Pipe Fabrication: Vital Guide to Sanitary & Industrial Piping
Pipe fabrication is a critical aspect of many industrial projects, with many pipe fabrication tasks requiring precision and expertise to ensure the integrity and functionality of the piping systems. The pipe fabrication process is complex and involves various stages, from initial planning to execution, each requiring adherence to strict specifications and regulations.
In this article, we will explore the different pipe fabrication methods, including shop and field fabrication, and the specialized tools and equipment used to fabricate pipe in each method.
Top 4 Things to Know About Hygienic Pipe Fabrication
This article will provide a bird’s eye view of the issues involved in the design and fabrication of the pipe and tube systems that are ubiquitous in the sanitary processing industries, including & beverage processing and biopharmaceutical manufacturing. Pipe systems carry gases, liquids, and solids throughout process plants, conveying both products and utilities (cleaning fluids, water, steam) from one location to another. Apart from equipment, they are the second most expensive component to be found in these types of plants and must be properly designed and fabricated to ensure product quality control, operating safety, and overall plant efficiency. Various pipe fabrication tools, such as pipe clamps and supports, are essential for fitting flanges and pipes, ensuring precision in manufacturing and assembly.
In this blog we will discuss the top four things to know as it relates to US pipe fabrication.
We’ll look first at how sanitary pipe and tube systems are designed, taking into account fluid properties in the products being transported, as well as other pipeline system design considerations such as:
- Physical space limitations
- Access for maintenance
- Clean-in-place (CIP)
- Steam-in-place (SIP)
- Clean-out-of-place (COP)
- Drainage
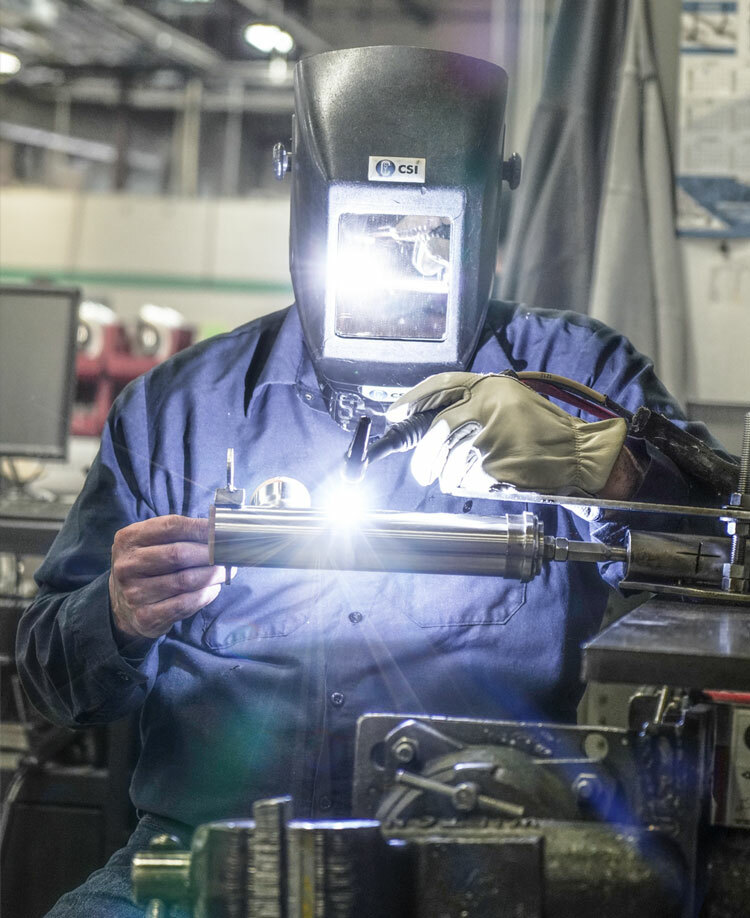
Next, we’ll look at what materials sanitary pipeline systems are made from, as well as where and how they’re constructed. Then, we’ll discuss how sections of sanitary tubes are joined together, exploring the relative advantages and disadvantages of threaded, flanged (e.g., Tri-Clamp), and welded connection approaches.
