A Guide to Wall Penetration eBook
in Processing Environments & Other Applications
Download PDF VersionPenetration Applications
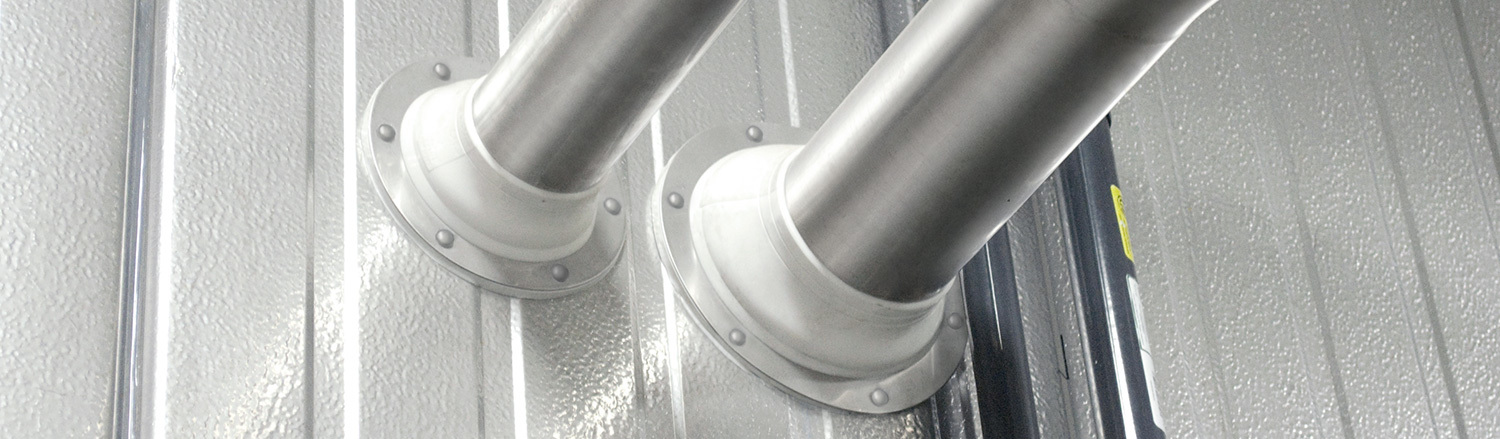
New Piping Installations
While not always possible, the best time to avoid many potential piping penetration problems in new installations is during the original construction of a project. To achieve advantages of pre-construction penetration design, coordinate with the contractor to determine the number, location, and size of penetrations. If penetration sleeves are being installed in concrete walls or floors, for example, they can be placed well before the concrete is poured. Incorporating openings into original construction eliminates the time, expense and mess associated with cutting holes in existing walls and floors.
To minimize the size of the gap between the barrier and the penetrant, make the openings just large enough to allow for vibration and thermal expansion or contraction of the pipe or tube. Minimizing the difference between piping diameter and opening diameter saves installation time and money by allowing you to use the smallest possible sealing device to cover the opening.
Escutcheon plates are easy to install onto new piping and provide an inexpensive, non-hygienic temporary cover for penetration gaps. The caulk or sealant required to make the actual seal for escutcheon plates will eventually cure to the point that it no longer adheres to the plate or barrier. The plate will then separate from the barrier and expose the gap.
The pliability of the food-grade silicone in flexible boots enables installers to stretch boots over the ends of pipe or tube easily and slide them into position as the piping is being installed. Once the piping is secured into place, the boot can slide down the piping until the pre-drilled base seats firmly against the barrier, then it can be anchored permanently in place. The flexibility of the boot allows the piping to move as needed without compromising the seal.
