What is Stainless Steel eBook
This eBook provides engineers, purchasing agents, and plant personnel with a tool to enhance their knowledge of stainless steel and its uses as related to their present and future applications.
Download PDF VersionChapter 4
Chapter 4
Alloy Selection
When a corrosion problem is encountered, review the solution chemistry to determine if a change can be made to eliminate the corroding condition. For example, if carbon steel is rapidly oxidizing in steam, is it possible to adjust the pH upward and add hydrazine, or one of its derivatives, to combat the dissolved oxygen?
If the system is being cleaned with muriatic acid, which is dangerous to stainless steel, can the acid be changed to one more friendly to the stainless steel such as nitric, citric or sulfamic? If the pH is being lowered using carbon dioxide sparging and chloride pitting occurs, can a mineral acid such as sulfuric or phosphoric acid be substituted to prevent acid bubbles from forming on the surface causing crevice corrosion?
If it is not possible to modify the environment, the alloy must be changed. Use the following selection process to narrow down the alloy options. This same procedure can be used in selecting an alloy for the initial design.
- Review the nature of the environment with respect to chemical composition, temperature, pH, and velocity. Always assume the worst-case scenario. Use the corrosion rate charts or tables to determine those alloys with the best uniform corrosion resistance. If the solution is a single composition, selection will be rather easy.