Next, we provide an overview of the myriad of sanitary connector types used to join pipe sections together (elbowstees, crosses, Y-bends, caps, and reducers). Finally, we’ll end with a brief review of additional items to consider when designing and installing sanitary pipe systems, including pipe and tube support and insulation.
1. How Sanitary Pipe and Tube Systems Are Designed
Sanitary process tube networks are complex systems that are generally considered to include the complete interconnection of pipes and their components, including pipe connectors and other fittings and equipment such as pumps, tanks, and valves.
Let’s start with some definitions. While we’ll use both the terms “sanitary pipe” and “sanitary tube” interchangeably in this article, the vast majority of the piping material used in sanitary processing systems is sanitary tubing.
- Sanitary tubes have thinner walls than pipes, and are more suitable for achieving a cleanable, autogenous, single-pass TIG weld when sections of material are joined together.
- Sanitary tubes are also mechanically polished on their inside surfaces for more effective cleaning.
Improved cleanability is the primary reason why sanitary tubes are preferred over pipes in hygienic processing applications.
Each sanitary process piping system is unique and must be tailored to both its site and application. Therefore, the system’s initial design begins with developing the requirements for transferring a product from one point to another. In this analysis, process engineers must determine fluid properties, including:
- Temperature
- Pressure
- Viscosity
- Corrosiveness
- Desired flow rate
- Allowable pressure and temperature drop or loss
- Needs for CIP and SIP
- Space limitations
In addition, they must determine other specific process requirements such as free drain or straight pipe runs to accommodate pumps or other components. Supports for these systems also often require a significant design and pipe fabrication specification effort. Pipe fabrication specifications are crucial at this stage to ensure all guidelines for detailed shop drawings, fabrication requirements, and applicable codes and standards are met.
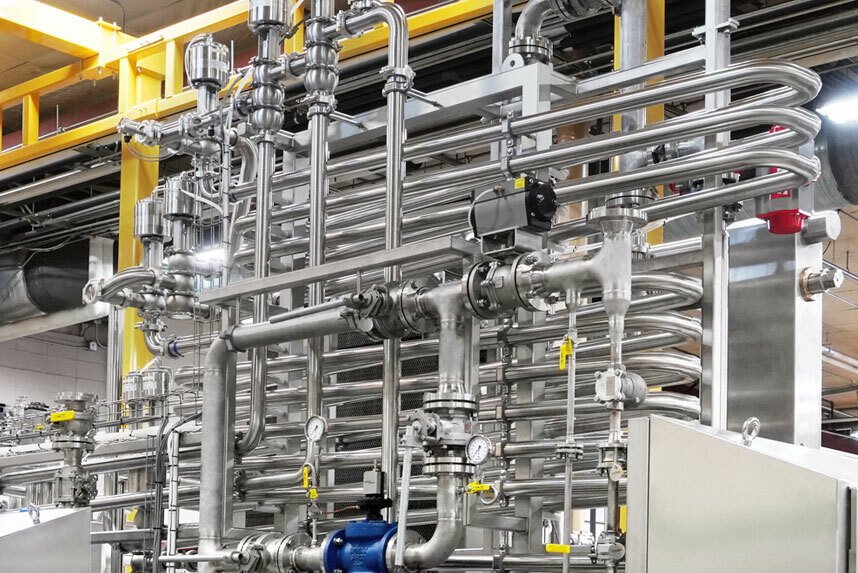
Properly engineering and installing a hygienic piping system helps a manufacturer produce high-quality, consistent products, while allowing for efficient and effective Clean-In-Place of their system.
~ Paul Marcink, Director - Installations Services, Central States Industrial
In developing these finished specifications for a sanitary process tubing system, process engineers create two engineering design documents, defined below:
- Process Flow Diagram (PFD) - shows the relationship between the major pieces of equipment in the product flow system such as pumps, tanks, heat exchangers, etc., and the piping systems to and from the significant pieces of equipment.
- Piping and Instrument Diagram (P&ID) - shows all major pieces of equipment and system components; tubing details (service, size, specs, rating, insulation, etc.); instrumentation details (all pressure, temperature, and flow instruments required, control and safety pressure valves, meters, etc.); and the actual pipe routing conditions (such as free flow, slope, the maximum length of pipe runs, etc.)
