Optimize Clean In Place Pump: Sizing & Performance Tips
Understanding CIP Systems
Clean-in-Place (CIP) systems are designed to clean and sanitize process equipment, pipelines, and tanks without the need for disassembly. These systems are widely used in industries such as food, beverage, pharmaceutical, and cosmetic, where maintaining high levels of hygiene is crucial. A typical CIP system consists of a pump, valves, and a control system that work together to circulate cleaning solutions through the process equipment. The pump ensures that the cleaning solution flows at the required rate and pressure, while the valves and control system manage the direction and timing of the flow. This automated process not only ensures thorough cleaning but also minimizes the risk of contamination, making CIP systems an essential component in maintaining product quality and safety.
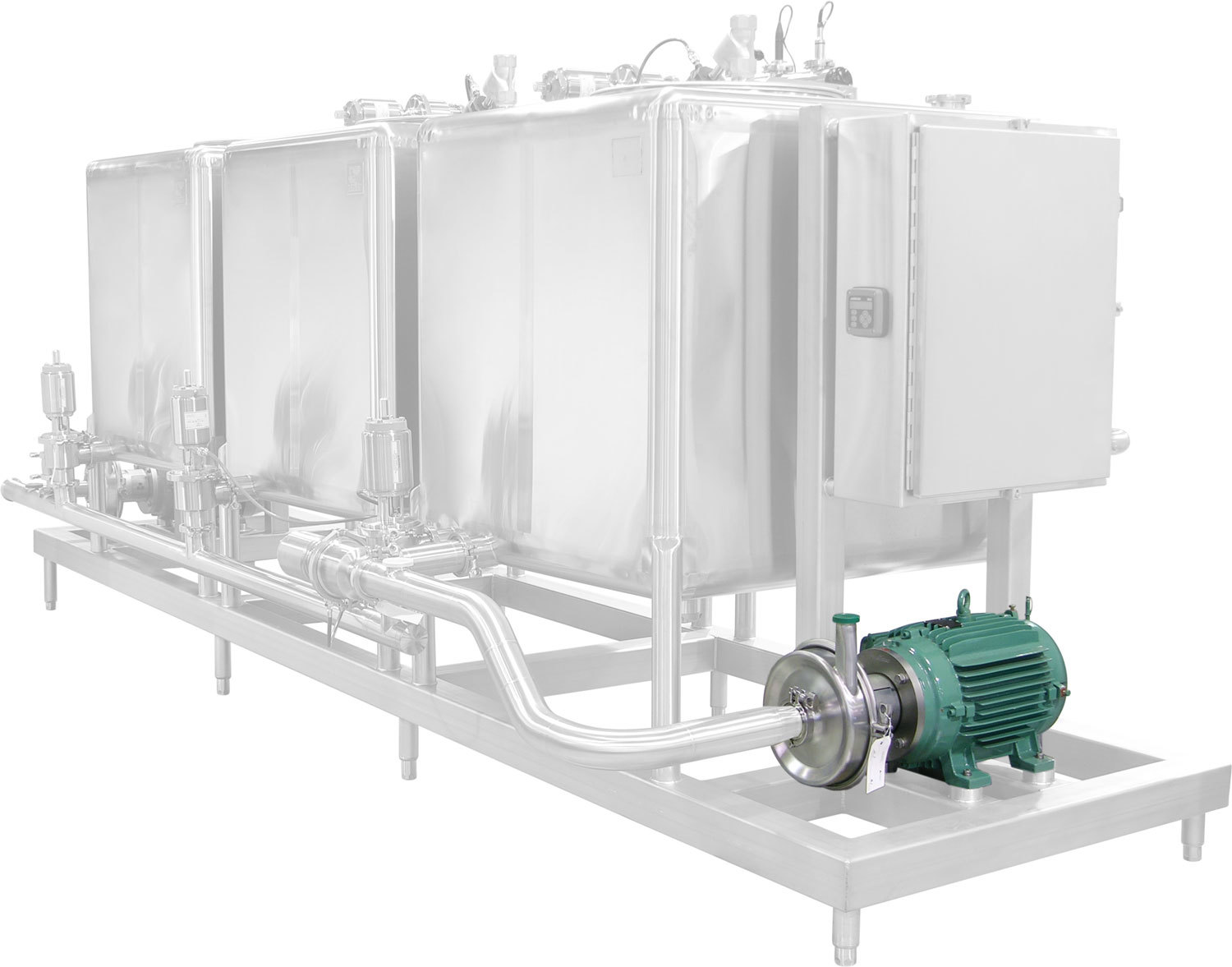
Benefits of Implementing a CIP System
Implementing a CIP system offers several significant benefits:
- Improved Hygiene and Reduced Risk of Contamination: By cleaning and sanitizing equipment without disassembly, CIP systems reduce the risk of contamination, ensuring that the highest hygiene standards are maintained.