If it is a complex solution of two or more components, determine the corrosion rates in each component individually. Keep in mind the corrosion rates may be accelerated or slowed down in each environment. Many complex solutions require the use of corrosion racks with different alloys exposed to a test environment to determine the best alloy.
- Always determine if chlorides are present. If they are-and they usually are-select the best alloy for pitting resistance as a function of pH and chloride content, using the chart in Figure 3 (above).
- Next, pick the proper alloy using its Pitting Resistance Equivalent Number (PREN) for the temperature based on crevice corrosion; see Figure 4 (above).
- Determine the best carbon range to prevent intergranular corrosion using Figure 6 (above), or use a low carbon grade as a general rule.
- Pick the best alloy that will not stress corrosion crack based on Figure 7 (above).
- Consider the metallurgical and mechanical characteristics of each candidate alloy. If you are not that familiar with each alloy and its limitations, contact a reputable and qualified material producer for assistance. Many tests have been conducted in many environments, and a wealth of information is available. There is an alloy, material or design modification out there that will solve your problem.
CONCLUSION
The correlation between metallurgical factors and corrosion resistance is straightforward. Inclusion of corrosion control and the correct material selection in the design process is the most efficient means of controlling corrosion and therefore high replacement costs, or catastrophic system failure.
If corrosion control is not considered in the design stage, the subsequent costs are usually much greater than the initial investment at the onset.
Reference Charts

(2) Pitting resistance equivalent number for stainless steels: PREN= %Cr+ 3.3[%Mo + 0.5(%W)] + 16%N
(3) Basler Norm 2
(4) Nominal composition
The reference of the PREN is not intended as an endorsement of corrosion resistance or any listed material. It is to be used as a reference only. It is recommended to contact a qualified corrosion engineer for guidance based upon the individual process conditions.
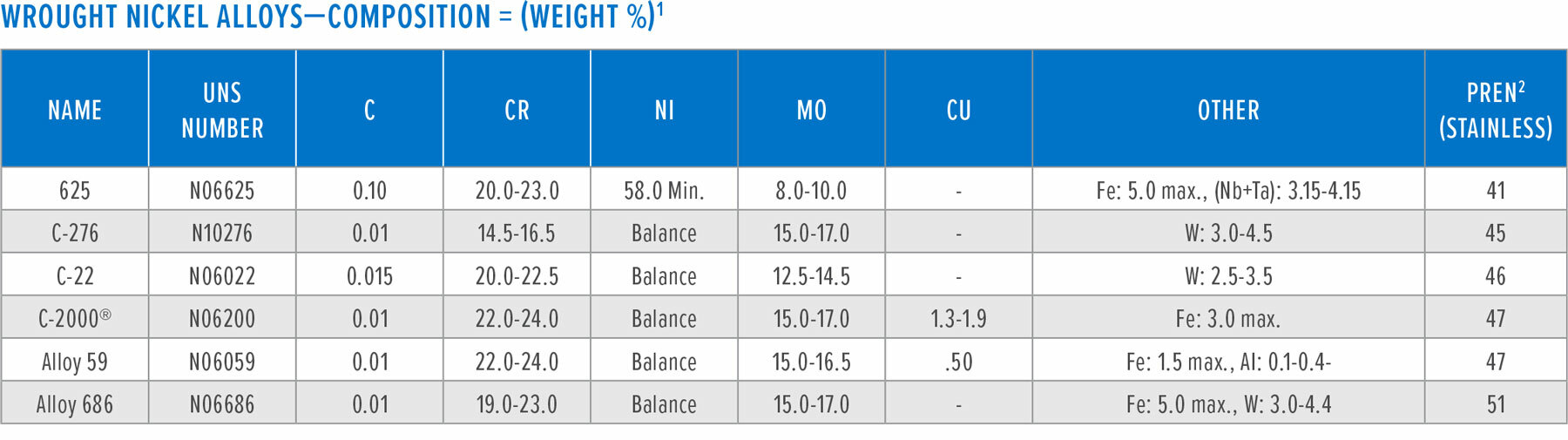
(2) Pitting Resistance Equivalent number for Ni-base alloys: PREN= %Cr+ 1.5(%Mo + %W + %Nb)
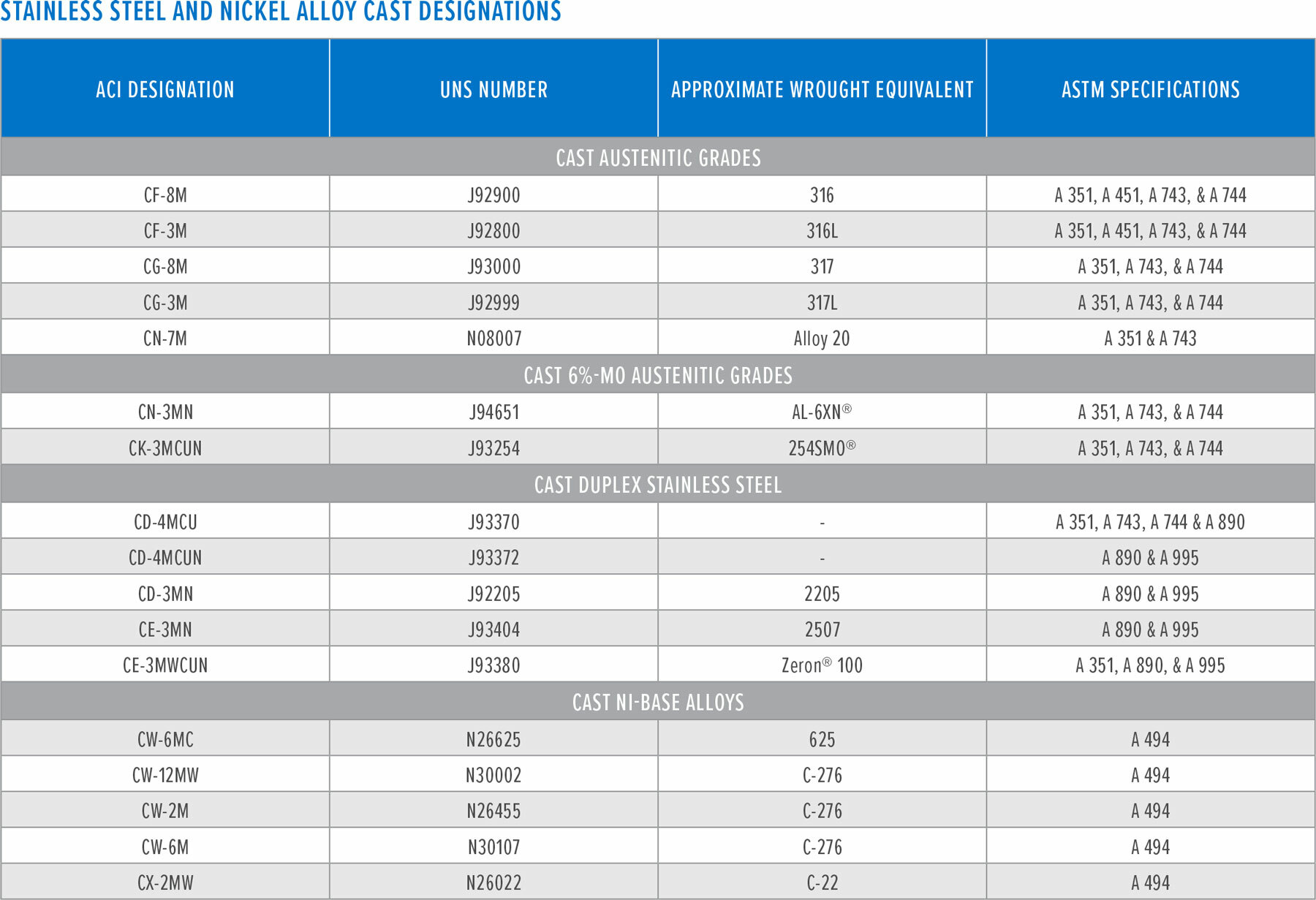
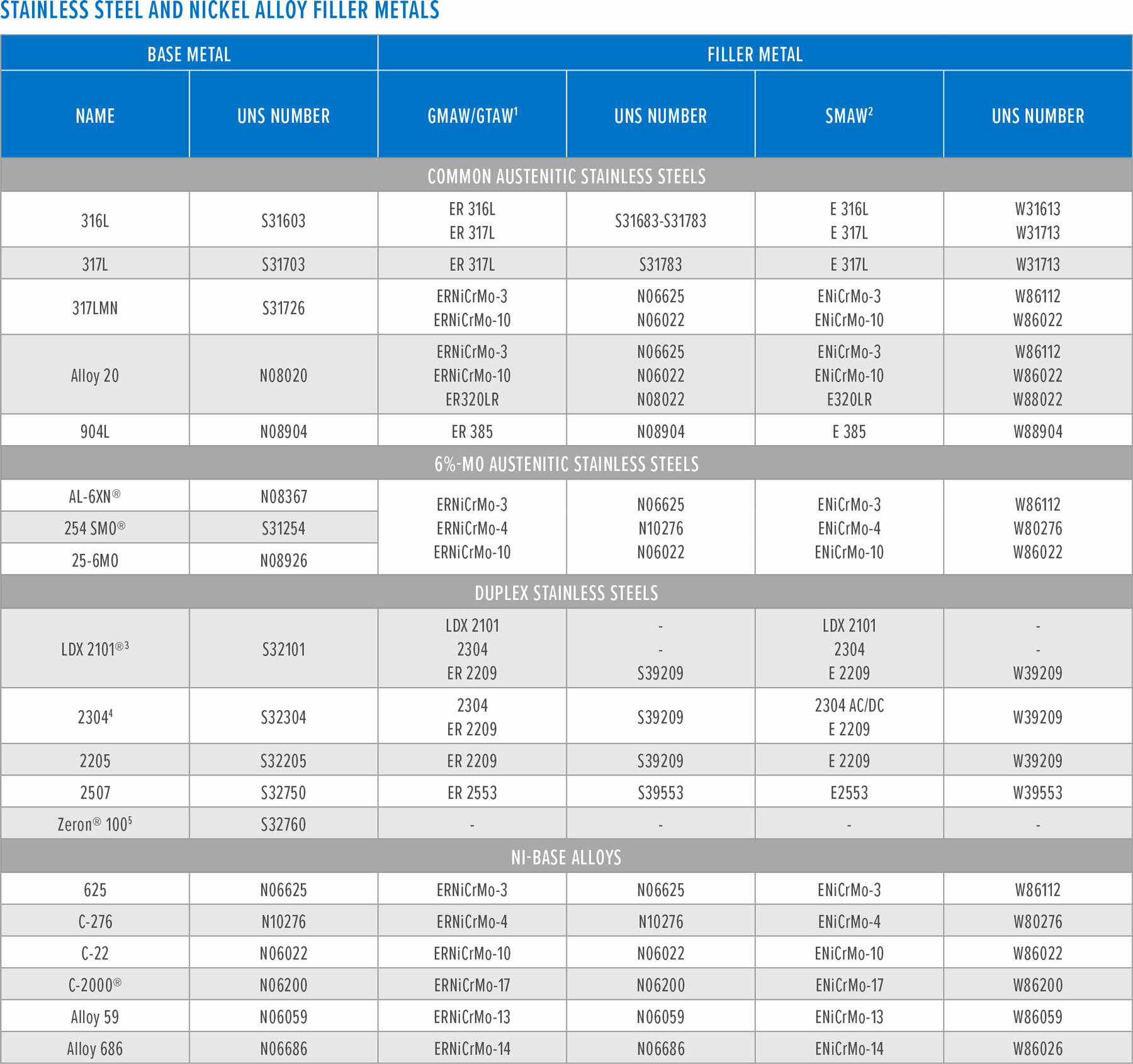
(2) The applicable AWS specification for Stainless Steel Electrodes for Shielded Metal Arc Welding, e.g., E316L, is AWS A5.4. The applicable AWS specification for Nickel and Nickel-Alloy Welding Electrodes for Shielded Metal Arc Welding, e.g., ENiCrMo-3 is AWS A5.11.
(3) Proprietary bare wire and electrodes, LDX 2101 and 2304 also used for welding 2101LDX.
(4) Proprietary bare wire and electrodes, 2304 also used for welding 2304.
(5) There are no AWS filler metal designated welding products for welding Zeron 100. The manufacturer recommends filler metals available from Lincoln Electric and Metrode Products, Ltd. Consumables for welds left in the “as deposited” condition are designated as “X” grades, i.e., Zeron 100X.