What is Pressure Drop and How Does it Affect Your Processing System?
What is Pressure Drop?
Process piping systems (a network of specialized tubes and valves used in factories and plants to move liquids or gasses during production) are subject to a phenomenon known as pressure drop. Simply put, pressure drop is the difference in total pressure between two points in a fluid-carrying network. When a liquid material enters one end of a piping system, and leaves the other, pressure drop, or pressure loss in the pipes, will occur. Pressure drops occur in piping systems when fluids encounter obstruction in the pipes, friction, or even an elevation change, such as pushing fluids through a nozzle or valve. When combined, these issues contribute to pressure loss, affecting the efficiency and performance of the piping system. For a given system, calculating the pressure drop can be done with engineering models using the type of fluid, its flow rate, the piping layout and specifications (including pipe diameter), the system component specifications (such as pumps), and more. Calculating pressure drop is essential for maintaining system integrity and diagnosing potential issues.
Pressure drop in and of itself is not necessarily bad. Understanding how to calculate it in a specific pipeline allows engineers to properly design a system, and determine variables such as pipe length and diameter, pump specifications, and the types of valves to be used, among other things. However, there are also negative consequences associated with pressure drop if it is not well understood for a particular installation.
However, depending on the piping system installation, negative consequences can occur if the pressure drop is not well understood.
If there is an excessive pressure drop in a system, the working fluid temperatures increase, and system pumps will need to work harder due to increased energy consumption. Pressure drops can also increase overall system pressure, increasing wear on components and introducing potentially dangerous over-pressure conditions. Pressure drop calculation is crucial in various industries to ensure system efficiency and prevent equipment damage. Accurate pressure drop calculations help in designing and maintaining fluid transport systems effectively. Finally, excessive pressure drop can also render some piping system components inoperable due to inadequate operating pressures, or create damaging system cavitation (also known as vapor bubbles). These negatives and the overall impact of pressure drop are the focus of this article, including the pressure drop equation and pressure drop formula.
Why does pressure drop matter?
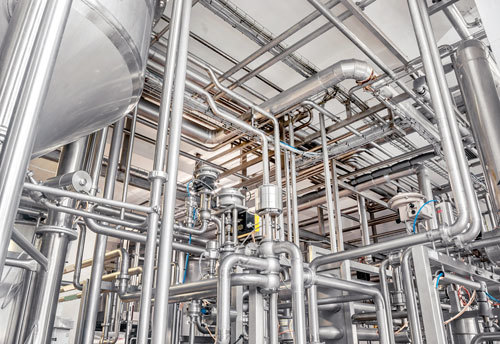
At its most basic level, understanding the pressure drop associated with a specific fluid-carrying network allows process plant engineers to determine the size of the pumps/motors needed and the process pipe diameter required to move a particular type of product through a piping system. The higher the pressure drop in the line, the greater the energy consumed to maintain the desired process flow, requiring a higher horsepower motor. Conversely, the lower the pressure drop in a piping system, the less energy consumed, providing the potential to use a lower horsepower motor. Pressure drop also determines the overall system pressure head requirements. Pressure drop increases proportionally to the frictional shear forces encountered, influenced by factors such as fluid velocity, viscosity, and pipe characteristics.
Pressure head (aka pump pressure head) is simply the height to which a specific pump can lift a column of water, typically expressed in meters. It measures the pump's force on the fluid being pumped. Pump pressure heads may be calculated or available from the pump’s manufacturer. Regardless of the method used for calculation, it’s essential to include the pump pressure head when adjusting for any pressure drop within a piping system.
If the needed pressure head is too high due to a large drop, adverse effects on system components may occur, including the proper operation of ancillary equipment, premature failure of seals, and potentially harmful overpressure situations.
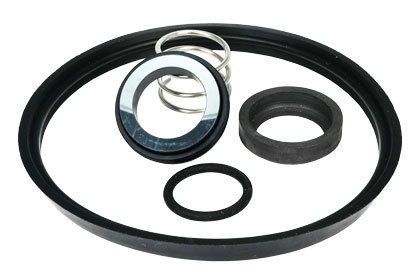
The effect of pressure drop on seals
Seals used in equipment such as pumps and heat exchangers have specific pressure limitations. When the equipment is operating within a suitable range (in terms of pressure, temperature, speed, etc.), seals will have a pre-defined life cycle.
When equipment is pushed to operate outside the optimal range, caused by factors such as over-pressurization, the seals will degrade or deform, causing leaks in the system.
Even after the overpressure incident has been corrected, the seals will continue to leak since they no longer fit properly.
The effect of pressure drop on safety
Over-pressure on pipes caused by pressure drops can also lead to safety concerns. Processing systems are designed to operate safely and efficiently. When system piping is undersized for a specific application, the pump has to be oversized to accommodate the pressure drop. In this situation, equipment close to the pump experiences higher-than-acceptable pressures.
This can lead to ruptures in the piping, exposing processing plant personnel to unsafe working conditions (e.g., hot liquid products, corrosive cleaning chemicals, etc.)
