant productivity.
This article will look at the primary issues affecting the care and maintenance of hygienic pumps and the options available when they do fail.
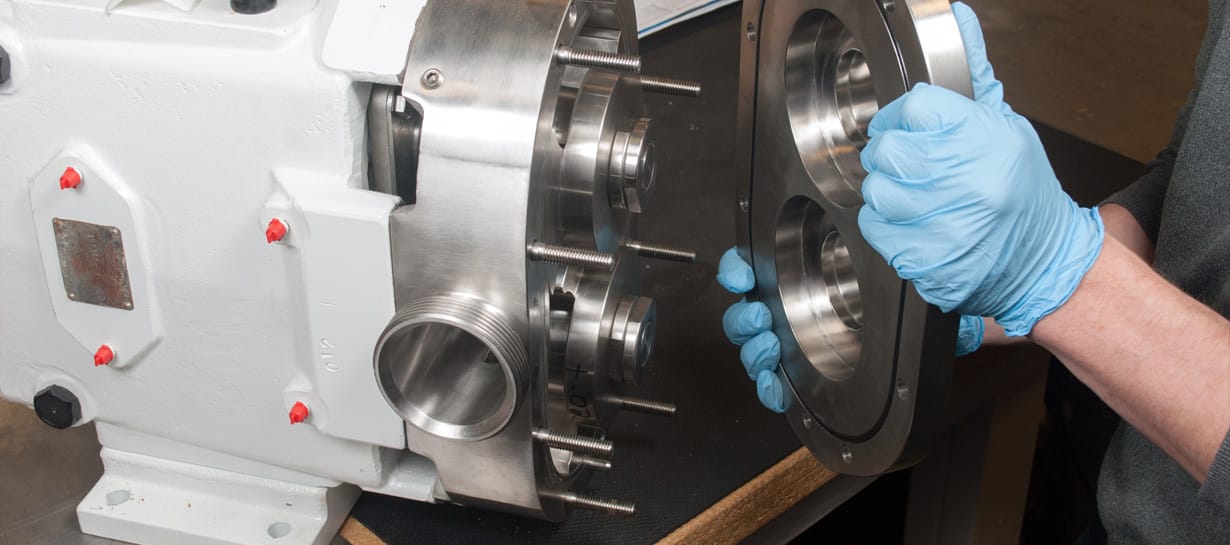
We'll discuss
- What is pump repair
- The root causes of pump failure and which components are most likely to break (and why)
- Proper pump selection, installation, and ongoing maintenance
- Two main options to consider when a pump does fail
- An overview of the hygienic pump repair and service options available from CSI
The Root Causes of Pump Failure
Pump failure can always be traced back to three types of problems: Mechanical, electrical, or hydraulic.
Mechanical problems
These problems in hygienic pumps are the primary reasons for pump failure, and they can be myriad.
They include the following:
Water in the Gearbox
Bearing or gear failure is most likely to occur due to the presence of water in the gearbox. This issue is the number one failure mode of most positive displacement pumps in the US. Learn how to recognize and avoid this issue by watching this video.
Running the Pump Dry
Pump seals require lubrication from fluid flows to dissipate the heat caused by friction. Running a pump dry results in the cracking and warping of these seals.
Overly Gritty or Abrasive Products
Unless an appropriate pump seal and pump seal flush are chosen — made from acceptable materials for the job — gritty or abrasive process fluids can quickly wear down pump seals.
Chemical or Physical Incompatibilities
Some chemicals in process fluids can quickly ruin pump seals unless the seal’s material is compatible with the fluids being pumped.
Pump Galling
Caused by a combination of friction and adhesion. Galling typically results from physical contact between a rotating surface and a stationary one. Galling leads to the slipping and tearing of the crystalline structures beneath the surface of the seal.
Excessive Shock and Vibration
Improperly aligned pumps may vibrate excessively, damaging the pump's rotating shaft and leading to seal failure.
