Understanding Pump Seal Failure: Common Causes and Solutions
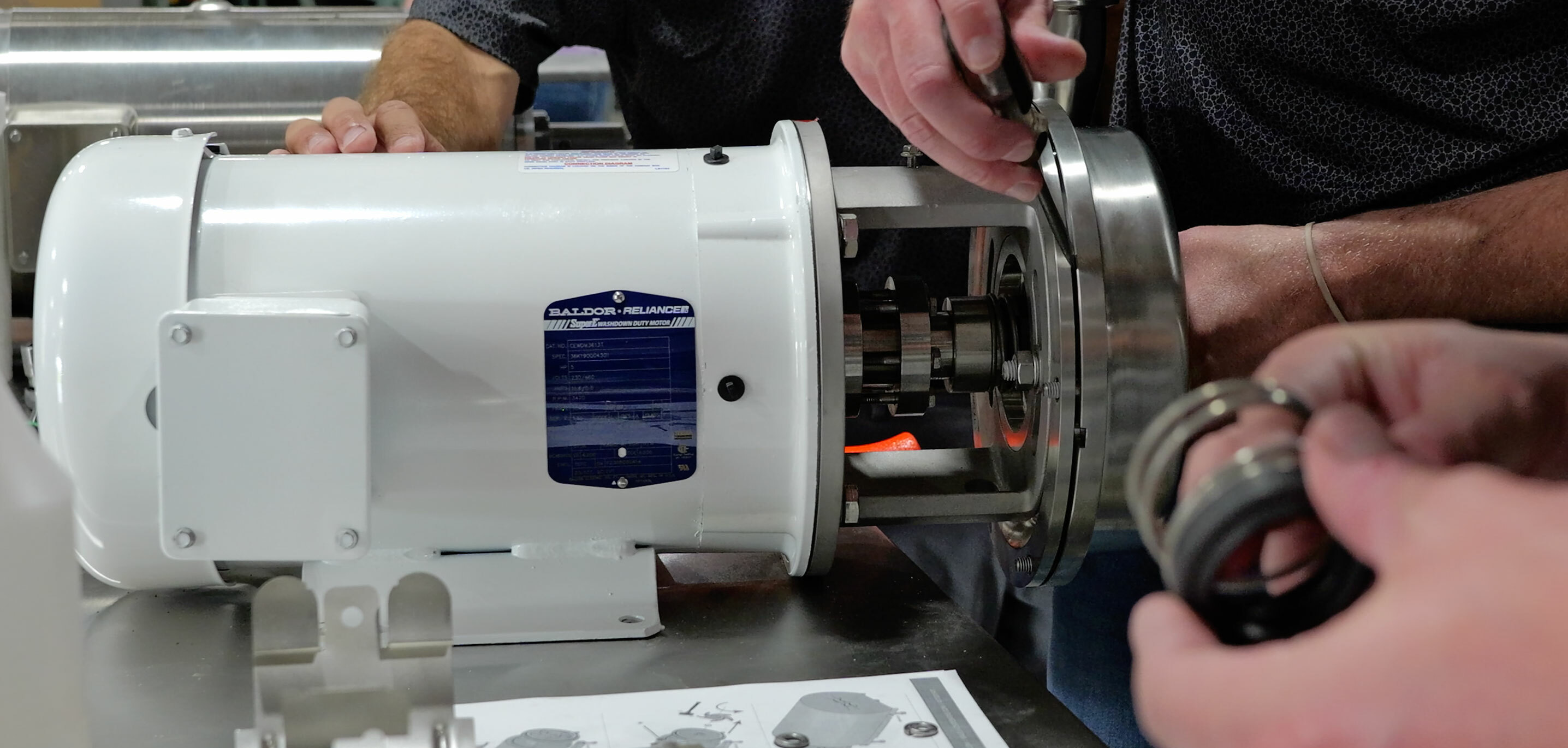
Pump seal failure is a critical issue in the sanitary industry, affecting pump performance and the efficiency and reliability of operations. Proper seal selection, installation, and maintenance can help prevent seal leakage and failure. Understanding the common causes is essential to minimizing costly pump downtime and maintaining sanitary conditions within the pump system and production line.
Preventing mechanical seal failures ensures operational efficiency and reliability. This article will explore the typical reasons behind pump seal failures, from installation errors to physical wear, and provide solutions to mitigate these issues. By understanding and addressing these common causes, you can implement preventive measures that enhance the performance and longevity of your pump systems.