While both documents are critical to the sanitary pipe system design effort, the P&ID is the primary document utilized by process engineers for material procurement and determining pipe routing.
Process piping system design must also include a stress analysis to ensure that pipe and tube routes, nozzle loads, hangers, and supports are properly placed and selected. This analysis confirms the allowable pipe stress is not exceeded under different conditions, including operating loads, pressure testing, etc. This stress analysis is governed by the various international agencies that regulate the hygienic processing industries. Various pipe fabrication tasks, such as pipe cutting methods, welding, and assembling, are essential to ensure the system's integrity and compliance with these standards.
Industry-specific design requirements exist for process tubing systems in each of the different sanitary processing industries. Critical requirements for engineered piping systems in each of these industries are described below:
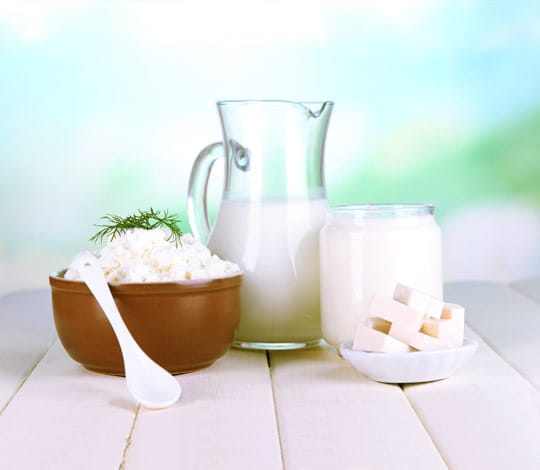
Dairy Industry
- Product tubing must be stainless steel, either 304 or 316L components.
- Permanent welds are the preferred method for connecting pipes.
- When removable connectors are necessary, a clamped union with a joint gasket is typically specified.
- All lines must be polished to a minimum of a 150-grit surface and passivated.
- All process lines must be designed to eliminate dead legs or traps where products might stagnate.
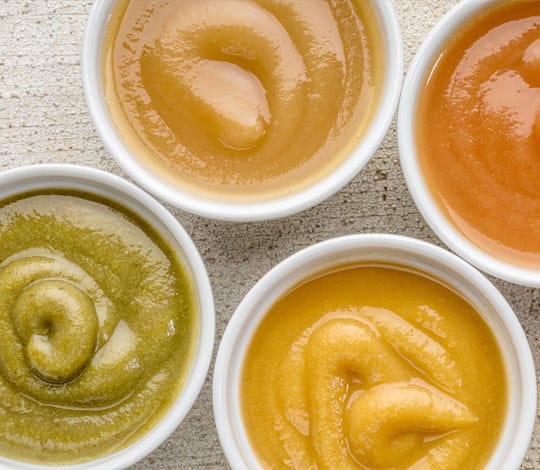
Food & Beverage Processing Industry
- Product pipes are made from 304 and 316L stainless steel.
- Inside surfaces should be passivated.
- Welding is the preferred method for connecting both pipes and tubes.
- Use the fewest number of connections between pipes and tubes to reduce system maintenance requirements.
- All pipes and tubes must be designed for drainability and cleaning.
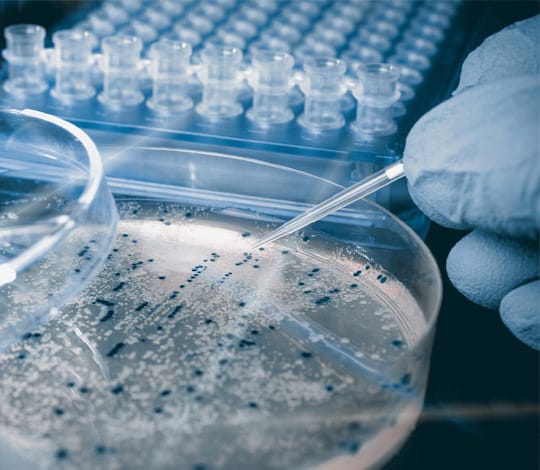
Biopharmaceutical Manufacturing Industry
All piping must be fully drainable, cleanable, and capable of being sterilized.