What Affects Pressure Drop in Fluid Flow?
1. The Product
When considering the potential for pressure drop in a specific fluid processing system, the first step is to understand the nature of the product being pumped through it.
Fluid properties including
- Density
- Heat capacity
- Temperature
- Viscosity
all affect pressure drop.
For example, in a food processing plant, certain products like ketchup can significantly alter their thickness as they're pumped through pipes due to shear forces. These types of products will become thinner due to friction caused by the passage through the pumps and the interior surfaces of the pipes.
This phenomenon is called thixotropy, which is a time-dependent shear thinning property. Thixotrophic fluids are normally viscous when in a static state (such as ketchup in a bottle), but become thinner or less viscous when shaken or agitated, returning to their normal state when the source of agitation is removed.
In contrast, other products, such as vinegar, act more like Newtonian fluids under processing conditions. Newtonian fluids are liquids which are not thixoprophic, and are not subject to changes in consistency when subjected to shear force. Products which exhibit Newtonian characteristics, therefore, can contribute to a higher pressure drop when being pumped through a pipeline because their consistency does not significantly change as it passes through the process piping system.
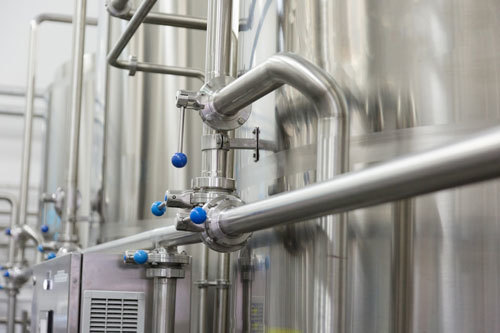
2. Mechanical Components and Pipe Diameter
Mechanical components in a piping system—including valves, flow meters, adapters, couplings, and tubing—can also impact pressure drop. Apart from pumps, all of these components commonly found in a process piping system contribute to a system's pressure drop because they remove energy from the process flow rather than adding to it.
The mechanical pressure drop also depends on
- The cross-sectional area of the pipe
- The pipe's interior surface roughness
- The length of the pipe
- How many bends there are in the system
- The geometrical complexity of each component
For example, changes in fluid flow or direction (like introducing bends like 45- or 90-degree elbows) can alter the flow, causing more friction and pressure drop. Longer distances traveled mean more chances for friction, reducing efficiency.
3. Changes in the Elevation of Piping
A change in elevation in the piping system can also significantly affect pressure drop. Suppose a pipe's starting elevation is lower than its end elevation. In that case, the rise in elevation will cause an additional pressure drop in the system (measured in terms of fluid head, which is equivalent to the rise in elevation).
In contrast, the pipe will experience an additional pressure gain if its starting elevation is higher than its end elevation (again, measured in terms of fluid head and equivalent to the fall in elevation in this case).
The overall pressure drop may be calculated using several equations for a specific process piping system.
Example:
P(end)= P(start) - friction loss- fittings loss -component loss + elevation (start-end) + pump head
Where
- P(end)= pressure at the end of the pipe
- P(start)= pressure at the start of the pipe
- Elevation (start-end) = (elevation at the start of the pipe) – (elevation at the end of the pipe)
- Pump head= 0 (if no pump is present)
So, when designing a process system to minimize or eliminate pressure drop, process plant engineers should do the following:
- Ensure that the process pipe's interior diameter and the size of the pump (horsepower, throughput) are properly sized for the type of fluid being piped through the system. Mistakes in either of these can result in excessive pressure drops or overpressure situations.
- Minimize the number of additional mechanical components (valves, flow meters, adaptors, and couplings) in a process pipeline, as these can increase pressure drop problems.
- Ensure that the process pipeline is laid out to be as compact as possible, minimizing pipe lengths and bends. Excessive pipe run lengths and changes in direction will contribute to pressure drop.
- Make sure that the process pipelines are as level as possible, ideally with both starting and end elevations close to the same height. As noted above, changes in piping elevation in the overall system will contribute to either pressure drop or overpressure situations.
Next Steps in Pressure Drop Calculations
Determining the pressure drop in a particular piping system is highly technical, requiring an understanding of fluid dynamics. Calculating elements such as friction loss in a pipe system requires the application of mathematical equations which goes beyond the scope intended in this article.
However, CSI can help. We're experts in designing and configuring process pipelines, and we will work with you to develop a solution to understand the pressure drops (or gains) in your pipeline system and properly engineer it to meet the needs of a particular process application. Contact CSI at (417) 831-1411 for more information.
ABOUT CSI
Central States Industrial Equipment (CSI) is a leader in distribution of hygienic pipe, valves, fittings, pumps, heat exchangers, and MRO supplies for hygienic industrial processors, with four distribution facilities across the U.S. CSI also provides detail design and execution for hygienic process systems in the food, dairy, beverage, pharmaceutical, biotechnology, and personal care industries. Specializing in process piping, system start-ups, and cleaning systems, CSI leverages technology, intellectual property, and industry expertise to deliver solutions to processing problems. More information can be found at www.csidesigns.com.