What Causes Pump Seal Failure
Various factors contribute to pump shaft seal failure, categorized into mechanical issues, material incompatibilities, and operational errors. Several problems can lead to mechanical seal failure, including dry running, improper installation, and chemical degradation. By understanding these factors, you can implement adequate preventive measures to reduce seal component failures and prevent mechanical seal leakage.
Understanding Mechanical Seal Failure
Dry running occurs when a pump operates without the necessary fluids to lubricate the seal faces, causing friction between the mechanical seals. This friction is exacerbated when coarse materials like salt or sugar fall out of liquid suspension during processing, further damaging the seals.
To mitigate the risk of dry running, proper lubrication is essential. In cases where dry running is unavoidable, such as during tank emptying, a flush seal system can introduce an alternative fluid to maintain lubrication, reduce heat, and minimize seal wear. Automated systems that detect low fluid levels and shut down the pump before dry running occurs can further protect the seals from damage.
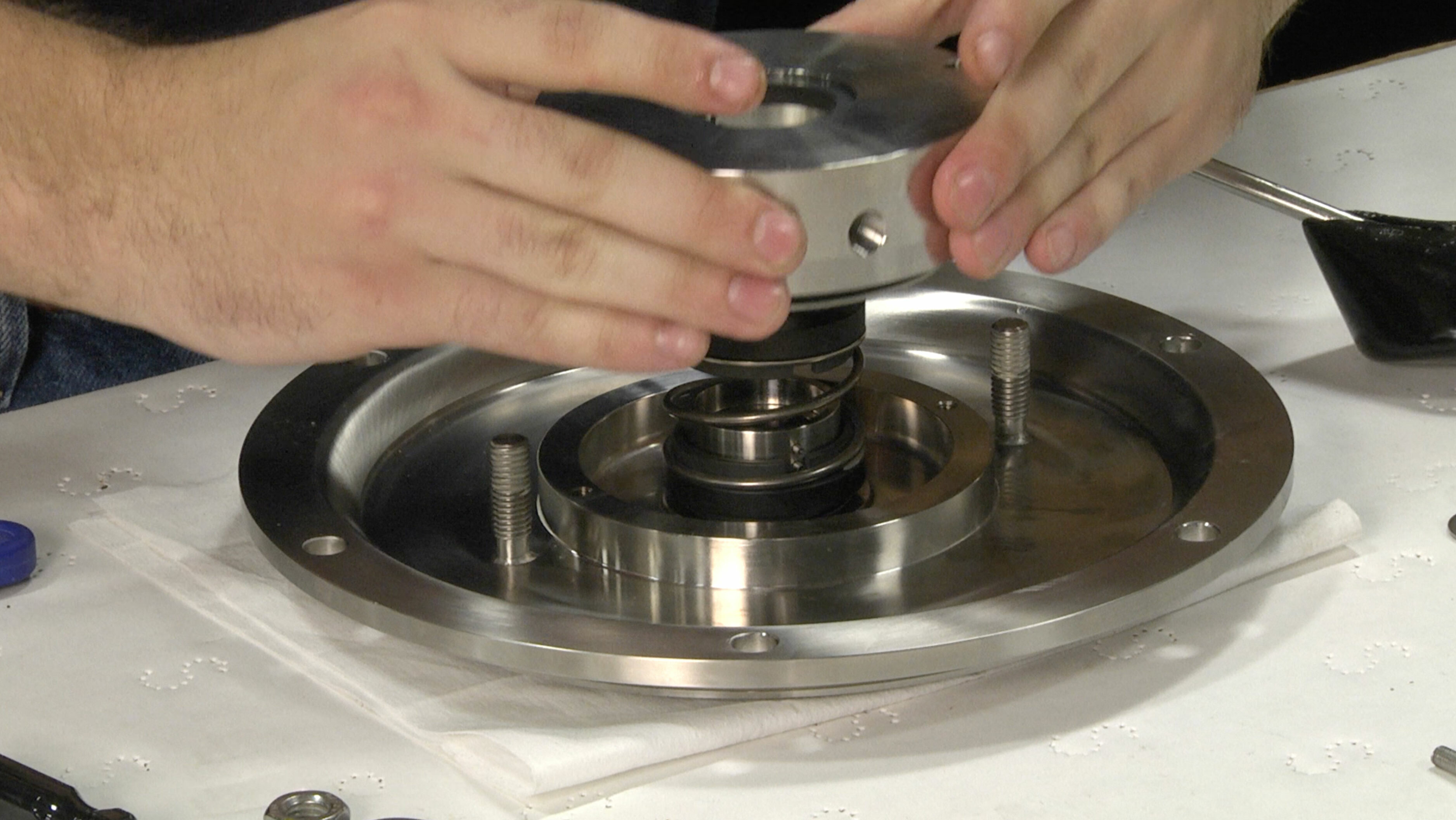
Improper Installation, Alignment, and Handling Errors
Improper installation and alignment are significant contributors to pump seal failure. One such case of improper seal installation is when the driver on the drive ring and the notch on the rotating seal are not properly aligned which can cause cracks in the rotating seal, typically made of carbon or silicon carbide. Cracks or breaks in the rotating seal will immediately present as a seal failure, allowing fluid to leak and leaving the pump needing service.