- Automated orbital welding is the preferred type of weld for joining pipes and components. The importance of welding piping components to meet specific design requirements cannot be overstated, as it ensures system integrity and minimizes accidents.
- Pipes need to be made of 316 or 316L stainless steel.
- Inside surfaces are often specified as electropolished.
- All product contact components/materials used must meet BPE (Bioprocessing Equipment) industry standards.
Due to the complexity in adequately designing and fabricating sanitary process pipe and tube networks, CSI offers complete design and engineering services that couple 3-D scanning capabilities with CAD data integration.
We’re here to help solve specific hygienic process issues, optimize existing processes, and develop new systems. CSI is also an expert in sanitary pipe welding, custom pipe and piping fabrication, and quality sanitary surface finishing. From mechanical fabrication, precision machining, sheet metal fab, electrical panel shop, automation and assembly services, we offer custom solutions, precision craftsmanship, and consistent manufacturing results.
2. What Materials Sanitary Pipe and Tube are Made From
Sanitary process piping used in the dairy, food & beverage processing, and biopharmaceutical manufacturing industries must be made from specific materials suitable for producing products under sanitary conditions. Pipes and tubes that carry product flows must be made from corrosion-resistant metal alloys such as stainless steel in compounds 304, 316, and 316L.
AL-6XN® and Hastelloy C-22 are utilized in some product applications involving highly corrosive ingredients. Steel unable to withstand corrosive materials are not acceptable for product-carrying applications. However, pipe fabricators may use these materials in pipes and tubes carrying utilities such as steam. The choice of pipe material plays a crucial role in determining whether the fabrication occurs in a shop or in the field.
Process pipes and tubes used in sanitary processing systems are either fabricated in a field pipe fabrication shop or in the final field location in which they’re to be installed. While some piping spools can be pre-fabricated from isometric tubing drawings in a shop, most pipes and tubes for a custom process pipe system are fabricated in the field. The pipe fabrication shop is essential for assembling and welding fittings and components into spool assemblies, which are then transported to construction sites for installation. To this end, various specialized tools are used in the final assembly of pipe networks at the installation site, including pipe jacks, pipe rollers, pipe cutting and bending equipment, tube facing machines, grinders, and welders (GTAW/TIG manual and automatic orbital).
In particular, using a GTAW/TIG welding process using proper gas purging protocols is a requirement for permanently welded sanitary processing systems. This process produces a consistent, cleanable, high-quality weld when performed by a skilled craftsman.
3. Methods of Joining Sanitary Pipes and Tubes: Pipe Welding Planning
Regardless of the method used in joining together sections of sanitary pipes, there are some general requirements common to all:
- The pipe connections must be leak-proof. Leaks pose several problems. If process fluids leak out of a pipe joint, contaminates can get in. Additionally, leaking fluids can pose a safety hazard to plant personnel. Product loss from leaking connections is also an issue.
- Like the pipes themselves, connectors (also called ferrules) must be constructed from an approved material such as austenitic stainless steel or a noble alloy such as AL-6XN or Hastelloy.
- Sanitary connectors must have a smooth and polished surface on all surfaces exposed to the product. 32 is the minimally acceptable Roughness Average (or RA) that is allowable for a connector to be deemed sanitary. In certain applications — primarily in biopharmaceutical manufacturing — the surface exposed to the product is often electropolished.
Socket welded pipes are typically fabricated in the field.
There are several types of connection methods that are approved for use with pipes and tubes in the sanitary processing industries. Each is described in the paragraphs below.
