Smart Instrumentation for Your Digital Transformation
Instrumentation should always be part of your process design. With appropriate instruments, you can ensure that your system operates within normal ranges. Additionally, because product and employee safety are critical in manufacturing environments, instrumentation plays a vital role in several system functions:
- Monitoring throughput
- Improving predictive maintenance
- Monitoring and controlling "Process" and CIP
- System monitoring
- Getting a return on your investment
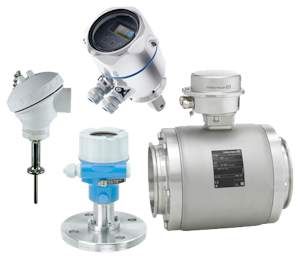
Monitoring throughput
Every manufacturing facility wants to be more efficient, which requires continuous monitoring of throughput so you can make targeted improvements.
Instrumentation enables facilities to track utility costs and raw material usage. With accurate, real-time data, managers and operators have an accurate picture of throughput and the factors that influence it.
Instrumentation identifies system bottlenecks that slow throughput, overfilling that wastes product, and over- or under-utilization of components that wastes system capacity.
Improving Predictive Maintenance
Manufacturers need the right instruments, and the data they provide, to create predictive models—and that makes systems smarter and more efficient.
For example, instead of performing preventive maintenance every six months to a year to replace seals on heat exchangers according to a schedule, algorithms based on pressure, flow, and temperature can predict when a gasket should be replaced. This can result in lower operating costs and increased machine uptime.
Moreover, utilizing smart instrumentation eliminates the need to hire a firm to replace gaskets prematurely or spend money on labor and materials every three months when equipment could last six months.
Optimizing Rinsing Times with Optical Sensors such as Turbidity
Incorporating optical sensors can be a game-changer regarding water and time savings. These sensors can detect phase changes in liquids, allowing you to optimize rinsing times rather than relying on static, non-optimized time schedule.
Benefits of Using Optical Sensors:
- Efficiency: Eliminate unnecessary rinsing, saving time and resources.
- Precision: Ensure the rinsing process is complete at the exact right moment.
- Cost Savings: Reduce water and energy consumption by optimizing the rinse cycle.
- Analytical: Identify and address potential issues early when rinsing takes longer than normal.
By using optical sensors to detect phase changes, you can achieve a more efficient and effective process. This innovative approach ensures you get the best performance while minimizing waste and costs.
Monitoring & Controlling CIP
Ensuring the safety and efficiency of food and pharmaceutical processing is paramount for all processing plants. In this context, Clean-in-Place (CIP) is instrumental in optimizing production. Specifically, tailored CIP systems for industries like food, dairy, beverage, and pharmaceutical processing offer a streamlined and reliable method for maintaining product quality and integrity without compromising safety.
At the heart of CIP systems lies sophisticated instrumentation tasked with the crucial role of monitoring, controlling, and optimizing the cleaning process. Instruments measure and regulate key CIP parameters—temperature, flow rate, pressure, and chemical concentration—guaranteeing that each cleaning cycle meets stringent repeatable hygiene requirements. Precise control prevents the underuse or overuse of resources such as cleaning agents and water, ensuring that cleaning is both effective and resource-efficient.
Clean-in-Place Instrumentation
CIP 2.0 from CSI leverages advanced instrumentation to monitor critical cleaning parameters, maintain stringent standards, and conserve valuable resources such as water, electricity, and cleaning agents, with the added benefit of potential water recovery.
“We are constantly pushing CIP 2.0 to be a smarter and more predictive machine. Ninety percent of our CIP projects include engineer-to-order specifications, so a customer can come in with a blank sheet of paper or an idea for a design and we will engineer to be as smart as their budget or schedule allows.”
—Trent Bullock, Director of Engineering Services
System Monitoring
Instrumentation technology is improving and now provides more self-diagnostics. That’s good news for end users implementing digital transformation projects. Newer instruments can conduct internal health checks and provide status updates to programmable log controllers (PLCs), indicating whether the equipment is operating within its specified range or if there is an issue with a machine or part that needs replacement.
Accurate readings are crucial. The latest instruments include an internal calibration check. They can be triggered to run the health monitoring feature and provide a detailed report. This is the type of cutting-edge technology CSI controls engineers have been working on when designing new systems to support digital transformation projects for their customers
Instruments are connected to a PLC that collects information and puts it on trend charts or sends a message to the control system to trigger further actions. In the past, the data remained isolated and was not transmitted to the operations team or other facilities. Today, that data can be accessed and utilized for process improvements.