Improper handling of seals can certainly cause failure. In many cases, operators or maintenance technicians inadvertently touch the seal face and do not clean it afterward. When unintentional contact is made with the seal face, oils, dirt, and grease can be transferred from the technician's hand to the seal face. This added debris on an otherwise very flat surface will lead to premature failure.
Proper installation, handling, and alignment training is essential. Installers must know how to correctly align components and recognize signs of misalignment to prevent errors that could result in leaks, additional damage, and costly downtime.
Chemical Degradation
Exposure to harsh chemicals can significantly impact the longevity of pump seals. During the pump application process, CSI will closely review your processing specifications and ensure that the process fluid and pump seal components are compatible. Without proper compatibility, the seal won't reach its expected lifespan. You should consult a mechanical seal professional when unsure how your process fluid will react to elastomers or seal materials.
Physical Wear
The pump seal's lifespan depends on many factors that impact its physical wear. Under ideal conditions—such as running with water, no dry running, and perfectly aligned mechanical components—a pump seal could last for years. However, continuous operation under harsh conditions including poor installation, can add physical stress to the mechanical pump’s internal components, leading to premature wear and reduced seal life. Routine maintenance is essential to identify and replace worn seals. Due to installation variances, it is challenging to determine seal longevity. Expert guidance and careful selection of seal materials based on processing requirements are crucial for maximizing seal life.
Cavitation
Cavitation is the formation and collapse of air bubbles at supersonic speeds in the process fluid within a pump. This is harmful because the bubbles violently collapse, causing material removal and physical damage. Cavitation typically results in a noisy, "gravel-like" sound during pump operation and is common in centrifugal pumps, though it can occur in other pump types.
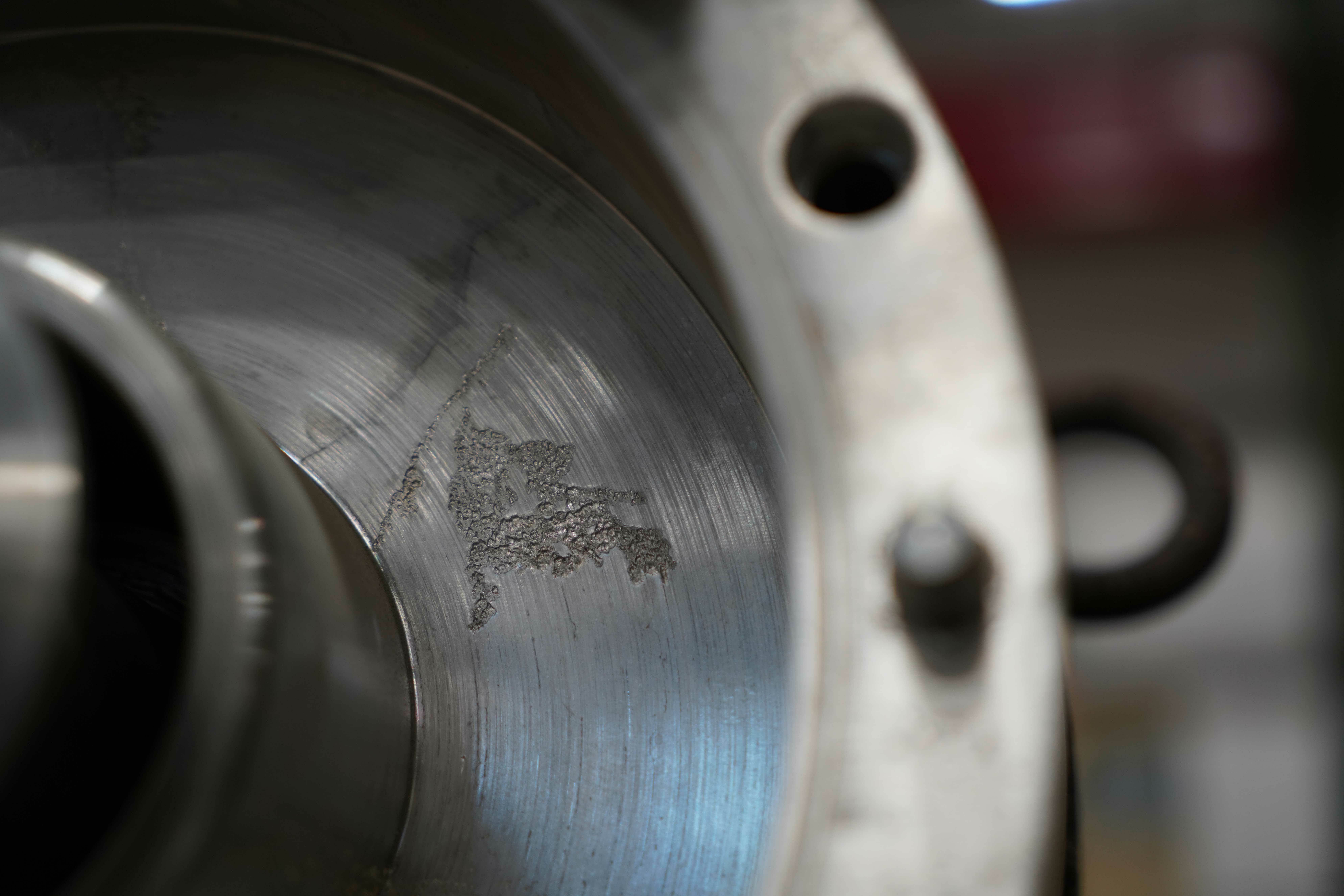
Monitoring and Controlling Cavitation