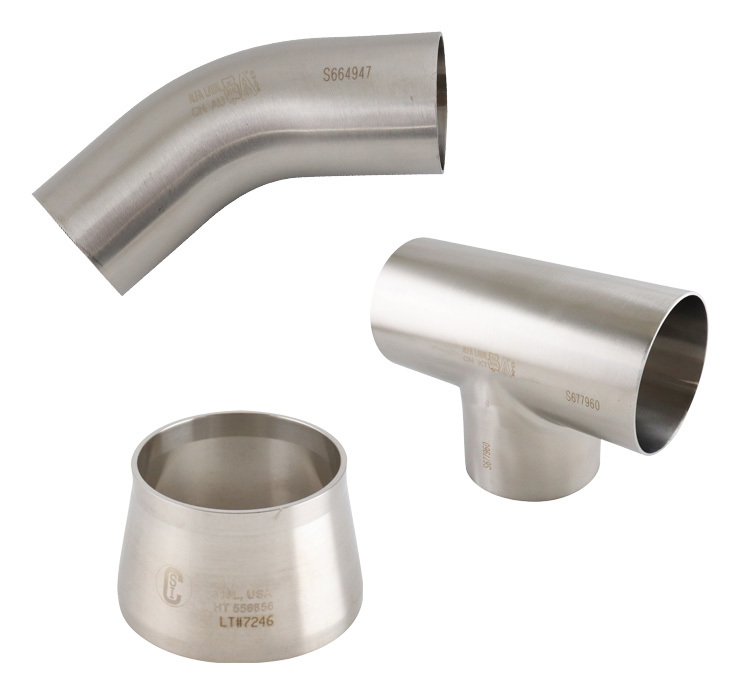
Butt Welding
Butt weld fittings are welded into the piping process using an autogenous TIG welding process.
Butt weld fittings are very robust and cost-effective. Due to the variety of standard shapes that are available, they allow for process pipe networks to be configured in various ways.
However, since this type of connector is welded into place, the butt welded pipes and connectors cannot be disassembled. Therefore, the pipe and tube networks must be cleaned using CIP methods. Butt welding the components also helps reduce the maintenance costs of a tubing system. Simply put, reducing the number of ferrule connections in a pipe network reduces the number of gaskets that personnel must replace regularly.
Tri-Clamps
Tri-Clamp connector unions are comprised of two flanged ends, a gasket, and a clamp used to secure the connector.
Tri-Clamps are popular stainless-steel fittings found in more than 2/3rds of sanitary process pipe and tube installations. Tri-Clamps are more easily disassembled than other types of removable fittings. They're designed to be cleaned-in-place but may also be disassembled for further cleaning, inspection, and repair.
To assemble the Tri-Clamp, the two faces of the connector are mated with a gasket in-between and then tightened with the clamp. For proper installation, the gasket must be completely seated into the seats in both flange faces. Incorrect alignment is one of the leading causes of leaks in these connector types.
Also, over-tightening the connector may cause the gasket to bulge and protrude into the process piping, creating locations for bacteria and other contaminants to build up. Over-compression of the gasket can also cause pieces of it to break off and get into the product stream.
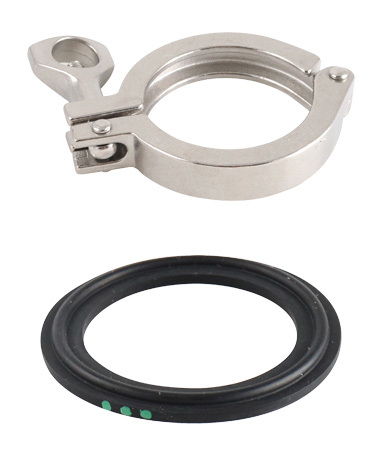
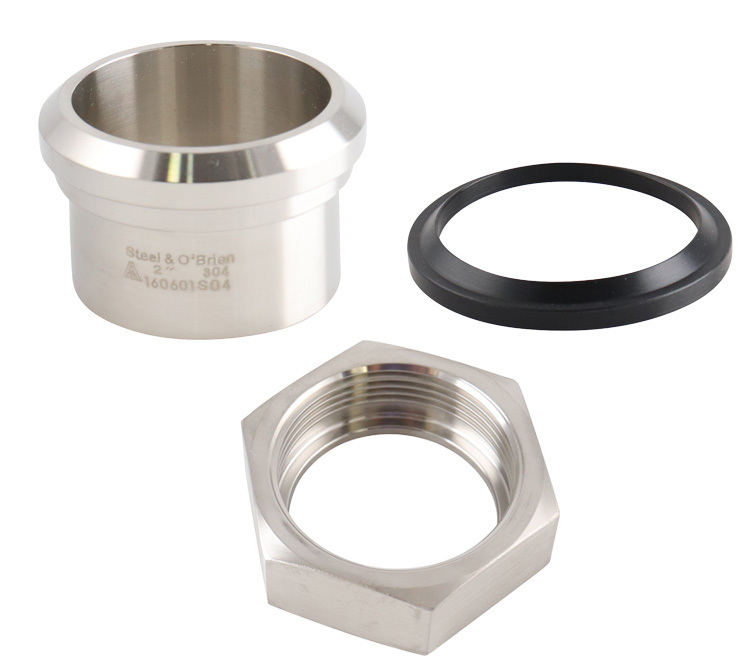
Bevel Seat Fittings
These three-piece fittings are comprised of a threaded nut, a plain end with an internal gasket taper, and a threaded end piece.
