Winery Cuts Tote Cleaning Expense by 87% With Affordable Automation
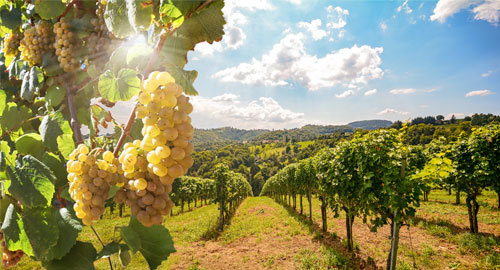
Winemaking is a difficult venture where maximizing efficiencies for increased output is paramount to success — not an industry for the faint of heart.
Whether it’s balancing profit margins, ensuring strong distribution channels, or fostering good customer and retail relationships, it’s clear to see why so many wine manufacturers struggle to survive. To overcome these challenges, wineries are increasingly forced to pursue new technologies to improve their processes.
According to the Silicon Valley State of the Wine Industry Report for 2020:
“As we move into a low-growth environment in 2020, the dominant competitive issue will shift to efficiencies. Now, you will not only need to continue to make great wine and incessantly evolve your sales channels, but you will also need to run your business as efficiently as possible so your margins are better than your peers’.”
Automating routine tasks is a smart move when pursuing efficiencies because automation improves productivity while reducing costs.
The Challenge
Located in the beautiful wine country of California is a vineyard that currently produces over 135,000 gallons of wine each season. The winery traces its family history back 100 years to Bari, Italy, and is renowned for its wines crafted from Alicante Bouschet, a deep, dark grape with spice, rich fruit, and a gentle earthiness. In addition to producing wine for local consumers, the winery produces high-quality bulk wine and grape juice concentrates for wineries across the U.S. to supplement their winemaking process and enhance their wines.
Producing wine at these volumes means the winery utilized large wine storage containers, which require frequent cleaning. For years this California winery was manually completing this cleaning process, taking an operator 45 minutes or more to clean each tote. Multiply this process over 500 totes each year, and they estimated their approximate labor costs at $5,625 each year. To help reduce their cleaning costs, the vineyard went in search of a durable, efficient, and cost-effective way to provide faster tote cleaning.
The Solution: Automated Tote Cleaning with Rotary Jet Cleaners
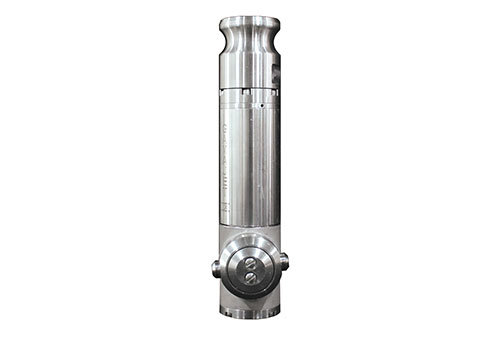
The winemaker contacted one of their distributors, Central States Industrial (CSI) to see if they had a solution to aid and expedite the tote cleaning process. CSI recommended the Gamajet 9 Rotary Jet Cleaner from Alfa Laval, specifically designed for cleaning small and mid-sized tanks and vessels.
By switching to a Gamajet 9 cleaner, the winery would be able to cut cleaning time down to an average of 6 minutes per tote, a savings of 87%.
With more time to spend on other important duties, the winery realized a productivity increase while slashing the cost of an activity that is essential to maintaining product integrity.
COST COMPARISON CHART
Manual Cost Per Tote | Automated Cost Per Tote | |
Time | 45 Minutes | 6 Minutes |
Labor Rate: $15.00 Per Hour | $11.25 | $1.50 |
Number of Cleanings Per Season | 500 | 500 |
Total Cost | $5,625 | $750 |
Total Savings | $4,875 |
Proof of Concept
The winemaker wanted to test the CSI solution, so CSI Business Development Leader John Riley did an on-site demo with the spray cleaner and a custom-crafted adaptor to mount the spray head inside the winery tote. The GJ 9 cleaned the tote in six minutes. Multiply that time savings by 500 totes a season, and the winery could save an average 375 staff-hours of cleaning time. With that time dedicated to other tasks, the winery would realize a significant increase in productivity and allow the winery to remain competitive in the market.
To learn more about how the Gamajet 9 can save you money, contact CSI today!
More About Rotary Jet Heads
Increase Efficiencies
Process designers recommend rotary jet heads when cleaning requires a combination of high water pressure and cleaning agents to produce impingement action. In Clean-in-place (CIP), impingement refers to the force of water under pressure and flow to adequately remove soils from interior surfaces of tanks. Cleaning occurs when the concentrated fluid stream meets interior surfaces.
The GJ 9 jet cleaner uses 5 pounds of cleaning force at 10 feet (5.5 kg at 3 m). With fewer parts, the GJ 9 spray head is an efficient cleaning tool that delivers reliable, repeatable 360 degree cleaning.
Designers also choose rotary jet heads to clean totes because they use less water, less energy, and smaller volumes of cleaning agent than spray balls. To achieve cleaning results, jet heads use an optimized high-impact jet pattern to create jet pressure, or force of impact, to remove residues.