Additional Installation Errors
Errors, including misaligning seals during installation and over-tightening fasteners, may also be causes of failure. Follow all manufacturer’s installation and torque specifications.
Harsh Environment
Uncontrolled heat, drastic shifts in operating temperatures, and caustic cleaning detergents may cause excessive seal wear. Varying the pressure around the seal can also lead to premature seal failure. The very nature of the materials being pumped will significantly affect the working life of pump seals.
Electrical problems
These may be associated with either the power supply or the pump's internals. To check for electrical problems, do the following:
Check the power supply voltage going into the pump.
The correct voltage and amperage rating for the pump are located on the nameplate of the motor. Overheating may result from excessively low power supply levels. Too high a supply voltage can lead to a lack of continuity in the motor's wiring or rotor windings.
Visually Inspect the Motor
Indications of motor overheating include burn marks or discoloration on the motor housing or components. Manually rotate the motor shaft to assess its condition. The shaft should rotate smoothly, with no catches or loose parts.
Check the Earth Continuity of the Motor
When measured with a multimeter, the earth continuity of a good motor should result in a reading of less than 0.5 ohm when it’s grounded to a good earth source, preferably near the motor’s base. Readings greater than this indicate that the motor’s insulation is failing, and could cause a shock.
Check the Continuity of the Motor’s Rotor Windings
Do so by connecting the multimeter to the motor’s Line (incoming current) and Load (outgoing current) terminals. Inconsistent voltage readings (or a zero voltage reading) may indicate that the motor is burned out.
Test the Motor’s Insulation Resistance
Use an insulation tester or megger. The minimum value of insulation resistance should be 1 megaohm. If the value is less than 0.2 megaohms, replace the motor.
Test the Motor's Running Amps
Do so with a multimeter. The ampere reading should be at or slightly below the manufacturer’s specified draw for the motor. If the reading is well below specification, or out of range, this may indicate problems with the motor.
Hydraulic issues
These issues in a hygienic pump may result from a pump that’s worn or broken, or incorrectly sized for the job. Occasionally there may be air or gas present in the process lines around the pump, resulting in a fluid lock.
In these cases, a fix can be as simple as venting the system using a vent check or air eliminator valve. For assistance with properly venting a system, call one of our pump experts today at 417-831-1411. We’d be happy to help.
Preventing Hygienic Pump Failure
There are multiple steps which may be followed to prevent pump failure
- Size the pump properly for the task at hand. In particular, know the flow rate and the viscosity of the materials being pumped. Partner with a pump professional to select the right pump for the job.
- Know what type of pump will work most effectively with the job at hand. There are various types of pumps, including centrifugal pumps, lobe pumps, screw pumps, and so on, and some pumping mechanisms work better with certain kinds of fluids than others.
- Avoid installation errors. Ensure that the pump is firmly mounted and dampened to avoid excessive vibration and that all rotating parts, including couplings, are correctly aligned.
- Use the pump in the manner for which it was designed. Proper day-to-day operations are one of the most significant determinants of the life of seals in particular. Therefore, operate the pump according to the manufacturer's specifications and guidelines, and do not run the pump without fluids in the rotor housing.
- Follow a regular preventative maintenance schedule for pumps. Conduct daily or weekly visual inspections of the pump and its components. In doing so, look for the following:
- Properly lubricated gearboxes
- Leaking from the seal area
- Seal flush liquid flow (should flow freely through the flush housing)
- Evidence of overheated bearings (e.g., discoloration)
- Excessive pump noise or vibration when the pump motor is running
Catching and correcting these problems when they first occur can result in less costly repairs downstream.
Pump Repair or Remanufacture?
When pump problems do need to be addressed, there are two options that may be considered:
- Repair the pump
- Remanufacture the pump, if possible. This is a less expensive option than purchasing a new pump, although not all pumps are eligible for remanufacturing.
Repairing a pump may be less expensive than remanufacturing it, although it depends on the underlying health of the pump.