Bevel seat fittings are another type of sanitary fitting commonly used in connecting sanitary pipes and tubes sections.
Bevel seat fittings are commonly used in the food, beverage, and dairy industries for joining pipes and tubes and are available in 304 and 316L stainless steel alloys. Care must be used when installing these types of connectors. It is relatively easy to strip the threads when they're tightened or set them too tightly and seize the connector.
4. Common Types of Connectors Used in Sanitary Pipe Systems
There are various standard types of connectors or fittings used in the sanitary processing industries to form pipe networks, joining together pipes and tubes using one of the methods described in the previous section. Each of these is described in the paragraphs below.
Various pipe fabrication tasks are involved in assembling these connectors, including cutting, welding, and fitting, which require specific tools and equipment to ensure proper execution in both workshop and field environments.
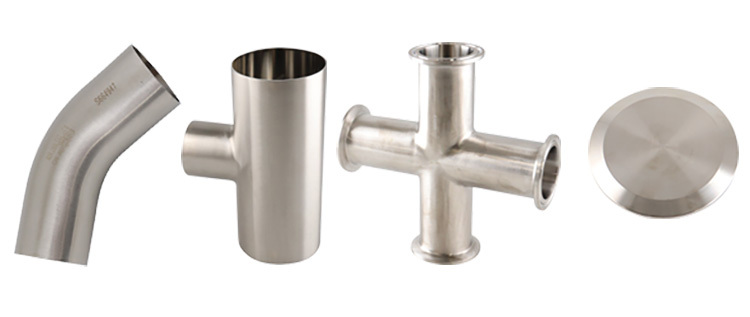
Elbows, Tees, Crosses, and End Caps
These are the most commonly used types of sanitary fittings.
- An elbow is a fitting used between two pipe sections to allow a change in the direction of the pipe run (typically available with either a 45° or 90° bend).
- Tees and crosses are used to connect two or more flows of the piping system.
- End caps are used to seal off the end of a pipe run or close off open ports on equipment.
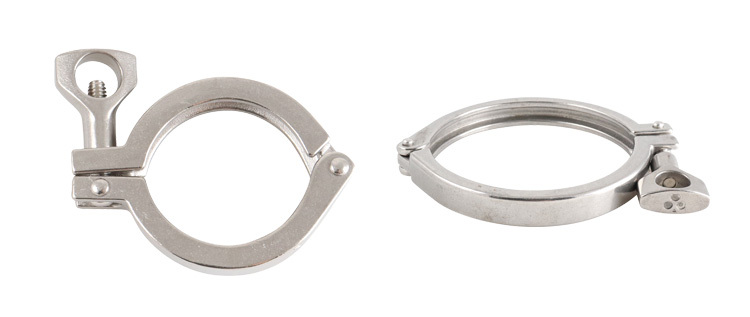
Clamps
- Clamps are used in tri-clamp fittings to join the components together.
As the clamp's wing nut is tightened, the Tri-Clamp's ferrules are joined together, compressing the gasket between them and forming a leak-proof connection.