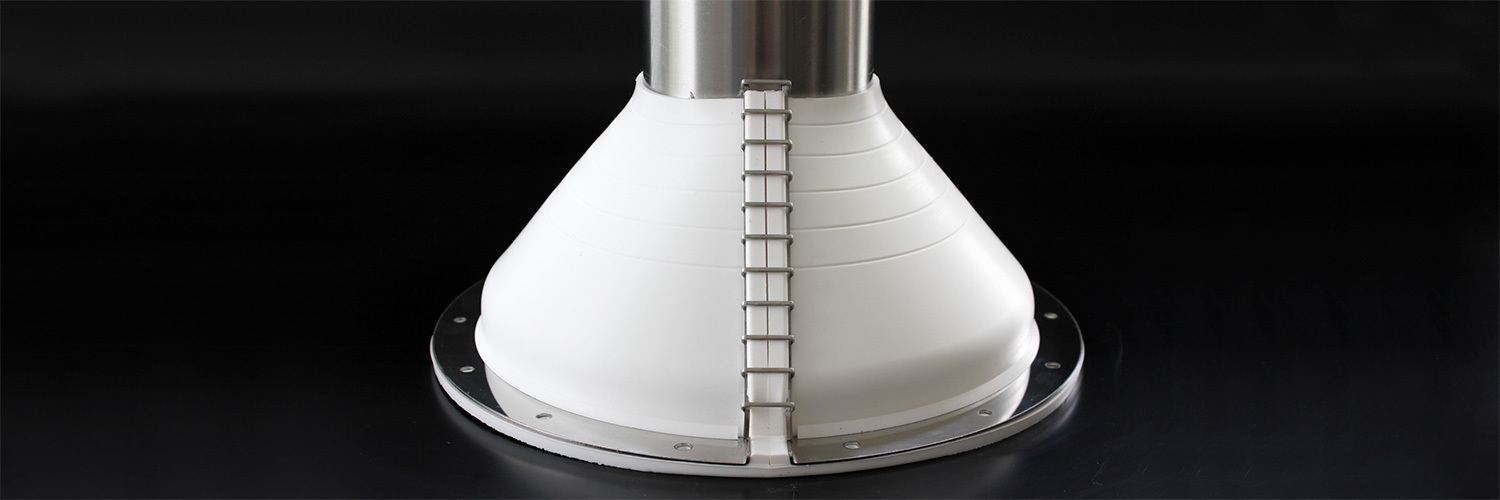
Existing Piping Installations
Sealing around existing piping penetrations can be a bit more problematic than sealing around new installations. With existing piping, you no longer have the advantage of being able to install the sealing device by simply sliding it over the end of the piping as it is being installed. Since the piping is fixed into position and can’t be removed from the opening, the seal has to encircle the piping, and then effectively be re-sealed once the piping is secured into place.
For existing pipes, a metal escutcheon plate must be cut into two halves and pieced together around the piping, or a single radial split must be made to allow the plate to bend enough to separate and wrap around the piping. In either case, cutting the plate creates an additional seam that must be sealed with caulk or sealant. Over time, vibration and curing can cause the sealant to separate from the plate and expose the seam, so additional applications of caulk or sealant are required periodically to maintain a secure seal.
Flexible sealing boots address the challenges of sealing around existing piping. The pliable silicone boot has the requisite split which allows it to be wrapped around the piping, the same as would be required with a metal escutcheon plate. The critical difference is that the two reinforced sides of the split seam are made of silicone elastomer that can be crimped together with a stainless steel staple. The result is a permanent, hygienic compression seal that doesn’t crack or separate over time.
Like flexible sealing boots, modular mechanical seal assemblies can be installed into existing piping penetrations but they should only be used in areas that do not require a hygienic design.
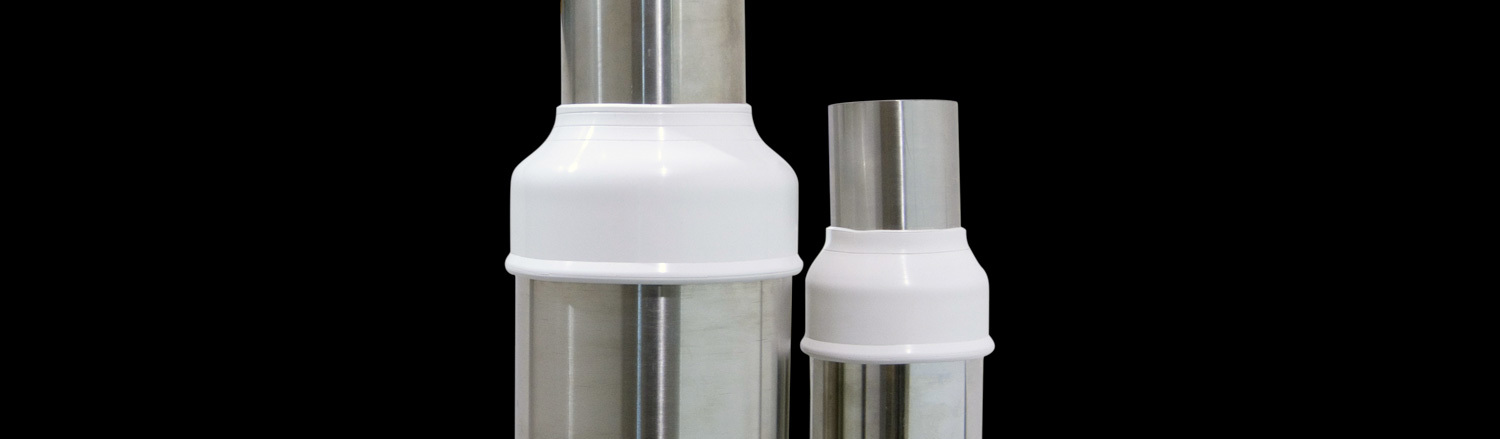
Tube-in-tube Transitions
Floor and ceiling penetrations often incorporate a section of pipe or sanitary tube in the opening as a sleeve to protect the process piping that runs through it. The sleeve serves as a kick-guard and gives the process piping sufficient room to move and vibrate without restriction. The gap between the floor sleeve (outer tube) and the process piping (inner tube) must be sealed to prevent unwanted particles, moisture or debris from falling through the gap. A tube-in-tube seal for this application must completely seal the gap and allow the inner tube to move and vibrate as needed.