Rotary jet heads also rotate in precise, repeatable patterns to achieve full coverage inside the tank.
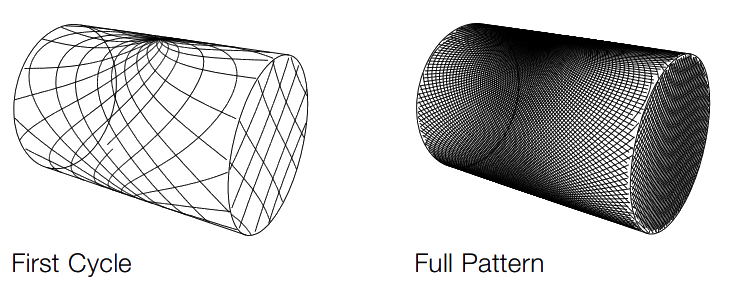
Its 360° spray pattern provides thorough scouring of the entire tote, reducing operating time and costs. The jet head readily passes through the small opening at the top of IBC totes and can handle high pressures and temperatures, enabling quick and easy cleaning.
Cleaning Process and Parameters
In addition to jet head factors, four cycle factors affect the cleaning action of rotary jet heads: time, action, cleaning chemicals, and temperature.
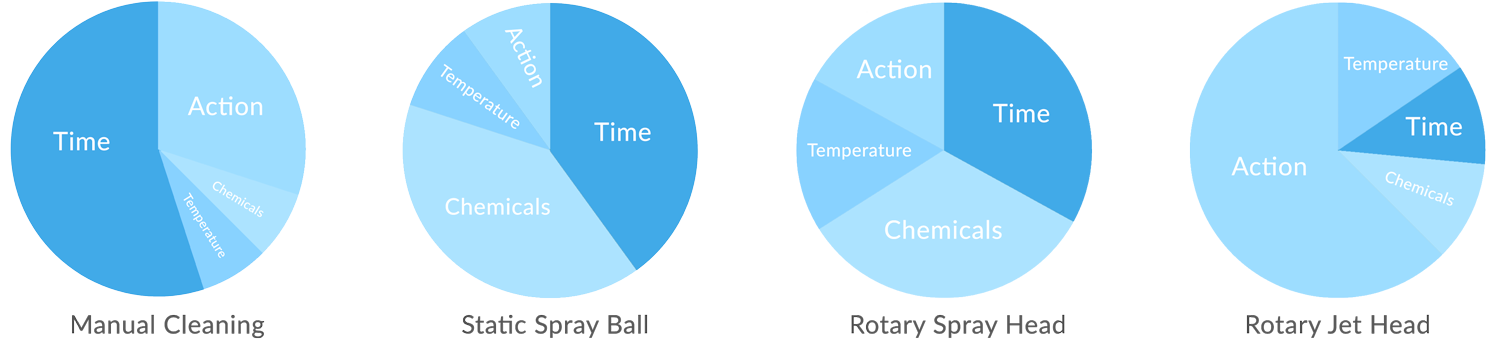
The pie graphs above illustrate various combinations of parameters. An increase in any one parameter decreases the other parameters.
TIME
The total amount of time it takes to run a complete cleaning sequence can include a number of different steps, such as preparation, programming, wash and rinse, and drying, but the critical time element of the cleaning process is the amount of time that cleaning solutions are in direct contact with soil. Longer contact times can equal better cleaning, but increasing impingement can also result in better cleaning in shorter cycles.
When time spent cleaning cuts into time spent producing saleable product, using a rotary jet cleaner reduces cleaning cycle times while ensuring that totes are clean and safe.
ACTION
The action in a cleaning process is the mechanical force of the cleaning solution that physically dislodges soil from the surface. The amount of impingement needed--and therefore jet devices and pressure required--are important considerations.
CHEMICALS
The right chemical cleaning agents in the right concentrations make a significant difference in CIP efficiency. The main job of chemicals in any CIP process is to enhance cleaning.
TEMPERATURE
Calculating the precise solution temperature is critical to effectively cleaning a system while at the same time reducing energy costs. Some studies have shown that for every one-degree reduction in CIP solution temperatures there will be nearly a 1% reduction in the energy needed to heat the fluid.
Higher solution temperatures can increase the effectiveness of chemicals and mechanical action and can also reduce the amount of time needed to clean properly. The temperature of each individual cleaning stage should be calculated and controlled as accurately as possible to conserve energy and avoid overspending.
To learn more about tank cleaning equipment, visit csidesigns.com/tank-cleaning.
ABOUT CSI
Central States Industrial Equipment (CSI) is a leader in distribution of hygienic pipe, valves, fittings, pumps, heat exchangers, and MRO supplies for hygienic industrial processors, with four distribution facilities across the U.S. CSI also provides detail design and execution for hygienic process systems in the food, dairy, beverage, pharmaceutical, biotechnology, and personal care industries. Specializing in process piping, system start-ups, and cleaning systems, CSI leverages technology, intellectual property, and industry expertise to deliver solutions to processing problems. More information can be found at www.csidesigns.com.