- Increased Efficiency and Productivity: CIP systems automate the cleaning process, reducing the time and labor required for manual cleaning. This leads to increased efficiency and allows for more production time.
- Extended Equipment Lifespan: By maintaining equipment in optimal condition, CIP systems help extend the lifespan of process equipment, protecting your investment.
- Compliance with Regulatory Requirements: CIP systems help ensure that your processes meet industry regulations and standards, which is crucial for avoiding fines and maintaining your reputation.
Understanding Clean-in-place Supply Pumps
Cleaning in place uses a combination of
- Chemistry
- Temperature
- Cleaning time
- Mechanical force
This is to weaken bonds between soils and system surfaces.
The force created by the supply pump and fluid action removes unwanted substances throughout the system.
Because of their role in achieving cleaning requirements, supply pumps should be sized to provide sufficient flow and pressure for maintaining turbulence throughout the piping circuit.
Certain diaphragm pumps used in CIP systems can run dry without damage, making them versatile for various operational needs.
Cleaning action in a CIP system
The action, or turbulence, of the cleaning fluid through the process lines is determined by the velocity of the fluid, which is determined by the flow output of the CIP supply pump, making proper pump selection and sizing an essential part of any CIP system.
Calculating the precise flow rate needed to create turbulent flow in a particular system is complicated because it must take into account every detail of the system that influences the flow and pressure demands on the supply pump, especially the pipe or tube diameter.
Pump Flow Chart
Tubing O.D. | GPM (for 5fps) | GPM (for 7fps) | GPM (for 10fps) |
0.5” | 1.7 | 2.3 | 3.4 |
0.75” | 4.7 | 6.6 | 9.4 |
1” | 9.3 | 13 | 19 |
1.5” | 23 | 32 | 46 |
2” | 43 | 60 | 86 |
2.5” | 69 | 96 | 138 |
3” | 101 | 141 | 202 |
4” | 180 | 252 | 360 |
6” | 409 | 573 | 818 |
A fluid speed velocity of 5-7 feet per second (fps) is generally accepted to be the target range, with 5fps considered the absolute minimum. In many CIP applications, quality managers and CIP design engineers prefer to maintain velocities of 7fps, particularly in line sizes of 3” or larger to adequately overcome entrained air and dead leg areas.
The amount of flow required to achieve a particular fluid velocity varies with line size so it is essential to know the relationship between pipe or tube diameter and flow rate. At a given flow rate at the discharge port of the supply pump, the velocity of the fluid decreases as the line size increases; therefore, the larger the process lines, the more flow the supply pump must generate to achieve the necessary velocity.
The chart shows the relationship between flow rates (in gallons per minute—GPM) for various line sizes and the relative velocity of the fluid.
In addition to flow rate, the pressure is also an important consideration when sizing CIP supply pumps. The supply pump must be capable of providing enough pressure to overcome friction forces and back pressure elements in the line to ensure proper movement of fluid throughout the circuit without stopping.
CIP system pumps keep product, cleaning chemicals, and water moving through the system during each phase of cleaning.
- Push-Out (optional) - Prior to the pre-rinse cycle, push out residual product in the process lines using a projectile-type product recovery system. Doing so saves valuable product from going down the drain and reduces the amount of soil in the lines, which reduces the amount of time and resources needed to CIP. Product recovery systems can be integrated with CIP systems.
- Pre-rinse – Use potable plant water, water-for-injection (WFI), purified water (PW) or re-use the final rinse solution from the previous cleaning sequence. The pre-rinse wets the interior surface of the lines and tanks, removes most of the remaining residue, dissolves sugars and partially melts fats. It also provides a non-chemical pressure test of the CIP flow path. The pre-rinse is a very important step in the CIP process because a well-monitored and well-executed pre-rinse makes the rest of the wash cycle predictable and repeatable.
