Plant Connectivity: The Next Industrial Revolution
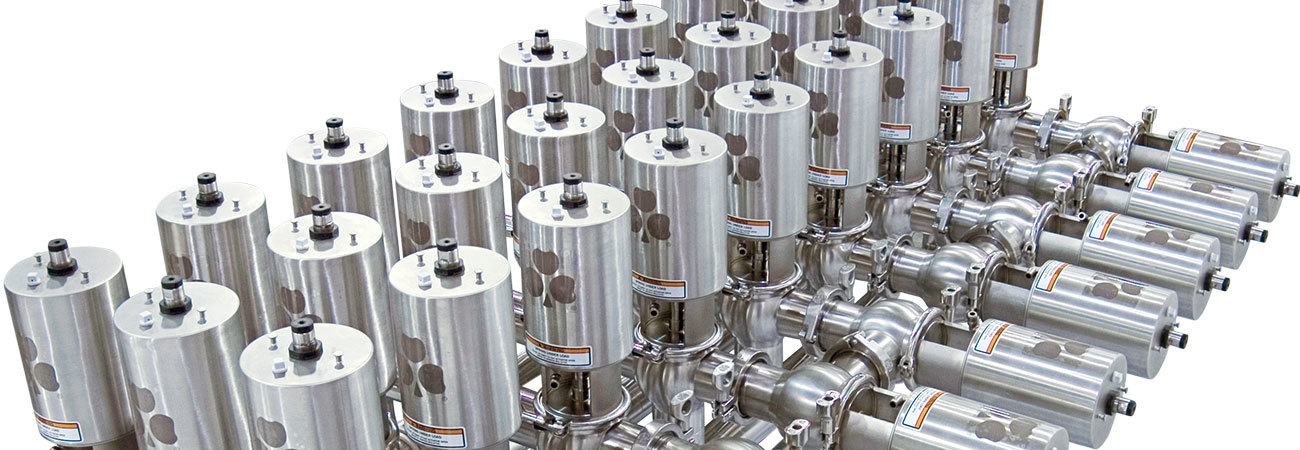
Production facilities across the globe are turning to technology to ensure that they are always functioning at top-level performance, using specialized equipment to digitally track processes and eliminate human error.
Plant connectivity is a phrase that describes the network that connects the industrial production environment to the corporate IT side. Plant connectivity lets an entire corporate network monitor vital production data, leading to informed decision-making throughout the enterprise. Making Ethernet/IP the standard communication protocol on a plant floor allows a company to create an interconnected web of understanding and data collection. With this in place, pieces of equipment are able to communicate with each other, giving the operators and corporate management information needed to make critical decisions.
Communication from skids to the plant are becoming more popular, as plants are getting hardware that allows companies to have more control over the plant and upgrades with new and better programming logic. In the past, a clean-in-place (CIP) system, with no plant communication, could be run as soon as an operator pushed the “Start” button. The wash ran, regardless if incorrect valves or lines were open or if the process line was still running production, significantly increasing the risk for product contamination, equipment damage, or injury to personnel. In contrast, a modern integrated solution asks permission to run from a plant programmable logic controller (PLC) and is only allowed to run when production is complete and appropriate routing valves have moved to their correct positions, thereby preventing an operator from carelessly running cleaning fluid down the wrong lines or into the sellable product.
Monitoring a production line suffering from disappointing output or production flow inconsistencies is a great example of plant connectivity. By upgrading the control system to analyze data while the line is running, an operator can determine the root cause as to why one line is running at a higher overall equipment effectiveness (OEE), while the other line is starved for product. The data monitoring can shed light on how a line might be hindered by processes not visible to the human eye.
Operators who manually monitor data do not have the capability to track resources such as water, electricity usage, and product waste. They are also unable to automatically adjust set points such as temperature, chemical concentrations, and conductivity. However, automated data tracking allows operators to accurately monitor resources and set points to get a comprehensive understanding of plant functions. This information is received almost instantaneously and can link multiple production facilities worldwide, allowing executives to compare plant productivity and make informed changes that maximize each plant’s output in real-time.
Plants are currently evolving to be smarter, allowing users to access data, utilize safeguards, and make informed decisions in real time. To stay ahead of the curve, many companies are investing in the future of technology. Taking small steps like automating equipment, enabling data tracking, and implementing an industrial communication system will enable a company to minimize mistakes, capitalize efficiency, and make the kind of informed decisions only accurate data tracking enables you to do. Plant connectivity is the natural progression for modern processing industries and, at this rate, will only become more important.
Expert Bio
Trent Bullock, Process Engineer
Trent Bullock is deeply knowledgeable about liquid process systems, manufacturing, controls, and automation. At CSI, he is responsible for designing sanitary process and control systems for food, dairy, and beverage industries. He is focused on providing support and technical expertise to both internal and external customers. His background is in Mechanical Engineering, and he graduated from UMR University Missouri Rolla, currently known as Missouri University of Science and Technology. Trent said he is not afraid to challenge conventions and is always looking for the best, most efficient way to achieve any goal.
Kyle Thompson, Process Engineer
Kyle Thompson graduated from Missouri University of Science and Technology with a Bachelor of Science in Mechanical Engineering. Before joining CSI in 2015, he worked in the manufacturing industry, where he focused on identifying and implementing process improvements and lean manufacturing strategies. As a Process Engineer at CSI, Kyle focuses on FDA compliant fluid processing systems. He has extensive expertise with automation, pasteurization, sanitization and clean-in-place, heat transfer, fluid dynamics, and sanitary process equipment.
ABOUT CSI
Central States Industrial Equipment (CSI) is a leader in distribution of hygienic pipe, valves, fittings, pumps, heat exchangers, and MRO supplies for hygienic industrial processors, with four distribution facilities across the U.S. CSI also provides detail design and execution for hygienic process systems in the food, dairy, beverage, pharmaceutical, biotechnology, and personal care industries. Specializing in process piping, system start-ups, and cleaning systems, CSI leverages technology, intellectual property, and industry expertise to deliver solutions to processing problems. More information can be found at www.csidesigns.com.