Monitoring and controlling fluid processes and operating conditions is essential to prevent cavitation. Understanding the Net Positive Suction Head (NPSH) is critical in managing cavitation. There are two types of NPSH:
- NPSH Available (NPSHa): The suction head available as determined by the customer’s process system.
- NPSH Required (NPSHr): The minimum suction head required by the pump to avoid cavitation, as published by the pump manufacturer.
Cavitation occurs when NPSHa is less than NPSHr. Ensuring that NPSHa meets or exceeds NPSHr is vital to prevent cavitation. While cavitation can cause significant physical damage and material erosion, it does not always directly affect the seal. However, maintaining proper NPSH levels is critical for protecting the pump's overall integrity and efficiency.
Excessive Pressure or Temperature
Operating a pump outside its recommended pressure or temperature ranges can lead to severe issues with seal integrity. When selecting seals, consider the potential for pressure spikes and temperature extremes. Ensure the seals are rated for the maximum expected operating conditions, including any additional factors like steam cleaning or extreme temperatures, to avoid premature failure and maintain reliable operations.
Effects of Operating Outside Recommended Ranges
Pressure: Excessive pressure, usually in the form of pressure spikes, can force the seal faces to separate momentarily before slamming back together. This can result in cracks and chips across the seal face, leading to failure.
Temperature: Pump seals comprise several components, including elastomers rated for specific temperature ranges. If the operating temperature exceeds the seal's rating, it can cause degradation or deformation. This is particularly important for clean-in-place (CIP), steam-in-place (SIP), or other extreme temperature applications.
Pump Selection Guide
This guide offers essential insights into choosing the proper pump for your processing systems. Learn about different pump types, their applications, and maintenance tips to ensure optimal performance and reliability in any environment.
Preventing Seal Failure with Best Practices
Implementing best practices throughout the process is essential to extending the life of your pump seals and preventing failure.
- Understand the Process: Gain a comprehensive understanding of your specific pumping process. This knowledge will help you select the appropriate seals and maintenance procedures.