The rigid design of metal escutcheon plates makes them ineffective as a tube-in-tube sealing device. They are, however, often used to cover the gap between the sleeve and floor decking since they can be welded or bolted into place without creating undue stresses on the process piping. The majority of commercially available flexible boots for transitioning from one piping size to another are engineered for plumbing applications on roofs, drains and sewers. Most boots don’t provide the hygienic design that is required in processing environments and are typically made from elastomers that do not have adequate resistance to high heat or cleaning solutions. They are molded in specific size combinations that can’t be altered in the field and are usually secured to the piping with a worm gear hose clamp.
Flexible sleeve boots made from hygienic white silicone provide the heat resistance and compatibility with cleaning solutions that is required in processing plants. They have a heavily reinforced lip seal that conforms to the diameter of the sleeve for easy, secure installation. The tapered cone end of the boot can be trimmed in the field to fit pipe and tube diameters. The silicone elastomer stretches tightly around the sleeve and process piping and has enough flexibility to allow movement while dampening vibration.

Fire Rated Applications
Combustible oils, explosive dusts and flammable liquids and gasses are some of the fire hazards that exist in many food and pharmaceutical facilities. Processing environments that contain potential threats to fire safety may be required to seal penetrations with some level of passive firestop that delay or prevent fire from passing through penetrations. The requirements for a proper penetration firestop are addressed in numerous standards and codes:
- Underwriters’ Laboratories UL 1479
- ASTM E814
- NFPA 101 and NFPA 70
- Life Safety Code
- National Electrical Code
- International Building Code
Most of the current standards require more than filling an opening with a firestop sealant. They require a complete system made up of a fire-rated barrier, the penetrating material and the firestop sealing agent. The fire codes for your facility are locally developed and enforced, so contact your local fire marshal or building code inspector to learn about requirements for your facility.
Many products specifically address firestop applications for various types of penetrations. These products range from complete multicomponent sealing systems to intumescent (heat expanding) sealants and pillows to fiberglass or mineral wool packing. Firestop approaches for food, dairy, beverage, or pharmaceutical penetrations should provide an appropriate level of fire protection and hygienically seal gaps to preserve a sanitary environment.
Stainless steel escutcheon plates are not fire-rated and they don’t provide a hygienic seal around penetrants, so they are not viable for sanitary environments. While flexible silicone boots don’t carry a fire rating, they properly seal penetrations that have been filled with approved firestop insulating products. Made of high-grade hygienic silicone, flexible boots are temperature rated up to 500° F and will effectively protect your sanitary environment from non-hygienic firerated materials inside penetrations.
Pressure Rated Applications
The majority of penetrations in processing plants don’t require a special pressure rating. The environments are generally open to atmosphere and only need a clean, reliable seal around the penetration to keep airborne particles, moisture or pests from moving through them.
If you do have a penetration application that requires a pressurerated solution, modular mechanical seals carry pressure ratings up to 40 psi or more. This rating typically meets or exceeds the performance requirements for most applications. But to be acceptable in a sanitary environment, the modular mechanical seal assembly has to be contained inside a hygienic seal like a flexible silicone boot so that the processing area is protected from the non-hygienic mechanical seal. The watertight silicone boot also protects the mechanical seal from potentially harmful cleaning solutions.