- Caustic Wash – (140 - 185° F) The main detergent wash. Removes organics like proteins and fats. For very heavy soil, the caustic wash may require a two-stage approach. The first wash is sent to the drain and the second can be recovered and re-used.
- Intermediate Rinse – Potable water, WFI or PW rinse. Purges dissolved soils and flushes out residual traces of detergent remaining from the caustic wash.
- Acid Wash – (130 - 150° F) Dissolves mineral scale from hard water deposits, protein residues, and neutralizes the system pH.
- Final Rinse – Rinse with WFI or PW to flush residual cleaning agents.
- Air Blow (optional) – Removes moisture remaining after the final rinse.
- Sanitizing Rinse (optional) – May be required to disinfect or sterilize the process lines by killing microorganisms before starting the next production run.
Introducing periodic changes in the flow velocity, known as pulsed flow, enhances the effectiveness of mechanical fluid action and shortens cleaning cycle times. Pulsing the flow between 4-7 fps during wash cycles creates temporary spikes in the mechanical cleaning forces and pushes cleaning solution into hard-to-clean areas like deadlegs, expansions, and standard tee branches. Pulsed flow cycles can easily be written into the cleaning cycle program.
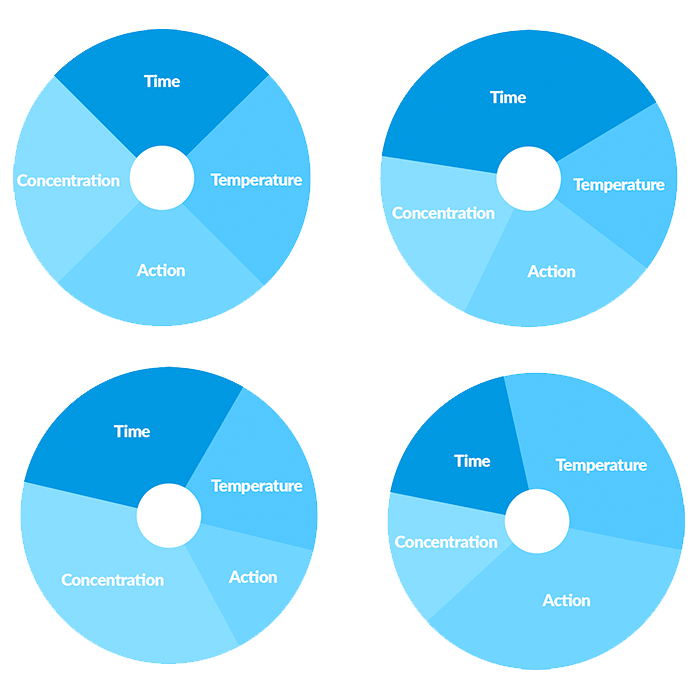
Action, or turbulence
The action in a cleaning process is the mechanical force of the cleaning solution that physically dislodges soil from the surface. Alone, it does a good job of removing unwanted debris. When combined with the other TACT elements, action becomes vastly more effective.
In 1959 a chemical engineer named Herbert Sinner introduced the four basic principles that are essential to the cleaning process: Time, Action, Chemicals and Temperature or TACT, for short. He represented these four factors in a graphic that came to be known as “Sinner's Circle.” The four principles Sinner identified must be applied in the right proportions to properly clean your process system.
If the supply flow rate is too low to create turbulence throughout the complete circuit, for example, no amount of time, temperature or chemicals will give you the cleaning results you need.
Centrifugal pumps
Their high flow rate capabilities, abrasive solution compatibility, mixing potential, as well as their relatively simple engineering, make centrifugal pumps well-suited to CIP applications.
If a pump is supplying multiple circuits that require different flows and pressures, control of the pump speed with a variable frequency drive (VFD) may be required. Supply pumps are typically 316 sanitary stainless steel centrifugal pumps with cleanable seals. The pump elastomers should be compatible with the product soil and Clean-in-Place chemicals such as ethylene propylene diene monomer (EPDM) or a perfluoroelastomer like Dupont's Kalrez®.