- Partner with Experts: Work closely with a pump company, like CSI, that understands your process and can offer tailored advice and solutions from pump sizing to pump seal material compatibility. Their expertise will be invaluable in optimizing seal performance and longevity.
- Manage Dry Running: Implement measures to minimize the risk of dry running, in which the seals operate without adequate lubrication. When evacuating a tank, consider using a flush seal system to reduce dry run time and maintain seal lubrication.
Following these best practices can significantly reduce the risk of failure and ensure more reliable and efficient operation.
Size the Pump properly to Prevent Seal Failure
Proper pump sizing is essential in preventing seal failure. An incorrectly sized pump can lead to several issues that compromise the integrity of the pump seal. Here are critical considerations for pump sizing to avoid seal failure:
- Differential Pressure: Ensure the pump can handle the differential pressure (the difference between the inlet and outlet pressures) to prevent excessive wear on the seals and potential seal failure. High differential pressure can cause mechanical stress and heat, damaging the seal.
- Fluid Temperature: Consider fluid temperature as it affects seal material selection. Only use pumps and seals rated for your application’s operating temperature range. High temperatures can degrade certain seal materials, leading to leaks and failures.
- Fluid Viscosity: Match the pump to the fluid's viscosity. Higher viscosity fluids increase the load on the pump and seals, leading to wear and potential failure. Use pumps designed for high-viscosity fluids to maintain seal integrity.
- Flow Rate: Properly size the pump to meet the required flow rate. Over-sizing or under-sizing can cause the pump to operate inefficiently, leading to pressure fluctuations and seal stress, which can result in leaks or premature seal failure.
- Fluid Density: Account for fluid density when selecting and sizing the pump. Higher-density fluids require more power to pump, which can increase the mechanical load on the seals. Ensure the pump can handle the fluid density to avoid overloading and damaging the seals.
Proper pump sizing enhances efficiency and performance and significantly reduces the risk of seal failure. By carefully considering these factors in seal design, you can ensure reliable pump operation, minimize downtime, and extend the life of your pump seals.
Proper Pump Selection and Usage
Selecting the right pump type is essential for both system efficiency and pump seal longevity. Each pump type—centrifugal, circumferential piston, rotary lobe, or twin screw—has specific applications and benefits that affect seal performance:
- Centrifugal Pumps: Ideal for low-viscosity and high-flow applications.
- Circumferential Piston and Rotary Lobe Pumps: These are best for handling high-viscosity fluids and sensitive materials due to their gentle action.
- Twin Screw Pumps: Versatile for both low and high-viscosity fluids, suitable for processes needing flexibility.
Choosing the right pump ensures optimal performance, reduces downtime, and extends pump seal life. Consulting with experts and aligning pump selection with your process needs will help maintain the integrity of your pump seals and achieve trouble-free operation.
Follow Pump Installation Guidelines
Adhering to installation guidelines ensures pump seals' proper setup and performance and helps prevent issues such as misalignment, improper fitting, and damage during installation. Closely following pump installation standards helps avoid mechanical seal failures and severe system malfunctions. Proper training and thorough knowledge of installation procedures are essential for maintaining seal integrity and ensuring reliable pump operation.