These additional data points are critical in creating new predictive models and can be sent for storage or further examination in the cloud. The rise of digital transformation, also known as Industry 4.0, paves the way for data mining and creating actionable plans.
Getting a Return on Your Investment
CSI can help customers with ROI through various approaches. Often on the engineering side, CSI engineering services will assist clients in building a business case to realize ROI. This involves retrofitting designs or processes to boost throughput or reduce cleaning downtime, leading to tangible ROI.
Instrumentation can also contribute to ROI by lowering utility costs. When a flow meter or pressure transmitter is used on a pump, the pump speed can be adjusted based on process requirements and then monitored, which can eliminate the need to run a pump at full speed all day. With the right instrumentation, pumps can operate at lower capacity and still get the job done. Reducing wear and tear on pumps and motors results in electrical savings.
"ROI often comes from instrumentation's increased accuracy. For instance, using an older meter on a filler might slightly overfill bottles, giving away product for free. By upgrading to a more precise instrument like a mass meter, product overfill can be minimized, resulting in a relatively quick ROI, even with a modest investment,” said Trent Bullock, Director of Engineering Services.
End users should consider the overall cost of ownership of any systems they purchase or design. Investing a little more upfront in instrumentation or a more robust system design could lower ROI in the long run.
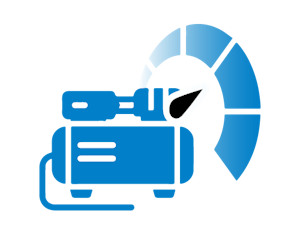
CSI customers commonly have one or more air compressors in operation. A variable frequency drive (VFD) on a 25-horsepower compressor costs about $3,500 and enables the compressor to adjust its speed based on operational needs. At annual savings of up to $6,000, the VFD would pay for itself in less than a year and deliver both energy and cost savings.
Automated CIP delivers smarter predictivity
Ensuring the safety and efficiency of food and pharmaceutical processing is paramount for all processing plants. In this context, Clean-in-Place (CIP) is instrumental in enhancing production optimization. Specifically, tailored CIP systems for industries like food, dairy, beverage, and pharmaceutical processing offer a streamlined and reliable method for maintaining product quality and integrity without compromising safety.
At the heart of CIP systems lies sophisticated instrumentation, tasked with the crucial role of monitoring, controlling, and optimizing the cleaning process. Instruments meticulously measure and regulate key CIP parameters—temperature, flow rate, pressure, and chemical concentration—guaranteeing that each cleaning cycle meets stringent repeatable hygiene requirements. This precise control is instrumental in preventing the underuse or overuse of resources, such as cleaning agents and water, ensuring that the cleaning is both effective and resource-efficient.
Instrumentation is key to operational efficiency, with features that can pay for themselves in months instead of years.
CSI’s expertise in instrumentation, plus offerings like CIP 2.0 technology, provides smarter predictivity for your digital transformation.
Contributing Author
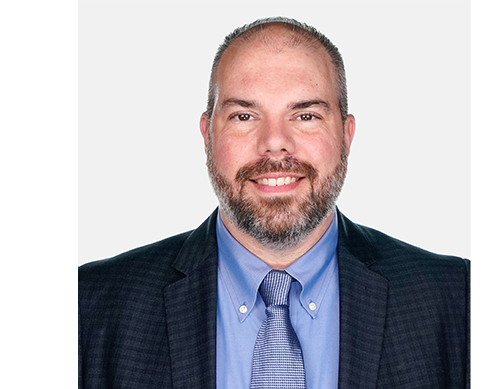
Trent Bullock is the Director of Engineering Services at CSI. Trent graduated from University Missouri Rolla (UMR), currently known as Missouri University of Science and Technology, with a degree in Mechanical Engineering. He has vast industry experience in controls and automation, process engineering, manufacturing engineering, and OEM equipment development. His team is responsible for designing sanitary process and control systems for food, dairy, beverage, personal care, biotech, and pharmaceutical industries. He is focused on providing support and technical expertise to both internal and external customers.
ABOUT CSI
Central States Industrial Equipment (CSI) is a leader in distribution of hygienic pipe, valves, fittings, pumps, heat exchangers, and MRO supplies for hygienic industrial processors, with four distribution facilities across the U.S. CSI also provides detail design and execution for hygienic process systems in the food, dairy, beverage, pharmaceutical, biotechnology, and personal care industries. Specializing in process piping, system start-ups, and cleaning systems, CSI leverages technology, intellectual property, and industry expertise to deliver solutions to processing problems. More information can be found at www.csidesigns.com.