Twin screw pumps
Twin screw pumps conforming to 3-A Sanitary Standards can serve several applications. Their unique design allows the pump to perform both processing and CIP using the same unit. Some models can move soft solids delicately without damaging the product or compromising visual integrity.
Pressure for spray devices
Supply pumps must also maintain the pressure required by spray devices installed in CIP tanks or vessels.
Device | Pressure |
Static spray balls | 25 psi |
Rotating spray balls | 35 psi |
Rotary spray heads | Working pressure: 1 - 3 bar Recommended pressure: 2 bar |
Rotary jet heads | Working Pressure: 40 - 300 psi Recommended Pressure: 50 - 200 psi |
Clean-in-place Buying Guide
This Buying Guide for Clean-in-Place Solutions is a comprehensive resource for anyone who designs, owns, or operates processing systems and wants information about all aspects of CIP Systems.
Static Spray Balls
As the name suggests, static spray balls are fixed in place by clamp, thread, weld or pin and therefore do not rotate inside the tank. The spray direction for the numerous small jets of solution is determined by the drilled hole pattern on the ball. Designed for relatively low flows and pressures (commonly 40gpm @ 25psi), they have a moderate amount of impingement action when used on smaller tanks but rely primarily on cascading action to clean tank surfaces.
Rotating Spray Balls
Combining the reliability of a static spray ball with the benefit of rotation gives rotating spray balls the advantage of better cleaning solution coverage inside the tank. The flow of cleaning solution causes the spray ball to rotate easily on ball bearings. Their heavier design permits higher flow rates than most static spray balls, which allows rotating spray balls to deliver more impact to the soiled tank surface.
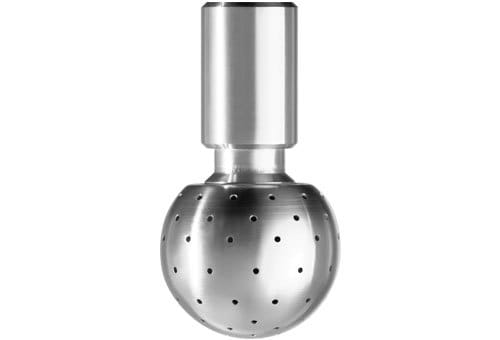
Rotary Spray Heads
Curved and straight slots in the body of the rotary spray head emit fanned jets of solution that swirl in a regular pattern throughout the entire vessel to create a vibrating impact effect and considerable cascading flow that can be effective for larger vessels with challenging product soil.
Rotary Jet Heads
When high impingement force is needed to properly clean a tank or vessel, a rotating jet spray device is the answer. Their multi-axis rotation can deliver extremely high impact streams of cleaning solution in precise 360° patterns to all areas of the tank. High-pressure capacities allow them to use
Pump maintenance and repair
Some pumps can be remanufactured up to three or four times over the pump's lifetime, at a fraction of the cost of replacing the pump. The remanufacturing process can turn a worn, inefficient pump into one that performs like new, saving the cost of replacing an underperforming pump.
Pump repair and remanufacture guide
For more information about CIP supply pump design, manufacturing, installation, and repair, contact CSI today.
Next Steps
It's essential to understand your processing system needs when deciding which type of supply pump to utilize. Not all pumps are created equally, and selecting between all of the available options can feel daunting.
That's where we come in.
CSI has a team of pump experts ready to answer your questions. Their years of industry knowledge working with dozens of pump manufactures will help determine the pump and motor sizes needed to achieve the correct system flow for your process.
We also offer a pump repair program designed to take the frustration and guesswork out of dealing with pump maintenance. Our OEM-trained technicians are prepared to perform routine maintenance on your pumps, including the replacement of wear parts and other components.
To speak with a pump expert, request a quote below or call 417-831-1411.
ABOUT CSI
Central States Industrial Equipment (CSI) is a leader in distribution of hygienic pipe, valves, fittings, pumps, heat exchangers, and MRO supplies for hygienic industrial processors, with four distribution facilities across the U.S. CSI also provides detail design and execution for hygienic process systems in the food, dairy, beverage, pharmaceutical, biotechnology, and personal care industries. Specializing in process piping, system start-ups, and cleaning systems, CSI leverages technology, intellectual property, and industry expertise to deliver solutions to processing problems. More information can be found at www.csidesigns.com.