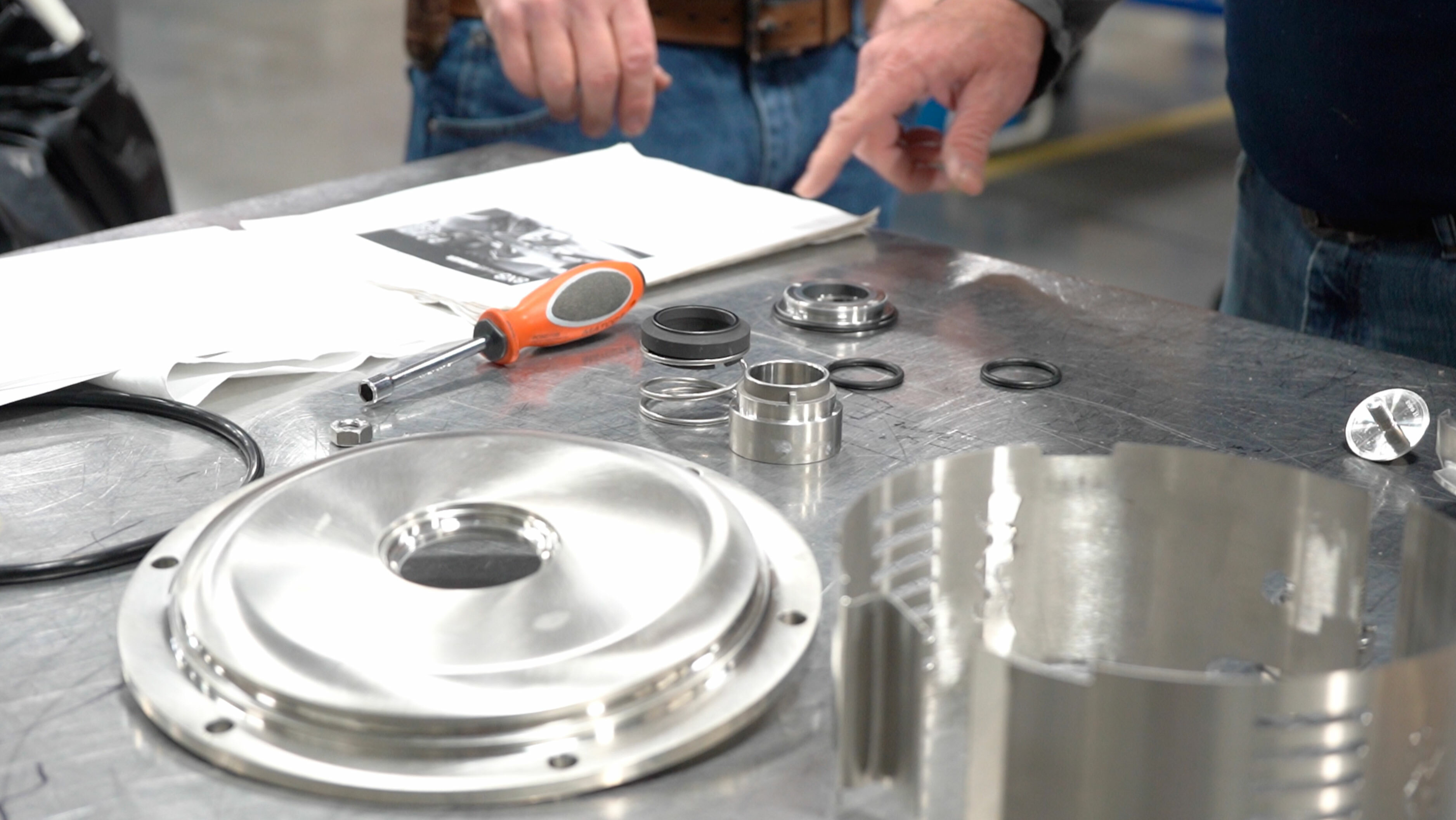
Preventative Maintenance
Scheduled maintenance is vital for extending the life of pump seals and preventing unexpected failures. Regular maintenance tasks should include:
- Inspection and Analysis: Conduct routine inspections to identify potential issues, such as misalignment or wear and tear, and analyze performance data to detect early signs of problems.
- Greasing and Oil Changes: Reduce friction and wear by lubricating moving parts regularly and replacing worn oil.
For industries such as food processing, pharmaceuticals, and dairy, where maintaining sanitary conditions is critical, preventive maintenance helps minimize downtime and avoid costly disruptions. Implementing a proactive maintenance schedule ensures the smooth operation of equipment and upholds the integrity of the production process.
Conclusion
To prolong the lifespan of pump seals and ensure optimal performance, understanding and addressing the common causes of seal failure is necessary. Key factors include:
- Dry Running: Ensure proper lubrication and minimize dry run time.
- Installation and Alignment: Follow precise guidelines and ensure proper alignment to avoid seal damage.
- Chemical compatibility: Use seals that are compatible with your process.
- Pressure and Temperature: Monitor operating conditions within recommended ranges to prevent stress and degradation.
Implementing best practices and preventive measures can enhance reliability and efficiency in industrial operations. Proper installation, regular maintenance, and selection of suitable seals are essential steps to reduce the risk of seal failure and ensure the equipment's smooth and safe operation.