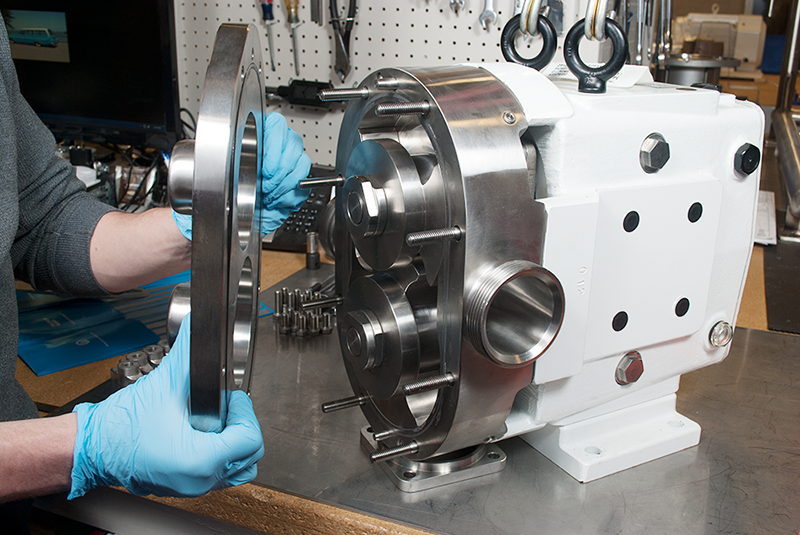
Pump repair is also relatively quick, minimizing operating downtime. And pump repairs can be conducted multiple times on a given pump, which may extend the useful service life of an old pump
Remanufacturing a pump is more extensive, expensive, and time-consuming. Remanufacture is limited to two or three occurrences for each pump depending on the specific pump and amount of wear present. Also, not all types of pumps can even be remanufactured. When it is an option, remanufacturing a pump typically includes the following steps:
- Every part within the pump's gearbox is replaced with new parts, and the gearbox is returned to new condition, including a fresh powder coat if applicable.
- All tolerances are returned to new factory specifications.
- New oversized rotors that fit the remanufactured body are installed.
With remanufactured pumps, the housing and casing are machined for oversized rotors, and all non-stainless-steel gearboxes are powder coated. Hydraulic performance tests are conducted on remanufactured pumps, and all carry a one-year warranty. Up to four standard rebuilds are available for the U1/ZP1/TRA10 pumps, and up to three standard rebuilds can be performed on U2/ZP2/TRA20 pumps.
Additionally, while maintenance personnel can conduct some pump repair operations in the field, when a pump is remanufactured it must be disconnected from the process line and shipped to the original manufacturer or a certified remanufacture facility.
CSI Pump Repair Services
CSI offers a repair/remanufacturing program at the company’s Springfield, MO; Fresno, CA; and Grand Prairie, TX facilities. Pumps are shipped to these locations, evaluated, and customers are presented with options, including repair, remanufacturing (if feasible), or replacement with a new pump.
The program is available for all brands of liquid hygienic pumps. In the case of repaired or remanufactured pumps, a “free from manufacturers defects” warranty is provided for all new parts.