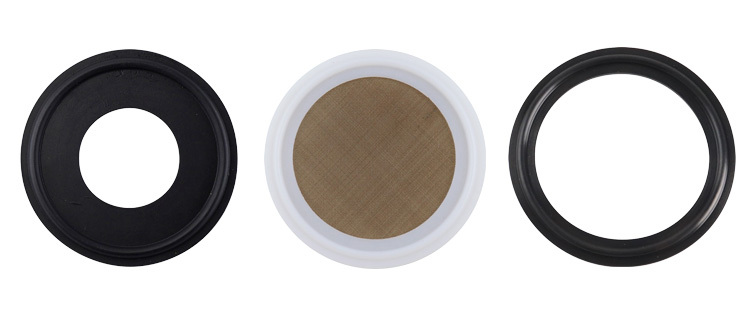
Gaskets
- Gaskets are mechanical seals (typically rings) that fit into a space between two pipe connectors, preventing leaks between the pipes when the fitting that joins them is tightened.
Additional Considerations: Pipe Fabrication Tools
Two other items are essential to consider when talking about sanitary pipe and tube installations, namely, pipe supports and pipe insulation.
Pipe bending is typically a process associated with shop fabrication.
1. Pipe Supports
Sanitary pipe and tube networks must be supported in such a way so that:
- The combined weight of the pipes and the products they carry do not cause the line to sag.
- Allowing for movement of the pipe due to expansion and contraction.
Various hanger types are used in supporting pipe systems, including straps, clamps, and U-bolts.
2. Pipe Insulation
Many sanitary process pipe networks carry fluids that are hotter or colder than the surrounding environment and must be insulated. Materials suitable for insulating sanitary pipe or tube networks exhibit the following qualities:
- A high-insulation value
- Long life
- Vermin-proof
- Non-corrosive
- Ability to retain shape/insulating value when wet
- Easy to install
- Wash-down rated
Materials suitable for sanitary process tubing insulation include diatomaceous silica, asbestos, calcium silicate, cellular glass, magnesium carbonate, glass fiber, and certain plastic foams.
Next Steps
As we’ve shown in this article, designing and fabricating sanitary process pipe and tube networks is quite complex and governed by a number of industry “best practices,” as well as regulatory industry standards.
Adhering to pipe fabrication specifications is crucial to ensure that all pipes and fittings are manufactured and assembled correctly throughout the detailed pipe fabrication process, regardless of project size.
Each pipe system is unique and must be designed for both the materials carried and the nature of the space in which it is installed.
CSI is a recognized expert in both design and fabrication work for the sanitary process piping systems found in the dairy, food & beverage processing, and biopharmaceutical manufacturing industries.
We’re here to help. Call us at (417) 831-1411.
Contributing Author
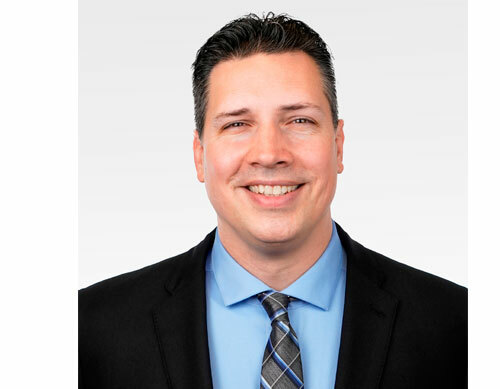
Paul Marcink is the Director of Site Services for CSI’s Installation and Service teams. Paul received his M.S. degree in Project Management and B.S. degree in Drafting and Design Technology from Missouri State University in Springfield, Missouri, and brings over 24 years of experience in engineering, designing, fabricating, installing, and maintaining process piping and equipment in the food, beverage, dairy, pharmaceutical, and biotech markets. Paul focuses on leading a team of highly-skilled individuals with passion to help customers achieve their goals.
ABOUT CSI
Central States Industrial Equipment (CSI) is a leader in distribution of hygienic pipe, valves, fittings, pumps, heat exchangers, and MRO supplies for hygienic industrial processors, with four distribution facilities across the U.S. CSI also provides detail design and execution for hygienic process systems in the food, dairy, beverage, pharmaceutical, biotechnology, and personal care industries. Specializing in process piping, system start-ups, and cleaning systems, CSI leverages technology, intellectual property, and industry expertise to deliver solutions to processing problems. More information can be found at www.csidesigns.com.