Effectively understanding and addressing the common causes of seal failure is vital for maintaining reliability and efficiency in industrial operations, especially within the sanitary industry. By adhering to best practices and preventive measures, such as proper installation, regular maintenance, and suitable seal selection, you can significantly reduce the risk of seal failures and ensure continuous, trouble-free operation of your equipment.
Mechanical Seal Failures: FAQs
- What is the most common cause of pump seal failure?
-
The most common cause is dry running, where the pump operates without adequate lubrication. Dry running generates excessive heat and accelerates seal degradation. Other significant causes include improper installation and alignment issues.
- How long should a pump seal last?
-
The lifespan of a pump seal varies based on operating conditions and maintenance. Properly installed and maintained seals can last from several months to several years. Factors like operating temperature, pressure, and chemical exposure are critical in determining potential seal longevity.
- Can pump seal failure cause a fire?
-
Yes, it can lead to leaks of flammable fluids, which can ignite if exposed to an ignition source, potentially causing fires. Proper seal maintenance and monitoring are crucial to prevent such hazardous situations.
- Do all pump seals leak?
-
Not all pump seals leak, but they may develop leaks over time due to wear, improper installation, or operating conditions. Regular inspections and maintenance can help detect and address potential leaks before they become significant issues.
- What steps ensure that pump seals do not fail?
-
Ensure proper installation, regular maintenance, and alignment to prevent seal failure. Use seals compatible with the operating conditions and process fluids, monitor pressure and temperature, and adhere to recommended operating guidelines to maintain seal integrity.
Contributing Author
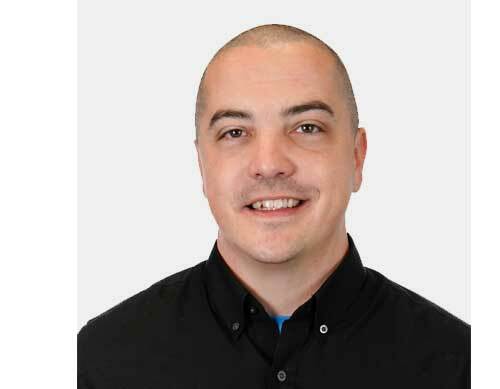
Michael David is the Manager of Pump and Heat Exchange Solutions at CSI. Michael received his B.S. degree in Mechanical Engineering from the Missouri University of Science and Technology, and brings over 17 years of experience in engineering, process design, fluid dynamics, and maintaining equipment for the food, dairy, beverage, biopharm and biotech markets. Michael supports a team of application specialists who focus on Pump and Heat Exchange solutions. He also leads many training initiatives for internal and external customers aimed at developing competence and confidence in the worlds of pumps and heat exchange technology.
Next Steps
Addressing pump seal failure is crucial to maintaining the efficiency and reliability of your sanitary processing operations. To prevent seal issues, consider the following steps:
- Assemble a Knowledgeable Team: Involve operators and managers from various departments to ensure a comprehensive approach to pump seal maintenance and failure prevention.
- Conduct a Thorough Analysis: Review your current pump systems and seals to identify potential vulnerabilities. Understanding your processes and the specific conditions that could lead to seal failure is essential.
- Partner with Experts: Collaborate with a trusted provider specializing in pump systems and seals. Their expertise can help you select the right components, ensure proper installation, and establish a maintenance plan that minimizes the risk of seal failure.
- Invest in Quality Equipment: Choose high-quality pump seals and systems tailored to your specific application needs. CSI offers a range of durable and reliable seals designed for various sanitary processing environments.
CSI has the expertise to help you design, engineer, and maintain pump systems that meet your exact hygienic processing needs. Our in-house team and state-of-the-art fabrication shop ensure that your equipment meets the highest industry standards, providing peace of mind and dependable performance.
To speak with a pump seal expert, request a quote below or call 800.654.5635. Let CSI help you keep your operations running smoothly and efficiently.
ABOUT CSI
Central States Industrial Equipment (CSI) is a leader in distribution of hygienic pipe, valves, fittings, pumps, heat exchangers, and MRO supplies for hygienic industrial processors, with four distribution facilities across the U.S. CSI also provides detail design and execution for hygienic process systems in the food, dairy, beverage, pharmaceutical, biotechnology, and personal care industries. Specializing in process piping, system start-ups, and cleaning systems, CSI leverages technology, intellectual property, and industry expertise to deliver solutions to processing problems. More information can be found at www.csidesigns.com.