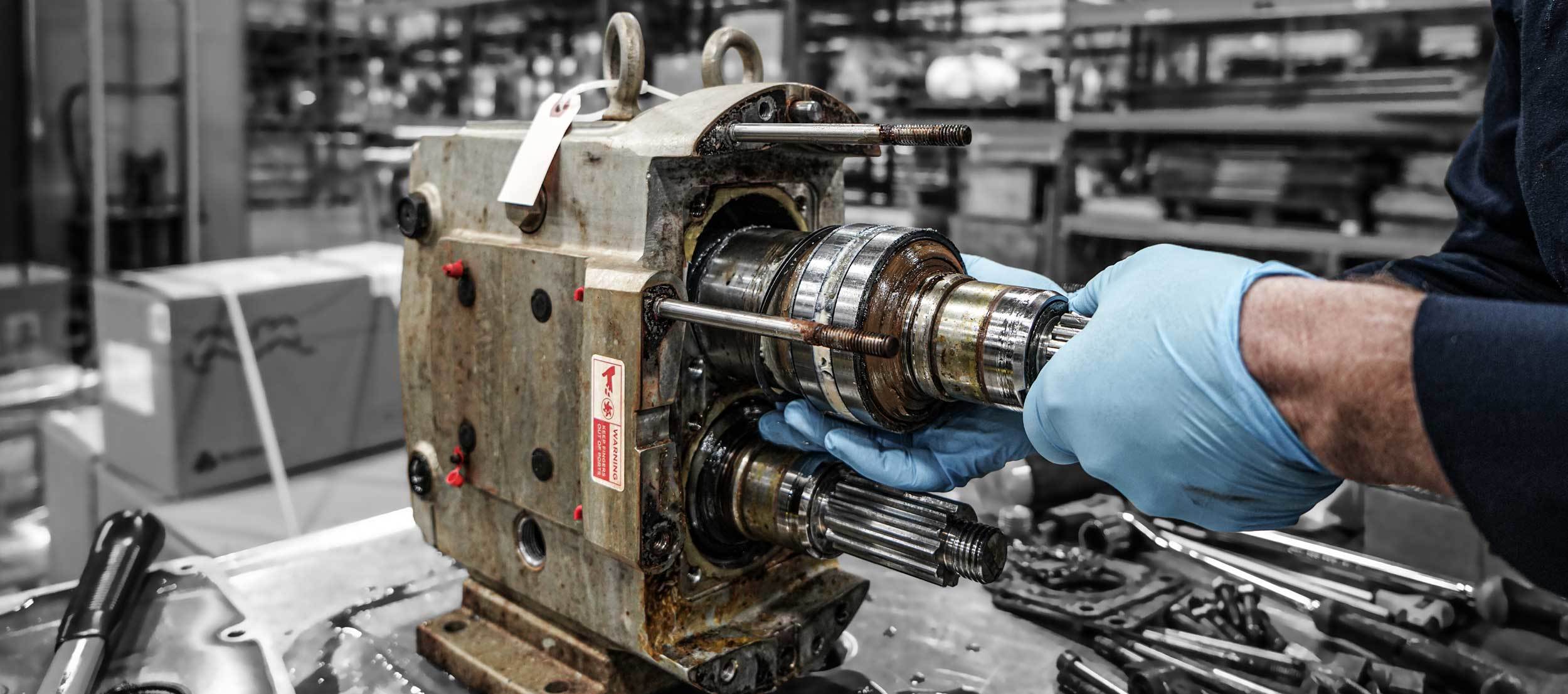
CSI’s pump remanufacturing program is an option for Ampco ZP Series, SPX Universal Series, Wright Flow TRA Series, and Alfa Laval SCPP Series pumps.
Remanufacturing these pumps returns an average cost savings of 20-30% over the purchase of a new one.
NEXT STEPS
Your hygienic pump is the heart of your processing system, and keeping it pumping properly is critical to maintaining efficient operations. Know what the causes are behind pump failure and how to avoid problems in the first place.
Should your pump need help, CSI can provide you with some options. Give us a call at (417) 831-1411.
A Guide to Choosing the Right Pump for Hygienic Applications
This guide is intended for engineers, production managers, or anyone concerned with proper pump selection for pharmaceutical, biotechnology, and other ultra-clean applications.
ABOUT CSI
Central States Industrial Equipment (CSI) is a leader in distribution of hygienic pipe, valves, fittings, pumps, heat exchangers, and MRO supplies for hygienic industrial processors, with four distribution facilities across the U.S. CSI also provides detail design and execution for hygienic process systems in the food, dairy, beverage, pharmaceutical, biotechnology, and personal care industries. Specializing in process piping, system start-ups, and cleaning systems, CSI leverages technology, intellectual property, and industry expertise to deliver solutions to processing problems. More information can be found at www.csidesigns.com.